In the petroleum refinery, the polymerization process converts light olefin gases such as ethylene, propylene, and butylene into hydrocarbons with a greater molecular weight and a more significant octane number of up to 97 that may be utilized as a good gasoline blending stock. Polymerization of ethylene, propylene, and butylene can be performed under various temperature and pressure parameters. The parameters can be set up so that the polymer yield is maximized while the olefines are entirely converted to gasoline.
The polymerization technique was widely used in the 1930s and 1940s but was replaced mainly by the alkylation process after World War II. Although polymerization products have a high-octane sensitivity, their capital and operational costs are substantially lower than alkylation ones. As a result of lower prices, the phase-out of leaded gasoline, and the need for high-octane fuel, the polymerization process is being used again.
It is a controlled process that converts olefin gases to liquid condensation products that may be used to make gasoline or other liquid fuels. The quantity of unsaturated hydrocarbons ranges from 20~90 %, with paraffin, naphthene, and, in particular, aromatic hydrocarbons having relatively low. Antioxidants are used as inhibitors to stabilize polymer gasoline and other commercial fuels that comprise these components.
The difference between alkylation and polymerization is that polymerization only uses olefins and no isobutanes are used. The alkylation process on the other hand forms a long chain molecule by combining two smaller molecules, one olefin and the other isoparaffinic (usually isobutane). Alkylate RON is up to 99 while Poly gasoline RON is up to 97. Further, the catalyst used in Polymerization is Phosphoric acid on inert support while Alkylaiton proceeds in the presence of strong acids (Sulfuric acid or Hydroflouric Acid).
The Pure Oil and Philips Company invented a thermal polymerization technique in 1935. Its low yields were quickly superseded by catalyst-based methods. Polymerization can be achieved by thermally at high temperatures called the Thermal Polymerization Process or in the presence of a catalyst at low temperatures called the Catalytic Polymerization Process.
Catalytic Polymerization | |
Polymerization Condition | Olefins may be efficiently polymerized using an acid catalyst. |
Catalysts | Sulphuric acid, copper pyrophosphate, and phosphoric acid on inert support or on pellets of kieselguhr, a porous sedimentary rock. |
Pressures | 10-81 atm (145-1200 psi) |
Temperatures | 150~220°C (300°F to 450°F) |
Space Velocity | 0.3 gal/lb. |
Thermal Polymerization | |
Advantage | Although thermal polymerization is not as efficient as catalytic polymerization, it has the benefit of being able to polymerize saturated materials that cannot be induced to react by catalysts. |
Temperatures | 510~570°C (950°F ~1060°F) |
Conditions for reactions | This process includes vapour phase cracking, followed by lengthy periods at high temperatures to enable the reactions to proceed. |
The primary feedstock for polymerization has been hydrocarbon gases from cracking stills, especially olefins. Polymerization processes convert by-product hydrocarbon gases generated during cracking into liquid hydrocarbons suitable for use as high-octane motor and aviation fuels and petrochemicals.
Olefins (Propenes and Butenes) are highly reactive compounds that can be combined to produce heavier and more effective cuts. This process combines two or more identical olefin molecules to produce a single molecule with the same components in the exact amounts as the original molecules but has a molecular weight that is two or three times that of the original molecules.
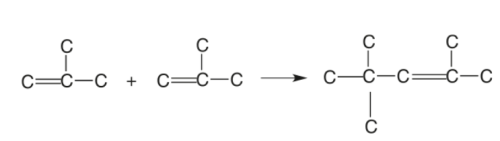
Process Description of Polymerization Process
The combining fractions must be unsaturated to polymerize olefinic gases to generate heavier fractions. The reactions are very exothermic, and the temperature is maintained by injecting cold propane or recycle stream.
After pre-treatment of the olefins (C3/C4) feedstock by removing sulphur compounds and other undesirables, the feed is received in the feed surge drum. The mixture of fresh feed and recycle stream mixture is first heated by the reactor effluent and then in the heater up to ~ 200 °C. The feed stream is then passed through a reactor with a phosphorus catalyst, generally a solid catalyst or liquid phosphoric acid, where an exothermic polymeric reaction occurs. Catalyst: 0.6 – 1.2 kg catalyst consumed per m3 polymerate generated as usual.
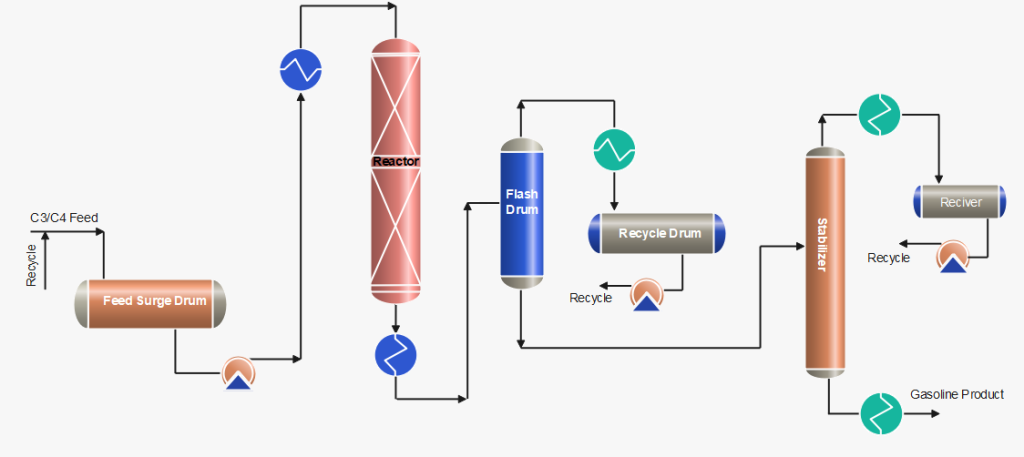
Cold feedstock or recycle cold streams are injected as a quench into the reactor to control temperatures at various pressures. When the reaction products exit the reactor, they are transported to stabilization and/or fractionator systems, which separate the saturated and unreacted gases from the polymer gasoline product. The product is then rundown to storage after cooling.
C3/C4 streams obtained from flash drums and stabilizer are cooled and pumped back to join with the fresh feed. Further, the recycle stream is also used as a quench to control the reactor temperatures.
Commercial Process
The most commonly licensed polymerization process is the UOP polymerization process, which uses phosphoric acid as a catalyst. IFP licenses a Dimersol® process that produces dimers from propene or butene using a homogeneous aluminium alkyl catalyst.
References
- Petroleum Refining Technology and Economics by James H. Gary.
- Polymerization Process for Gasoline Production
- Springer Handbook of Petroleum Technology Hsu Robinson Editors.
- Handbook of Petroleum Refining, James G. Speight.
- www.e-education.psu.edu
- www.setlab.com