The amine treating process is a crucial component of refining operations, specifically designed to remove hydrogen sulfide (H2S) and other acid gases from off-gases in the refinery. By employing a 20% diethanolamine (DEA) solution, the process ensures that treated gas meets the required purity standards, typically not exceeding 100 mol ppm H2S. The amine treating process is instrumental in gas purification and sulfur recovery, making it an essential unit in oil and gas refineries.
Process Chemistry
The amine treating process operates on a reversible chemical reaction principle. Hydrogen sulfide, a weak acid, ionizes in water to form hydrogen and sulfide ions:
H2S ⇌ H+ + HS-
Similarly, carbon dioxide (CO2) undergoes a comparable reaction:
CO2 + H2O ⇌ H+ + HCO3-
Diethanolamine (DEA), a weak base, ionizes in water to form amine ions:
(HOCH2CH2)2NH + H2O ⇌ ((HOCH2CH2)2NH2+) + OH-
When H2S dissolves into the amine solution, it forms a weakly bonded salt:
(HOCH2CH2)2NH2+ + HS- ⇌ (HOCH2CH2)2NH2SH
This equilibrium reaction enables the continuous absorption and regeneration of the amine solution, making the process highly efficient for removing H2S and CO2 from hydrocarbon streams.
Importance of Amine Treatment in the Industry
Amine treatment is essential in natural gas processing, petroleum refining, and petrochemical plants. It ensures that gases meet environmental and safety standards by reducing H2S and CO2 concentrations before they are released or used further. Failure to remove these acid gases can lead to equipment corrosion, environmental hazards, and operational inefficiencies.
The use of amine treatment also plays a significant role in carbon capture and storage (CCS) technologies, helping reduce greenhouse gas emissions by efficiently capturing CO2 before it enters the atmosphere. With global concerns about climate change, amine-based carbon capture is being explored as a viable solution for sustainable industrial operations.
Key Operating Variables in Amine Absorption
For optimal H2S removal, certain process conditions must be maintained:
- Low Temperature – A lower temperature enhances the absorption efficiency. However, the lean amine temperature must be at least 3°C higher than the gas feed to prevent condensation of hydrocarbons.
- Low Acid Gas Loading – The reaction must be maintained in the forward direction by controlling H2S loading in the rich amine. Typically, total acid gas loading should not exceed 0.3–0.4 moles per mole of amine.
- High Amine Concentration – The recommended DEA concentration is 20 wt% for optimal absorption efficiency and minimal operational issues.
- Proper Contact Time – The gas and amine solution must be in contact for an adequate duration to maximize the absorption efficiency.
- Absorber Efficiency – The number of trays or packing material inside the absorber impacts the overall efficiency of gas treating.
Key Operating Variables in Amine Regeneration
Regeneration of the amine solution involves reversing the absorption reaction to release H2S:
(HOCH2CH2)2NH + H2S ⇌ (HOCH2CH2)2NH2SH
To achieve efficient regeneration, the following parameters must be optimized:
- High Temperature – Increasing temperature promotes H2S release but should be kept below 125°C to prevent thermal degradation of DEA.
- Low Pressure – The stripping column should be operated at the lowest possible pressure (0.35–1.0 kg/cm²G) to facilitate H2S removal.
- High Stripping Steam Rate – Steam assists in separating H2S from the amine solution. A heat input of 120–140 kg steam per cubic meter of amine ensures effective stripping.
- Proper Column Design – The design and efficiency of the regenerator column impact the effectiveness of amine regeneration.
- Reflux Control – Proper reflux management ensures that the amine regeneration process remains stable and efficient.
Process Description of the Amine Treating Unit
The amine treating unit operates in multiple stages:
- Gas Treatment – Sour fuel gas from the gas concentration unit is fed into the amine treating section. The gas first enters a knockout drum to remove liquid hydrocarbons before flowing into the fuel gas amine absorber.
- Absorption – Lean DEA is introduced into the Amine absorber to remove H2S from the gas stream. The treated gas is then sent to the refinery fuel gas system. The regenerated lean Amine is also supplied Amine Scrubbers located in Hydropressing units (Hydrotreating and Hydrocracking) in petroleum refinery.
- Rich Amine Handling – The H2S-rich amine solution is collected and sent to the rich amine flash drum, where hydrocarbons are separated.
- Regeneration – Rich amine is heated in an exchanger and sent to the amine regenerator, where H2S is stripped off, regenerating lean amine.
- Amine Storage & Filtration – Lean amine passes through mechanical, carbon, and sock filters to remove impurities before being reintroduced into the absorber.
- Sulfur Recovery – The stripped H2S gas is sent to the sulfur recovery unit (SRU) for further processing.
- Water Balance Management – Controlling water balance ensures that amine concentration remains optimal and prevents excessive dilution or buildup.
- Hydrocarbon Skimming – Hydrocarbons collected from the rich amine flash drum must be periodically removed to avoid contamination.
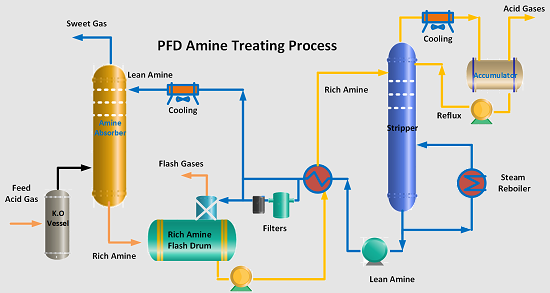
Challenges and Optimization Strategies
While amine treatment is effective, several challenges may arise, including:
- Foaming Issues – Caused by hydrocarbon contamination, foaming can reduce efficiency and lead to operational disturbances. Regular monitoring and use of antifoaming agents can help.
- Corrosion Risks – Due to acidic compounds and excessive heat, corrosion of equipment is a common issue. Proper material selection and corrosion inhibitors mitigate this problem.
- Heat Management – Regenerator temperature control is critical to avoid thermal degradation of amines.
- Solvent Losses – Continuous monitoring of amine losses through evaporation or degradation ensures cost-effectiveness.
- Environmental Compliance – Stricter environmental regulations require continuous monitoring and process improvements to ensure compliance with emissions standards.
Optimization strategies include:
- Regular Monitoring and Testing – Routine analysis of lean and rich amine compositions helps maintain operational efficiency.
- Efficient Process Control Systems – Automated control systems enhance precision in flow rates, temperatures, and pressures.
- Proper Equipment Maintenance – Scheduled maintenance reduces downtime and prolongs equipment life.
- Use of Alternative Solvents – Research is ongoing to develop advanced solvents with lower energy requirements and higher selectivity for acid gas removal.