The crude distillation unit (CDU) is the first processing unit in an oil refinery. In CDU main equipment is the crude oil fractional distillation column that separates the crude oil feedstock into various petroleum fractions (Gases, naphtha, kerosene, diesel, heavy gas oil, and bottom) which are further processed in downstream units to produce products of desired specifications. This blog focuses only on crude column operation and its optimization to produce the desired straight-run products. For a description of the crude oil distillation unit please view the previous blog “Crude Distillation Unit.”
Crude oil feed after being freed from water and sediments by gravity settling in the storage tank is preheated up to 130 oC in a series of heat exchangers, then salts are removed in the Desalters. Afterwards, crude feed is further preheated, pre-flashed, and finally heated in a furnace up to 330~385 oC, before introducing to the crude oil distillation column. The partially vaporized crude is transferred to the flash zone of the crude column.
Working of Crude Oil Fractional Distillation Column
As the hot vapours from the flash zone rise through the trays up in the column, they are contacted by the colder reflux liquid down to the column. During this counteraction, the lighter fractions are vaporized while heavier ones are condensed. The various products are condensed at different locations according to their boiling points and then separated. In the overhead condenser, the vapours are condensed and part of the light naphtha is returned to the column as reflux. At the bottom of the stripping section, steam is injected into the column to strip off any light hydrocarbons from the crude oil.
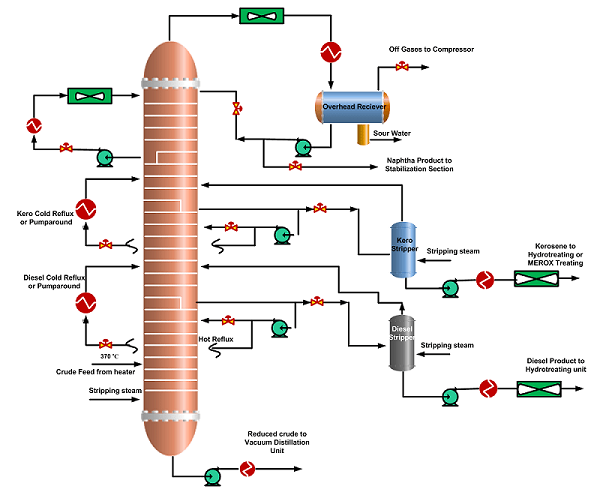
Below are the different sections and operating variables of the crude oil distillation tower, their optimization guidelines, and the working of the crude oil distillation column.
1. Crude Column Inlet temperature
It is the key operating parameter that determines the degree of fractionation of crude oil feedstock. Lower inlet temperature will reduce the separation and lowers the endpoints of side stream products. This temperature can vary from 310ºC to 430ºC depending upon the composition of crude oil but the crude oil heater outlet temperature should be below cracking temperatures. Heavier crude will require higher temperatures to obtain the required degree of separation. Further, a rise in the inlet temperature will increase the endpoints and flow rates of the side-cut products due to the rising of heavier vapours.
2. Crude Column Overhead Temperature
The overhead temperature of the crude oil distillation tower must be controlled 14~17 oC higher than the dew point temperature of water at the column overhead pressure so that no liquid water is condensed in the column. This is to prevent corrosion due to the hydrogen chloride dissolved in liquid water (hydrochloric acid). The top temperature control is critical because the change in top temperature affects the entire operation of the crude column. The temperature is controlled by returning part of the condensed naphtha as reflux. But the rise in the reflux reduces the endpoint of the overhead naphtha making it lighter. Further, the high reflux will also decrease the IBP (Initial Boiling Point) of the next lower-tray product Kerosene. In the same way, increasing the top temperature will have inverse effects of making the column products heavier. Moreover, if the tower inlet temperature is increased, more vapours will rise in the tower, and the reflux rate has to increase to control the same top temperature.
3. Pumparounds or Refluxes
In the distillation tower, the heat required to separate the crude feed is provided by the enthalpy of the feed. For effective separation, heat has to be removed from the tower and this work is done by the overhead condenser and several pumparound streams along the tower length. The pump around flow is adjusted to control the temperature of the draw-off tray, required endpoint, and draw-out rate of the separated product.
The pump around the stream is a liquid withdrawn at a point below a side stream tray that is cooled by the cold crude oil feed in the preheat exchangers. It is then returned back to the column a few trays above the draw-off tray. This pumparound reflux is also called an External Reflux or Cold Reflux. This pump around cooling or cold reflux accomplishes a number of tasks.
- Dumps the lighter vapours or product to the heavier side making the heavier product lighter and reducing the endpoint.
- The returned cold liquid condenses more of the rising vapours and provides more reflux to compensate for the withdrawal of the product from the column.
- The heat is removed from the column at higher temperatures which results in improved thermal efficiency of the column and reduced efficiency of the furnace.
- The pump around streams reduces the vapour flow rate throughout the column. Therefore, the required column is smaller.
The circulating streams help to operate the tower with higher tower inlet temperatures (or called over-flash) for maximum separation of lighter ends from the crude oil. The circulating streams of the column increase the reflux to improve the fractionation and thus improve the gap of 95% and 5% distillation of the column products. To achieve the desired product specifications the distillation gap, and the external reflux streams act as a control point for the side-cut products.
Internal or Hot Refluxes
All side draw products are taken from accumulator trays of the specific product section. A part of each side draw stream is separated and returned as hot internal reflux to the column below each draw-off tray. Like cold reflux, hot reflux is used to control the endpoint or vapour load in the crude distillation tower. The rise in hot reflux will condense the heavy vapours below the draw-off tray, thus making it lighter. On the other side, a decrease in the hot reflux will allow the rise in heavier vapors to flow upwards in the tower, thus making the products heavier. In addition, hot reflux is also used to control the level of the tray. Decrease in tray level is compensated by reducing hot reflux, which allows more vapors to rise and controlling the tray level.
4. Stripping Steam
Stripping steam reduces the partial pressure of the hydrocarbons and thus lowers the required vaporization partial pressure of the hydrocarbons and thus lowers the required vaporization temperature. The stripping steam in the crude distillation tower is utilized to remove lighter vapours from the bottom reduced crude, and control the vapour load of the tower.
5. Over–flash
In order to completely fractionate the crude oil into the required petroleum products, some percentage of the crude feed should be over-flashed. The furnace outlet temperature should be enough to vaporize all the products withdrawn above the flash zone plus about 3–5 volume % of the bottom product. This over-flash has the function of providing liquid wash to the vapours going up the column from the flash zone and improving fractionation on the trays above the flash zone.
6. Side Steam Strippers
The lighter vapours from the side draw products are usually stripped to control their initial boiling point and flashpoint. The strippers contain several trays and the stripping is done using steam at the bottom of the stripper or reboiler-type side stream strippers. The vapours produced are returned back at the tray above the reflux return point.
7. Crude Column Overhead Pressure
The pressure inside the crude distillation tower is controlled by the backpressure of the overhead reflux drum at about 0.2–0.34 bar. The flash zone pressure is usually at 1.0~1.5 bar. The column pressure remains almost stable during the normal operation of the column. Small variations in pressure will result in large temperature changes in the column and hence the compositions of the products might change. Frequent pressure changes will cause unstable column operations.
8. Side Product Draw Out
This amount of the side product is drawn based on the final boiling point or 95% distillation point of the product. If the rate of product withdrawal is increased at the expense of internal reflux. Due to low internal or hot reflux, heavier vapours will rise to the draw-out tray, and the endpoint of the product will increase.
9. Crude Column Bottom
Some portion of the crude is flashed and travels up in the column as vapours, which are then condensed and returned back to the column bottom. The remaining part of the reduced crude remains in a liquid state. Stripping steam is applied here to strip out lighter ends from the reduced crude. The reduced crude is then transferred to the next treatment section.
For further information, discussion and queries please comment in the box below or contact at admin@ or follow us on Facebook & LinkedIn.