The term Merox is an abbriviation of ” Mercaptan Oxidation”. It is a specialized catalytic chemical process created by UOP (Universal Oil Products) applied for the chemical treatment of petroleum distillates to remove mercaptans. In the Merox process, the mercaptans (Sulfur compounds) are removed or converted to a less objectionable form. The process is based on a special UOP catalyst to accelerate the oxidation of mercaptans to disulfides at optimum operating conditions in an alkaline environment.
Mercaptans, also known as methanethiol, are undesirable in finished petroleum products as they adversely affect the product’s odor, stability, and quality, apart from being corrosive to the refining and handling equipment. The Merox Unit selectively sweetens petroleum products by oxidizing the foul-smelling mercaptans into the sweeter disulfides that remain in the product while keeping the overall sulfur content.
[amazon_auto_links id=”3284″]
The Merox process can be applied in a petroleum refinery to treat Kerosene, Jet fuel, naphtha, LPG, or natural gas for order improvement, sulfur removal, meet product specifications and help the oxidation inhibitors to prevent gum formation in the gasoline.
Mercaptans of low molecular weight are more soluble in caustic therefore, Merox process is mainly applied for the low lighter low boiling range petroleum feedstocks such as natural gas, LPG, and light gasoline. These light petroleum fractions contain lighter mercaptans. As low molecular weight mercaptans are soluble in caustic this reduces the sulfur content of the treated product.
The Merox technique is also known as “sweetening,” and is significantly less expensive to install than a Catalytic Hydrotreating Unit. The Merox process needs an alkaline environment, provided by an aqueous solution of Sodium Hydroxide (NaOH) in the presence of Merox catalyst. The catalyst in some processes is a water-soluble liquid. In other versions, the catalyst is impregnated with charcoal granules.
Chemistry of Merox Process
In the first step, the LPG feedstock is combined with an aqueous caustic solution containing UOP’s proprietary liquid catalyst in the trayed extractor vessel. The caustic solution combines with the feedstock and removes mercaptans. The mechanism of mercaptan extraction is as follows:
2RSH + 2 NaOH → 2NaSR + 2 H2O
RHS is a mercaptan, and R is an organic group such as methyl, ethyl, propyl, butyl, etc. For example, methyl mercaptan (methanethiol) has the formula CH3SH.
The second step is the regeneration of the caustic, which includes heating and oxidizing the caustic solution that leaves the extractor. The oxidation process converts the extracted mercaptans to organic disulfides (RSSR), water-insoluble liquids separated and decanted from the aqueous caustic solution.
The reaction that occurs during the regeneration stage is as follows:
2NaSR + 2H2O +O2 → PSSR + 2NaOH
After the separation of the disulfides, the regenerated “lean” caustic solution is recycled to the extractor to begin the mercaptan extraction process.
The following is the net overall Merox reaction, which includes the extraction and regeneration steps:
4RSH + O2 → 2RSSR + 2H2O
LPG MEROX Process Description
- The LPG feedstock after treating with Amine in the Amine Absorption tower enters the prewash vessel and flows upward through a caustic batch, eliminating any undesirable remaining H2S from the feed stream.
- The H2S free feedstock enters the mercaptan extractor and goes upward through the contact trays, where the mercaptans are extracted from LPG by countercurrent contact with the downflowing caustic.
- After leaving the tower, the sweetened LPG passes through three vessels; any entrained caustic is removed in a caustic settler vessel, any residual caustic is further removed in a water wash vessel, and any water is removed in a vessel with a bed of rock salt. The dry-sweetened LPG product leaves the unit for storage. In some cases, Sodium traces present in LPG are removed by a sand filter.
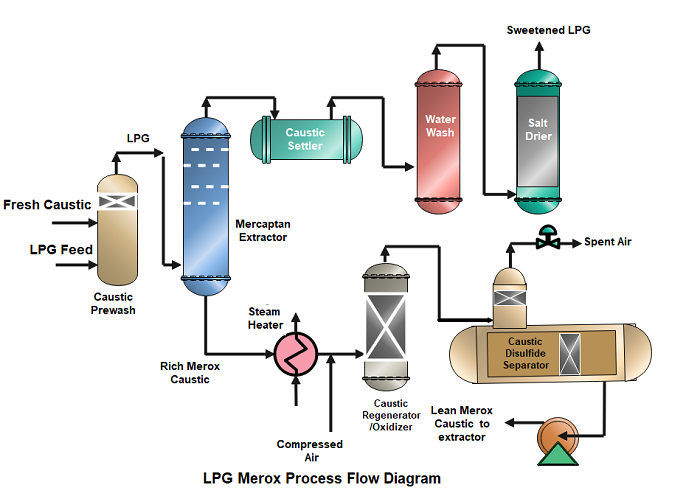
- The mercaptan-rich caustic solution from the extractor bottom passes to the regeneration section. The rich stream is heated and contacted with the compressed air before entering the Oxidizer. In the Oxidizer Mercaptans are oxidized and converted to disulfide oils.
- From the Oxidizer the caustic-disulfide mixture and spent air proceeds to the Disulfide Separator. It is then allowed to produce an upper layer of disulfide and a lower layer of “lean” Merox caustic in the separator vessel. The vertical column of the separator, used to exhaust spent air, has a Rasching rings section to stop any disulfides from being drawn into the vented air. The disulfides are removed from the separator and sent to a hydrotreater unit or fuel storage. After regeneration, the lean Merox caustic is pumped back up to the top of the extractor for further use. The spent air is sent to the Incinerator for safe disposal in the Sulfur Recovery Unit.
Top References
- Springer Handbook of Petroleum Technology Hsu Robinson (Editors)
- Handbook of petroleum product analysis by James G. Speight
- www.wikipedia.com