Heat Recovery Steam Generators (HRSGs) are the energy saving equipments of process industries like chemical plants, refineries, and power generation, transforming waste heat into valuable steam for power, heating, or industrial processes. Their ability to enhance efficiency, cut costs, and reduce emissions makes them vital for sustainable operations. Whether in combined cycle plants or co-generation systems powering industrial processes, HRSGs play a critical role in making energy production more sustainable and cost-effective. By understanding their design, applications, and benefits, you can leverage HRSGs to optimize operations while meeting environmental and safety goals.
What is a Heat Recovery Steam Generator?
A Heat Recovery Steam Generator (HRSG), often referred to as a waste heat recovery boiler, is a heat exchanger that captures thermal energy from hot exhaust gases, typically from gas turbines or industrial processes, and converts it into steam. This steam powers turbines for electricity, supports industrial processes, or provides heating, making HRSGs a cornerstone of energy efficiency. Unlike traditional boilers that burn fuel directly, HRSGs repurpose “free” heat that would otherwise be lost, slashing fuel costs and reducing emissions.
HRSGs shine in combined-cycle power plants, where they pair with gas turbines to boost electricity production, and in cogeneration systems, where they supply steam for industrial needs while generating power. Their versatility makes them essential in industries like petroleum refining, chemical processing, and even marine applications.
Why Heat Recovery Steam Generators are important?
HRSGs are more than just equipment. They’re efficiency powerhouses with wide-reaching benefits:
- Energy Savings: They capture waste heat, boosting plant efficiency by up to 60% in combined-cycle setups.
- Cost Reduction: Generating steam without extra fuel lowers operational expenses.
- Environmental Benefits: Less fuel consumption means fewer greenhouse gas emissions and compliance with strict regulations.
- Adaptability: From sulfur recovery to gas turbine systems, HRSGs fit a range of applications.
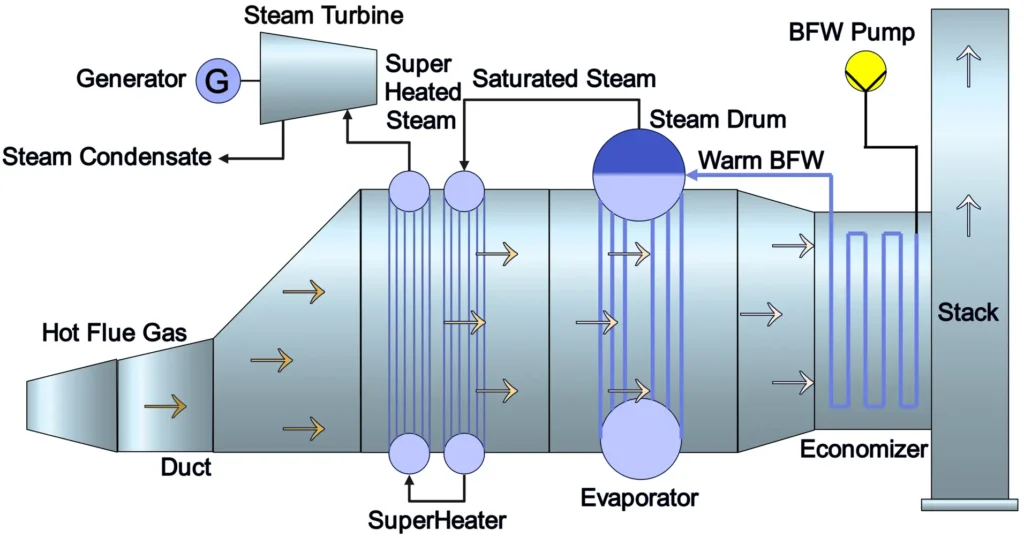
How Heat Recovery Steam Generators Work
HRSGs transform hot exhaust gases into usable steam through a well operated process. Here’s how it happens:
- Hot Gas Input: Exhaust gases, often from gas turbines at 400–600°C (752–1112°F), enter the HRSG, carrying significant thermal energy.
- Heat Transfer: The gases flow over tubes in three key sections:
- Economizer: Preheats feedwater to reduce energy needs and prevent thermal shock.
- Evaporator: Converts water into saturated steam by absorbing heat.
- Superheater: Heats steam further to produce superheated steam, ideal for turbines or high-temperature processes.
- Steam Output: The steam drives turbines for power or supports industrial processes like heating.
- Exhaust Exit: Cooled gases exit via a stack, typically at 150–300°C (302–572°F), with temperatures controlled to avoid corrosion.
The design adapts to gas characteristics like temperature, pressure, and composition, ensuring durability and efficiency in diverse settings, from corrosive sulfur gases to high-pressure hydrogen streams.
Key Components of a Heat Recovery Steam Generator
An HRSG is a complex system with several critical components working together to recover heat efficiently. Here’s a closer look at the main parts:
- Economizer: Preheats feedwater using the cooler exhaust gases, reducing the energy needed to reach boiling conditions.
- Evaporator: Facilitates the phase change from liquid water to steam, absorbing the latent heat of vaporization.
- Superheater: Increases the steam’s temperature above its saturation point, producing superheated steam for turbines or processes.
- Drum: Separates steam from the water-steam mixture, ensuring dry steam is sent to the superheater. It also aids in circulation and maintains water quality through blowdown.
- Downcomers and Risers: These tubes enable natural or forced circulation of water and steam within the HRSG. Downcomers carry water downward, while risers carry the steam-water mixture upward due to density differences.
- Ductwork and Fans: Direct the flow of exhaust gases and combustion air, ensuring efficient heat transfer.
Types of Heat Recovery Steam Generators
HRSGs come in various designs according to specific needs. They’re classified by circulation and configuration:
Circulation Types
- Natural Circulation: Uses the density difference between water and steam to drive flow through vertical tubes. It’s reliable for large gas flows and requires no pumps.
- Forced Circulation: Employs pumps to move the steam-water mixture, often used for compact designs but requiring pump maintenance.
- Once-Through: Water enters as liquid and exits as steam without recirculation. These drum less units enable faster startups but demand high-purity water to prevent tube deposits.
Configuration Types
- Water Tube HRSGs: Hot gases flow outside tubes, with water inside. Ideal for large flows and clean gases, they support compact designs with finned tubes.
- Fire Tube HRSGs: Gases flow inside tubes, surrounded by water. Suited for smaller flows and high pressures, but less flexible for superheater placement.
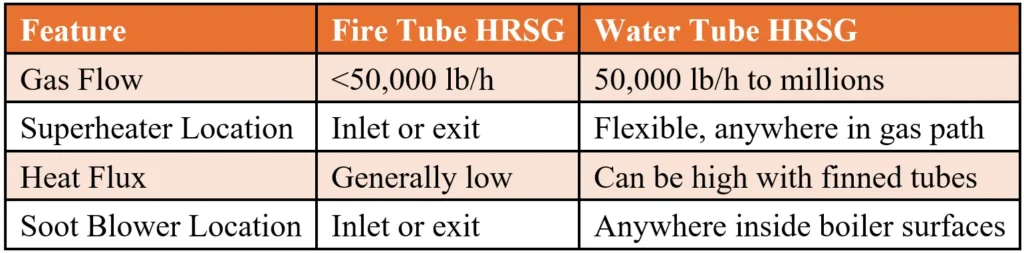
Key Applications of Heat Recovery Steam Generators
HRSGs are indispensable across various industries, each with unique demands:
1. Sulfur Recovery Plants
In the Claus process, HRSGs cool gases from 1800–2800°F to 650°F, generating high-pressure steam (600–650 psig). Two-pass designs with refractory-lined tube sheets to protect against sulfur corrosion.
2. Sulfuric Acid Plants
HRSGs cool gases from 1900°F to 800°F, ensuring optimal conditions for catalytic conversion of SO₂ to SO₃. Gas bypass systems maintain precise exit temperatures, and hot casing designs prevent corrosion from SO₃.
3. Hydrogen Plants
In steam reforming, HRSGs cool high-pressure gases (20–40 atm) from 1600°F to 600°F. Fire tube designs handle the high heat transfer rates of hydrogen-rich gases, with careful engineering to avoid overheating.
4. Gas Turbine Systems
HRSGs recover heat from gas turbine exhaust (900–1000°F), cooling it to 250–300°F. Water tube designs with multiple pressure loops maximize efficiency in combined-cycle or cogeneration plants.
5. Incineration Applications
HRSGs manage dirty gases at 1500–2000°F from waste incineration. Water tube boilers with bare tubes and soot blowers handle slagging and ensure compliance with environmental standards.
6. Enhanced Oil Recovery (EOR)
Special HRSGs produce wet steam (80% quality) at high pressures (up to 2500 psig) for injecting into oil wells, reducing oil viscosity for easier extraction.
7. Marine Applications
Compact HRSGs power steam turbines in ships, operating at 60–65 bar and producing superheated steam at 540°C.
Design Considerations and Challenges
HRSG design requires balancing efficiency, durability, and cost. Key challenges include:
- Corrosion: Sulfur trioxide (SO₃) or hydrogen chloride (HCl) in gases can cause low-temperature corrosion. Hot casing and high feedwater temperatures (above 320°F) mitigate this.
- Slagging: In incineration, ash deposits form slag. Bare tubes and soot blowers keep surfaces clean.
- High Heat Flux: Hydrogen-rich gases increase heat transfer, requiring robust tube designs.
- Thermal Stress: Frequent startups and shutdowns stress materials. Up-flow economizers and gas bypass systems help.
- Pinch and Approach Temperatures: A pinch point of 8–28 K and economizer approach of 6–17 K optimize heat recovery but increase costs if too small.
- Back-Pressure: Typical back-pressures of 2.5–3.75 kPa balance turbine efficiency and HRSG size.
Heat Absorption in Heat Recovery Steam Generator
Heat distribution across HRSG components is critical:
- Economizer: 20–30% of total heat, preheating water.
- Evaporator: 30–50%, converting water to steam.
- Superheater: 40–60%, producing superheated steam for high-efficiency applications.
People Also Asked Questions with Answers
What’s the difference between a heat recovery steam generator and a traditional boiler?
An HRSG uses waste heat from processes like gas turbine exhaust, while a traditional boiler burns fuel directly. HRSGs are more efficient in combined-cycle systems ecl systems but depend on available waste heat.
How efficient are heat recovery steam generators?
HRSGs recover up to 90% of waste heat, boosting plant efficiency to 50–60% in combined-cycle systems, compared to 30–40% for simple-cycle gas turbines.
What industries use heat recovery steam generators?
HRSGs are used in chemical plants, refineries, gas turbine power plants, sulfuric acid production, incineration systems, and marine applications.
How do heat recovery steam generators reduce environmental impact?
By recovering waste heat, HRSGs reduce fuel consumption, lowering greenhouse gas emissions and operational costs. They also help manage emissions in processes like sulfur recovery.
References:
- Ganapathy, V. (2003). Industrial Boilers and Heat Recovery Steam Generators: Design, Applications, and Calculations. Marcel Dekker.
- Kitto, J. B., & Stultz, S. C. (Eds.). (2005). Steam: Its Generation and Use. The Babcock & Wilcox Company.
- Nag, P. K. (2007). Power Plant Engineering. Tata McGraw-Hill.
- Sarkar, Dipak K. (2015). Thermal Power Plant: Design and Operation. Elsevier.
- https://www.sciencedirect.com
- https://patents.google.com