Solvent Deasphalting is an extraction process used in petroleum refining to remove the asphaltenes from the refinery residues to prepare a suitable feedstock for catalytic conversion unit and lube base oil. In propane deasphalting, propane is used as an extraction fluid for the removal of asphaltenes. The de-asphalter unit is usually configured after the vacuum distillation tower. The output from the de-asphalter unit is de-asphalted oil (DAO) and asphalt pitch.
Asphaltenes
Asphaltenes are defined as the nonpolar and nonvolatile components of crude oil. They are insoluble in alkanes (normal pentane and normal heptane) but soluble in aromatics (benzene and toluene). The chemical properties of asphaltenes are not well known. In general, asphaltenes are known as complex organic matter, containing carbon, oxygen, nitrogen, and sulfur. The black colour of some crude oils and residuals is related to the presence of asphaltenes, which have not flocculated or precipitated. Asphaltenes have polar molecules with very high molecular weights.
Applications of Solvent Deasphalting Unit
Solvent deasphalting (SDA) is applied as part of a bottom-of-the-barrel upgrading solution that separates higher-quality components from heavy residues and other heavy petroleum feedstocks using solvent extraction and supercritical solvent recovery technology. Following are some applications of SDA in petroleum refineries;
- SDA (Solvent Deasphalted) pitch can be used in the manufacturing of asphalts and cement and as a blending component in refinery fuel oil pools. Other potential uses of SDA pitch include the production of hydrogen, synthesis gas, or low-Btu fuel gas and as a solid-fuel blending component.
- It is used to remove the asphaltenes from the residue to prepare a suitable feedstock for Hydrocracker and FCC catalytic conversion units. In these conversion units, the performance of the catalyst is greatly impaired by the presence of heavy metals and the high Conradson carbon content of the residue feed. In hydrocrackers and FCC units, DAO is easier to process than straight-run residual oils. This is because asphaltenes easily form coke and contain catalyst poisons such as nickel and vanadium, and the asphaltene content of DAO is (by definition) almost zero.
- The Solvent Deasphalting process has been in commercial use for the preparation of lubricant-bright-stock feeds from asphalt-bearing crude residue.
- Commercial penetration grades of asphalt can be produced by blending the SDA pitch with suitable aromatic flux oils. In many cases, this can eliminate the need for air-oxidizing asphalts and thus present obvious economic and environmental advantages.
- Deasphalted Oil (DAO) can be used to produce low-sulfur fuel oil compared with direct desulfurization of the atmospheric residue, this route can be economically attractive in many cases.
Vacuum residue is the typical feed of Solvent Deasphalting unit although atmospheric residues have also been commercially solvent-deasphalted. The vacuum residue with the heavy Arabian crude feed, has specifications of 570 °C TBP, API gravity 3.6, CCR 25 %, Sulfur 5.5 % and Ni/V metals ~200 wt ppm.
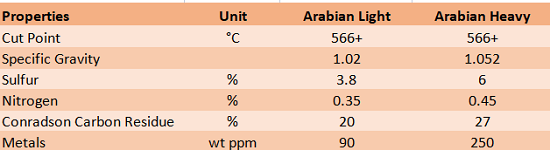
The solvent Deasphalting process produces a low-contaminant, relatively high hydrogen deasphalted oil product (DAO) and a pitch product that contains the majority of the residue’s contaminants (metals, asphaltenes, CCR). SDA units can provide a conversion rate of up to 90%.
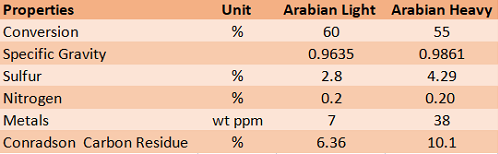
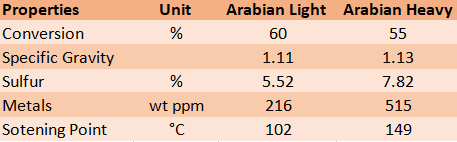
Propane Deasphalting Process
Propane usually is used as the solvent in Solvent deasphalting but ethane, butanes, pentanes, or pentanes and various mixtures of these can be used. These materials are readily available in the refinery. Their makeup rates are also small as are recycled in the process. Propane is preferred where high-quality DAO is desired but it produces low DAO yields. Heavier solvents Butane or pentane are used where high yields are desired.
Propane has a significant solvent ability at temperatures 40~60°C because paraffin is very soluble in propane, but the solubility decreases with an increase in temperature until at the critical temperature of propane [206°F (96.8°C)] all hydrocarbons become insoluble. In the range of 40 ~ 96.8°C the high molecular weight asphaltenes and resins are largely insoluble in propane.
Solvent Deasphalting Process Description
Vacuum residue feed enters the unit directly from the vacuum distillation tower and is heated to ~60 °C before entering the top portion of a trayed extraction tower at 34 Kg/cm2. Liquid propane is entered into the bottom of the tower below the bottom tray. The propane solvent flows up the tower counter currently to the precipitated asphalt.
The extracted asphalt is retrieved from the bottom of the tower and routed through a fired heater to enter the top tray of a baffle-trayed separator. Some propane entrained in the asphalt phase is extracted from the flash tower’s overhead. The asphalt phase exits the flash tower at the bottom and decreases pressure before entering the asphalt stripper tower above the top row of baffles.
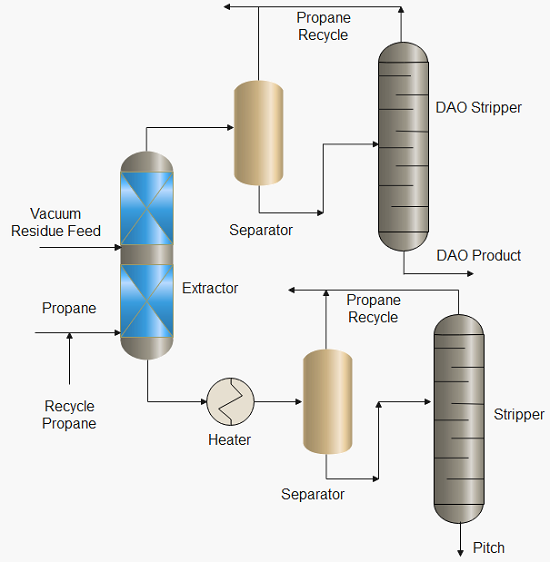
The bottom of the stripper tower is filled with steam, and the remaining entrained propane is extracted from the asphalt. The stripped asphalt leaves the tower, is cooled to battery conditions, and is directed to storage or the asphalt blending unit. The propane strip out is run into the propane accumulator.
The deasphalted oil phase from the extraction tower overhead enters a high-pressure oil evaporator, where most of the entrained propane is removed. The propane stream exits the evaporator and enters the propane accumulator after cooling. The oil phase leaves the evaporator and enters the top row of baffles in a low-pressure stripper tower.
The remaining propane is stripped from the oil phase and exits the stripper tower. Steam is injected into the tower’s bottom trays and travels counter currently up the tower to the oil phase. The propane is cooled and drained of the water from the stripping steam in the accumulator. The deasphalted oil is extracted from the stripper tower’s bottom.
Commercial Solvent Deasphalting Processes
- UOP Foster Wheeler SDA Process, collectively UOP and FWUSA have licensed and designed over 70 SDA units of capacity 7000~50000 BPD.
- An advanced version of solvent deasphalting is “residuum oil supercritical extraction,” or ROSE. The ROSE TM Process was developed by the Kerr McGee Corporation and now is offered for license by KBR Engineering and Construction, a subsidiary of Halliburton.
Top References
- Petroleum Fuels Manufacturing Handbook, Surinder Parkash, Ph.D.
- Handbook of Petroleum Processing, 2nd Edition by Steven A. Treese, Peter R. Pujado, David S. J. Jones.
- Handbook of Petroleum Refining Processes by Robert A Mayers.
- www.wikipedia.com
For further information, discussion and queries please comment in the box below or contact us at admin@ or follow us on Facebook & LinkedIn.