A packed column is a type of distillation column that is filled with packing material. Packed columns are used for distillation, gas absorption, and liquid extraction. Packing in Packed columns is applied in the process industry in many types, shapes and sizes. Many of these packings are non-property and come from various suppliers but some are property and patent protected.
Applications of packed bed columns include in a chemical reactor, a distillation process, or a scrubber, gas absorption, desorption, liquid-liquid extraction, vacuum distillation of reduced crude, direct heat transfer in chemical process industries, petroleum refineries, petrochemical industries and fertilizer chemical industry. Packed beds have also been used to store heat in chemical plants.
Some of the top Advantages of packed bed columns are defined below;
- A packed column is less expensive when compared to an equivalent plate column. It is usually less expensive when handling corrosive liquids.
- Due to their construction, packed columns are best for handling foaming systems.
- Packed columns cab used for smaller applications, since packing can fit in areas with less space on the other hand plates can often be expensive and hard to install in columns with a smaller diameter.
- Packed columns will have a lower liquid hold-up than plate columns. This lower placement is especially useful if dealing with flammable or toxic liquids. Since we need to keep potentially dangerous liquids in smaller quantities for safety purposes.
- Typically, plate columns have higher pressure drops than packed columns. Therefore for more consistent pressure in a distillation column, a packed column is a good choice.
- Packed columns provide more surface area for heat and mass transfer in the columns as compared to plat type of distillation columns.
Types of Packings
Various types of packing are used in packed columns; these include Random packing, structures packing and grid packing. Their selection depends upon the service required but random packing is the most common in the process industry.
Packing can be randomly filled with small rings, or it can be a specially structured design. Packed columns may also contain catalyst particles or adsorbents such as zeolites, granular activates carbon etc.
1. Random or Dumped Packing
This type of packing consists of specific geometric shapes packing pieces which are randomly packed or dumped into the shell of the distillation column over its supporting grid. Most separations call for random packing.

The major advantage of random packing is that it is much less expensive to implement than structured packing. Other benefits of random packing, such as improved contact area, mass transfer and efficiency over older technologies such as tray technology, come without high costs. In addition to the applications discussed above, random packing applications also include stripping, distillation, carbon dioxide scrubbing and liquid-liquid extraction.
2. Structured or Systematically Arranged Packing
These packings are wavy layers of wire mesh or corrugated sheets which are stacked in the column. Sometimes, however, more structure is called for than random packing can provide. In this case, structured packing is necessary.
Structured packing is a type of organized packing used to channel liquid material into a specific shape. It uses discs composed of materials such as metal, plastic or porcelain with their internal structures arranged into different types of honeycombed shapes. These honeycomb shapes are always found within cylindrical columns.

Structured packing cylinders are precisely engineered to provide a large surface area for the liquid to contact without causing resistance that impedes the liquid’s flow. It allows for a decrease in the size of columns compared to other distillation column internals. This packing consists of a set of corrugated sheets in the form of honeycombs.
3. Grids Packing
These are also systematically arranged packing but instead of mire mesh or corrugated sheets, these use an open lattice structure.
Grid packings are applied for specific applications, like wash-zones and pump-around sections in crude oil and vacuum columns in refineries, where insensitivity to fouling and corrosion, low-pressure drop, and heat transfer are dominating concerns, and rather a low separation results are required. For such applications, robust, smooth-surface structured packings with specific geometric areas between 50 and 100 m2 /m3 like Mellagrid are used, or more frequently, robust ordered structures known as grids packings.
Being highly open structures, grids can handle easily situations where high vapour and low liquid loads are involved. They allow high capacities at rather a low-pressure drop and are usually used in combination with spray distributors. The turndown of the latter is a limiting factor and their liquid distribution quality is poor but more than sufficient to handle typical heat transfer requirements.

It can provide high heat transfer efficiency, high mechanical strength and antifouling characteristics in severe services that are prone to plugging, coking, erosion and containing solids. The smooth surface provides low liquid hold-up, and reduces the residence time and the possibility of coke formation.
Types of Random Packing
To install random packing, materials are dumped into a column and allowed to settle. The materials are collected randomly in the packaging bed inside the collection container. Then the liquid to be separated flows through the materials. Random packing makes use of a few different structures:
1. Raschig Rings
These are the cheapest, oldest, and previously most widely used packings. These were first presented by Dr Rasching in Germany in 1904. The height of the ring is equal to its diameter. The rings are cut from pipes but they can also be rolled from strips. They are smooth, without holes, grooves, ribbing or other textured elements. They have low capacity and low efficiency, and they tend to cost more than other types of random packing. Because Raschig rings have such a high cost in comparison to their efficacy, applications for this type of packing are limited. In situations where corrosive material is being separated, however, ceramic Raschig rings are effective thanks to their high corrosion resistance.

2. Lessing Rings
These are similar to Rasching rings but a partition is added across the centre of the ring to improve the surface area. The partition strengthens the rings but the improvement in efficiency is lower. Lessing rings are made of ceramic. Like all ceramic packing pieces, they are highly resistant to heat and corrosion. These qualities make them ideal for applications such as regenerative oxide systems.

3. Tri-Packs
Tri-Packs were first developed in the late 16970s and are now broadly used. Tri-Packs provide many advantages over older types of packing. Due to their spherical shape, they are not prone to nesting and settling. Their interior ribs also maximize surface area and wetting qualities. Tri-Packs are a good choice to achieve low-pressure drop and high-mass transfer rates. Tri-Packs are commonly offered in a range of plastics, providing corrosion and temperature resistance.
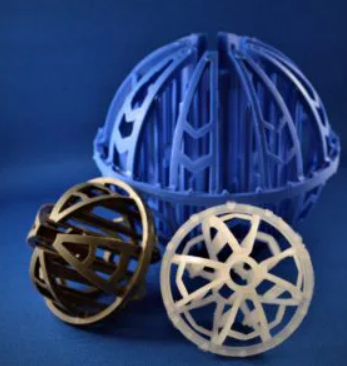
5. Pall Rings
Pall Rings are similar to Raschig rings but come with added sophistication. Pall rings include added internal support structures and external surfacing. The texture within the ring walls allows for points of internal dripping that significantly increase the capacity and the efficiency of the packing. Pall rings work particularly well for distillation and absorption applications.
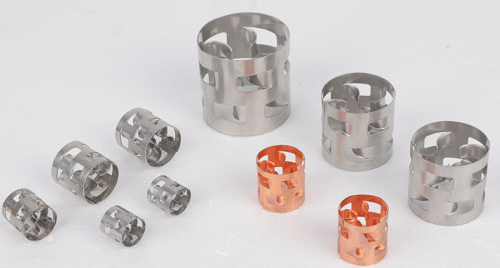
5. Saddle Rings
Saddle rings come in two primary types — Berl saddles and Intalox® saddles. As their name suggests, they’re shaped like tiny saddles. They differ from Raschig and Pall rings in that their length exceeds their diameter. Smooth Berl saddles are often shorter, with a more traditional saddle shape. Berl Saddles have a smaller free gas space than Rasching and Lessing rings, but their aerodynamic shape is better giving lower pressure drop and higher capacity as compared to Rasching and Lessing rings.
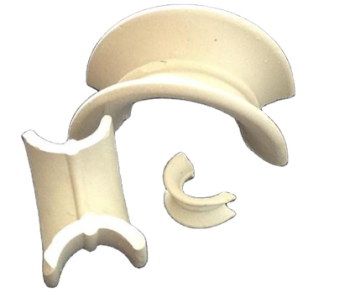
Intalox® saddles are significantly longer, shaped much like pieces of macaroni halved lengthwise into long, open curved pieces. They also offer small holes and grooves for increased surface area and contact opportunity. Saddle rings, with their increased surface area for liquid and vapour contact, offer increased capacity and efficiency. They are ideal for chemical distillation, stripping and absorption.
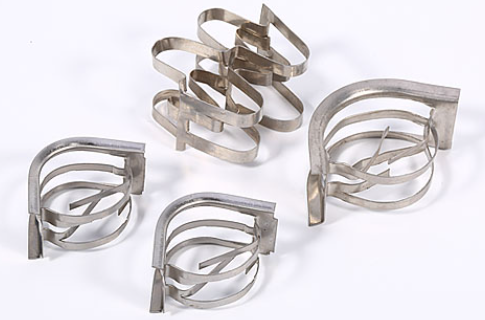
Top References
- Distillation Design by Henry Z. Kister
- www.machengineering.com
- www.wikipedia.com
For further information, discussion and queries please comment in the box below or contact us at admin@ or follow us on Facebook & LinkedIn.