Pressure swing adsorption (PSA) is a process for purifying hydrogen in a petroleum refinery by removing other hydrocarbon gases. The PSA unit uses molecular sieves to adsorb hydrocarbons and impurities other than hydrogen, resulting in a purified hydrogen gas stream. Pressure is used to release the adsorbed hydrocarbons once the hydrogen has been separated. The use of Pressure Swing Adsorption technology has seen exceptional growth due to its simplicity, less expensive, more energy efficiency, and uninterrupted supply of the desired gas.
PSA unit capacities range from a few hundred Nm³/h to large-scale plants with more than 400,000 Nm³/h. The hydrogen product meets purity requirements up to 99.9 % and is achieved at the highest recovery rates. Major applications of PSA units in petroleum refinery, petrochemical, and chemical industries include;
- In petroleum refineries, the PSA is applied for the removal of lighter hydrocarbons, and H2S from the refinery fuel gas, recycle or bleed gas in hydrotreater, naphtha reformer hydrogen off gas, hydrocracker bleed or off gas, and steam cracker off gas, etc. to provide pure hydrogen for utilization in hydrotreating, hydrocracking, and Isomerization units.
- Bulk removal of carbon dioxide (CO2) during the final step in the large-scale commercial synthesis of hydrogen (H2) or in the production of Ammonia (NH3).
- The recovery and purification of pure hydrogen from different hydrogen-rich streams, such as synthesis gases from steam reforming process, partial oxidation or gasification, as well as from various off-gases in refineries or petrochemical processes, e.g. ethylene off-gas, coke oven gas, methanol, and ammonia purge gas.
Working Principle of PSA
PSA works on the principle that at high pressure, the impurities are adsorbed on the adsorbents, as a result, the high-purity gas is produced. While the adsorbed impurities are desorbed or rejected by significantly reducing the pressure and purging the adrobers with pure gas. As the pressure of the vessel is continuously increasing and decreasing within predetermined short periods, therefore it is called as pressure swing adsorption process. The Pressure Swing Adsorption (PSA) technology is based on the physical binding of gas molecules to adsorbent material. The respective force acting between the gas molecules and the adsorbent material depends on the gas component, type of adsorbent material, partial pressure of the gas component, and operating temperature.
Adsorption is carried out at high pressure typically in the range of 10 to 40 bar until the equilibrium loading is reached. At this point in time, no further adsorption capacity is available and the adsorbent material must be regenerated. This regeneration is done by lowering the pressure to slightly above atmospheric pressure resulting in a respective decrease in equilibrium loading. As a result, the impurities on the adsorbent material are desorbed and the adsorbent material is regenerated. The amount of impurities removed from a gas stream within one cycle corresponds to the difference between adsorption to desorption loading.
Components of PSA
A PSA plant consists of five major components:
- Carbon steel adsorber vessels, designed for fatigue service, because of pressure swings during normal operation.
- A selected mix of adsorbent materials which are typically zeolites and activated carbon are customized by the technology providers. Adsorbent layers are arranged according to impurities and each bed removes the specific impurity. The heaviest components are removed first and the lightest in the last layer.
- A valve and piping skid that houses all automatic process switching valves, manual isolation valves, feed, product, tail gas, equalization piping networks, internal connection headers, and local instrumentation, connected to the adsorber vessels.
- A tail gas drum to mix the tail gas and a tail gas compressor to transfer the purge gas for use as a fuel in the refinery.
- The control system ensures the correct and systematic operation of the PSA unit.
Description of PSA Unit Sequence
The pressure swing adsorption process has four basic process steps:
- Adsorption
- Depressurization
- Regeneration
- Repressurization
Adsorption
The impure feed gas enters the absorber vessel at high pressure in the upward direction. Selected impurities are adsorbed on the adsorbent and high-purity product gas is provided to the downstream unit. When the adsorber is reached its adsorption capacity is taken offline and a fresh adsorber is taken into service. During multibed operation, 6~8 beds, normally two beds are adsorption step any time.
Impurities such as water, heavy hydrocarbons, light hydrocarbons, CO2, CO, and nitrogen are selectively adsorbed on the surface of the adsorbent material. Highly pure hydrogen exits the adsorber vessel at the top. After a defined time, the adsorption phase of this vessel stops, and regeneration starts. Another adsorber takes over the task of adsorption to ensure continuous hydrogen supply. To provide a continuous hydrogen supply, a minimum of 4 adsorber vessels are required
At the completion of the Adsorption step, the impurities reach Level A in the adsorbent bed.
Regeneration of the Adsorbers
The Regeneration phase consists of the following consecutive steps; Its purpose is to recover the adoption capacity and to remove the trapped impurities from the absorbent. The impurities concentration is maximum at the bottom of the bed but greatly decreases as moves upwards in the bed.
Co-current Depressurization
Regeneration of the adsorbers starts with a series of co-current depressurization steps. The gas produced during this step is still at high purity and is utilized for internal pressurization, pressure equalization, and purge-providing steps of other vessels. Depending upon the number of adsorbers and process configurations, 1 to 4 pressure equalization steps are performed. Provide purge is the final depressurization step in the co-current direction providing pure hydrogen to purge or regenerate another adsorber.
After the completion of this step, the impurities reach Level B.
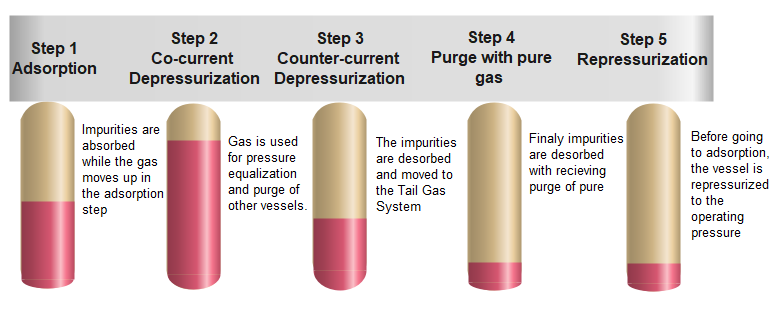
Counter-current depressurization
After the completion of counter-current depressurization, the adsorber is depressurized counter-currently and the remaining pressure is dumped to the tail gas pressure (<1.0 Kg/cm2) system. This step prevents the breakthrough of the impurities at the adsorber top. This is the first step of the regeneration phase when desorbed impurities leave the adsorber at the bottom and flow to the tail gas system. During this step, the impurities are removed from the adsorber and moved with tail gas.
After this step, the impurities reach Level C.
Purging with Pure Gas
Final desorption and regeneration are performed at the lowest pressure of the PSA sequence. Highly pure hydrogen obtained from an adsorber in the provide purge step is used to purge the desorbed impurities into the tail gas system. The residual loading on the adsorbent material is reduced to a minimum to achieve high efficiency of the PSA cycle.
The impurity level reached Level D.
Pressurization
Before restarting adsorption, the regenerated adsorber must be pressurized again. This is accomplished in the pressure equalization step by using pure hydrogen from the adsorbers presently under depressurization. Since final adsorption pressure cannot be reached with pressure equalization steps, repressurization to adsorption pressure is carried out with a split stream from the hydrogen product line. Having reached the required pressure level again, this regenerated adsorber takes over the task of adsorption from another vessel having just terminated its adsorption phase.
Technology Providers
- Linde Engineering as the world leader in adsorption technology has designed and supplied more than 500 PSA plants – including the world‘s largest units and units with the highest availability.
- UOP Honeywell polybed PSA unit, with more than 1,000 systems installed in more than 70 countries. As the industry leader in molecular sieve/adsorbent research and development, UOP combines high-performance adsorbent technology with innovative processes and mechanical design.
Top References
- James G. Speight, in Heavy Oil Recovery and Upgrading, 2019
- www.linde-engineering.com
- www.wikipedia.com
For further information, discussion and queries please comment in the box below or contact us at admin@ or follow us on Facebook & LinkedIn.