The process of transferring a substance from one solvent to another due to differences in solubility or distribution coefficient between the two immiscible (or slightly soluble) solvents is known as the solvent extraction process. The solvent extraction technique has been considered an effective separation method due to its ease, simplicity, speed, and broad scope. The solvent extraction process is a physical separation method that is used in all conventional lube plants.
The solvent extraction process produces high-quality lubricating oils characterized by good thermal and oxidation stability, light color, and a good additive response. The byproduct extract phase produced in the Solvent Extraction Unit is rich in aromatics and is used as a carbon black feedstock, rubber extender oils, and many other non-lube uses.
In solvent extraction, also known as Liquid-liquid extraction (LLE) or partitioning, a mixture of two components treats with a solvent that preferably dissolves one or more of the components in the mixture. The raffinate is the treated mixture and the desired product, while the solvent-rich phase is the extract. The solute is the component transferred from the raffinate to the extract, while the diluent is the component left behind in the raffinate. The solvent in the extract that leaves the extractor is usually collected and reused.
The feeds to the Solvent Extraction unit are vacuum distillate cuts such as spindle, light neutral, intermediate neutral, heavy neutrals, and bright stock which is produced from the propane deasphalting of vacuum residue.
These feeds are suitable for the production of LOBS (Lube Oil Base Stock). The finished lube oils are obtained by blending metallic soaps and additives along with the lube oil base stocks. More than half the lube oil supply today comes from these solvent processes.
The conventional method for improving the viscosity index of the oil is solvent extraction, which involves partially removing the aromatic hydrocarbons, which are high-viscosity and low-viscosity index components. The solvent extraction process also removes undesirable components such as compounds containing heteroatoms such as oxygen, nitrogen, and sulfur, present in vacuum distillates and residual stocks.
Many refineries also use the solvent extraction process also known as the solvent refining process to manufacture lubricants and petrochemical units used to recover propylene, benzene, toluene, and xylenes for further processing into polymers.
Solvents for Solvent Extraction Process
Solvents such as phenol, furfural, and nitromethyl pyrrolidone (NMP) are often utilized in refineries. These solvents have a strong affinity for aromatic hydrocarbons, which dissolve and generate a distinct layer or phase known as an extract. The processed feedstock, the pollutants present, and the finished product requirements all affect the selection of specific processes and chemical agents. Solvent needs to be available at a reasonable price, safe for the environment, and non-corrosive to construction materials.
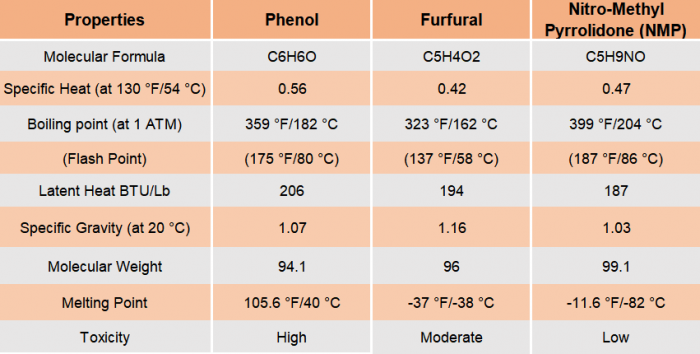
Description of Solvent Extraction Process
The Solvent Extraction Process flow chart is sown below.
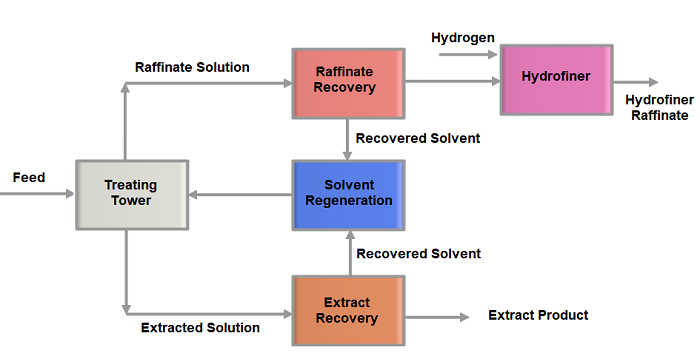
- The lube feedstock and the solvent are contacted in a trayed column counter currently. There are several types of continuous treater tower designs used in conventional lube plants. These include trayed towers, packed towers, and rotating disk contactors. The treater tower internals are designed to promote contact and separation of the oil and the solvent phases
- The uprising stream is gradually lean with aromatics and rich with paraffins and other non-aromatics and finally emerges as the raffinate stream from the tower top. Not all of the Aromatics removal is desired from the feed. Therefore, the removal of aromatics is carefully selected based on the required adjustment of the viscosity and viscosity index of the final product.
- The Raffinate stream exits from the top of the tower and is routed to a solvent recovery section for the separation of solvent from this stream. The solvent is separated from the primary raffinate by vacuum flashing and steam stripping under the vacuum.
- The extract stream containing the bulk of the solvent exits the bottom of the extraction tower and is routed to the recovery section for the removal of solvent from this stream. The solvent is separated from the extract phase by multiple effect evaporation at various pressures followed by vacuum flashing and steam stripping under vacuum.
- The overhead vapors from steam, strippers are condensed and combined with solvent condensate from recovery sections and are distilled at low pressure to remove water from the solvent.
- The stripped solvent subsequently undergoes some regeneration to prepare the solvent phase for recycling. The loaded strip solution is then treated to remove the desired product before recycling. One of the essential components of this process is that liquid phases are recovered and recycled wherever possible. Recovery of liquid is significant both economically and environmentally.
Top References
- Handbook of Petroleum Processing, 2ndEdition by Steven A. Treese, Peter R. Pujado, David S. J. Jones
- Handbook Petroleum Refining by James G. Speight.
- Springer Handbook of Petroleum Technology by Paul R. Robinson
- Fundamentals of Petroleum and Petrochemical Engineering by Uttam Ray Chaudhuri.
- Solvent Extraction Principles and Practice Second Edition, by Jan Rydberg, Michael Cox, Claude Musikas, and Gregory R.Choppin
For further information, discussion and queries please comment in the box below or contact us at admin@ or follow us on Facebook & LinkedIn.