Diesel fuel keeps our world moving, powering trucks, trains, and heavy machinery. But with growing environmental concerns, refineries face the challenge of producing cleaner diesel with minimal sulfur content. This is where the diesel hydrodesulfurization (DHDS) unit steps in. It is a vital refinery process that removes sulfur and other impurities transforming raw diesel into clean, high-performance fuel that meets stringent global standards.
What is a Diesel Hydrodesulfurization Unit?
The Diesel Hydrodesulfurization Unit is a catalytic chemical process designed to strip away sulfur, nitrogen, and aromatics from diesel feedstock. These impurities, if left unchecked, can corrode engines, increase particulate matter (PM) emissions, and contribute to acid rain. Sulfur, for example, forms harmful sulfur dioxide (SO₂) when burned, posing risks to both health and the environment. The HDS process uses hydrogen gas and catalysts to convert sulfur compounds into hydrogen sulfide (H₂S), which is then separated, ensuring the production of ultra-low-sulfur diesel (ULSD) with sulfur levels below 10 ppm.
Why It Matters
Sulfur in diesel fuel contributes to:
- Air Pollution: Burning high sulfur diesel releases SO₂, leading to acid rain and respiratory issues.
- Fuel Performance: Reducing sulfur improves diesel’s burning characteristics, minimizing smoke and enhancing engine efficiency.
- Regulatory Compliance: Global standards demand ultra-low sulfur diesel (ULSD), with sulfur levels as low as 10–15 ppm in many regions.
By removing sulfur, DHDS ensures diesel meets these standards while improving its odor, stability, and performance.
How Does a Diesel Hydrodesulfurization Unit Work?
Diesel Hydrodesulfurization unit transforms raw diesel into a cleaner product. The process revolves around a trickle-bed reactor, where diesel feedstock reacts with hydrogen over a catalyst to remove impurities. Here is a step-by-step breakdown:
1. Feed Preparation
The DHDS process begins with the preparation of the diesel feedstock, typically a blend of straight-run diesel from the crude distillation unit, cracked diesel from fluid catalytic cracking (FCC) or other diesel units. These feedstocks contain organic sulfur compounds such as thiophenes, benzothiophenes and dibenzothiophenes (DBTs).
- Filtration and Preheating: The feedstock is filtered to remove particulates and passed through a heat exchanger to raise its temperature to approximately 200–300°C. This preheating reduces the energy required in the reactor.
- Hydrogen Mixing: The feedstock is mixed with high purity hydrogen gas, sourced from a hydrogen plant or recycled from within the unit. The hydrogen-to-feed ratio is typically 200–400 Nm³/m³ of diesel to ensure sufficient hydrogen for desulfurization and to minimize coking on the catalyst.
2. Heating and Pressurization
The diesel and hydrogen mixture is further heated to the reaction temperature (320–425°C) using a fired heater. The mixture is also pressurized to 150–250 psig (10–17 bar) for atmospheric diesel or up to 600–1000 psig for heavier feeds. These conditions optimize the catalytic reaction while preventing thermal cracking of the diesel.
- Temperature Control: Precise temperature control is critical to avoid overheating, which can lead to catalyst deactivation or unwanted side reactions.
- Pressure Management: High pressure enhances hydrogen solubility in the liquid phase, improving reaction efficiency.
3. Catalytic Reaction in the Reactor
The heart of the DHDS unit is the fixed-bed catalytic reactor, where the desulfurization reaction occurs. The reactor is packed with a catalyst, typically cobalt-molybdenum (CoMo) or nickel-molybdenum (NiMo) supported on alumina (Al₂O₃). The choice of catalyst depends on the feedstock’s nitrogen content and sulfur compound complexity.
Key Reactions in the reactor are:
- Hydrodesulfurization (HDS): Converts sulfur compounds (e.g., mercaptans, thiophenes) into H₂S.
- Hydrodenitrogenation (HDN): Transforms nitrogen compounds into ammonia.
- Hydrodearomatization (HDA): Reduces aromatics to naphthenes, boosting cetane number.
- Olefin Saturation: Stabilizes olefins to prevent gum formation.
These reactions compete for hydrogen and catalyst sites, requiring careful optimization to achieve deep desulfurization.
4. Product Separation
After the reaction, the effluent from the reactor contains desulfurized diesel, H₂S, unreacted hydrogen, and light hydrocarbons. This mixture undergoes several separation steps:
- High-Pressure Separator: The effluent is cooled to 40–60°C and sent to a high-pressure separator, where H₂S and light gases are separated from the liquid diesel. The gas phase, rich in H₂S, is sent to a gas treatment system.
- Low-Pressure Separator: The liquid phase undergoes further separation to remove residual gases and stabilize the diesel product.
5. Hydrogen Recycling
Unreacted hydrogen is recycled back to the reactor to minimize hydrogen consumption, which is a significant operational cost. A compressor boosts the pressure of the recycle gas, and a purge stream removes light hydrocarbons and impurities to maintain hydrogen purity (typically >90%).
6. Product Polishing
The desulfurized diesel is sent to a stripper column to remove residual H₂S and light hydrocarbons, ensuring the final product meets ULSD specifications (e.g., <10 ppm sulfur).
Process Flow Diagram
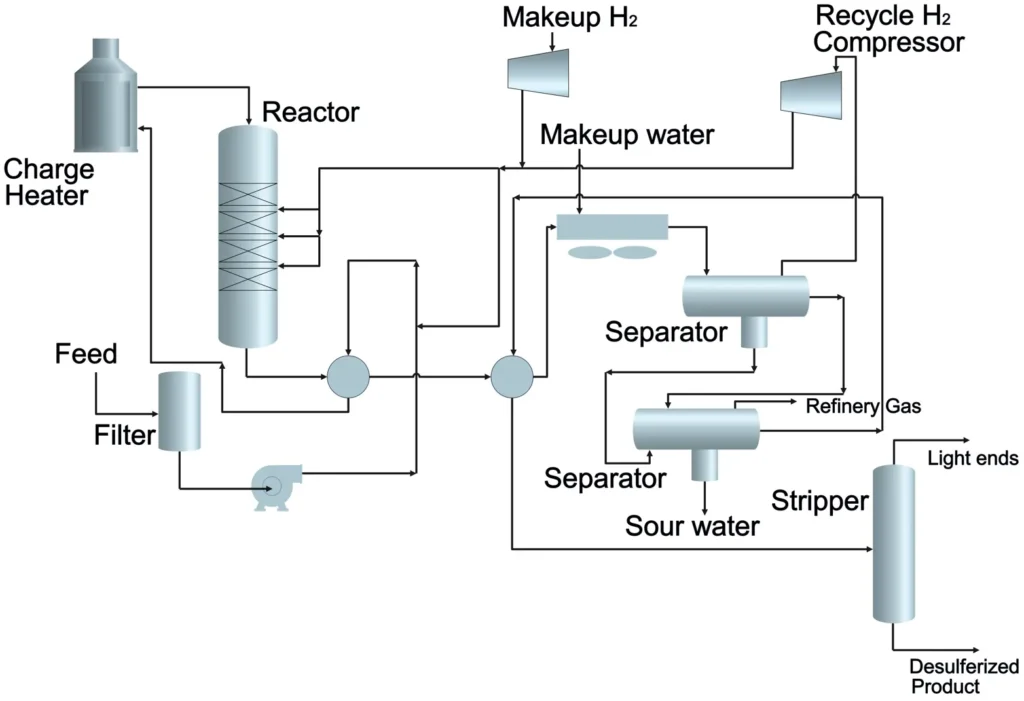
Key Components of a DHDS Unit
A DHDS unit is a complex system with several critical components:
- Reactor: A fixed-bed reactor where the catalytic reaction occurs.
- Heat Exchangers: Preheat the feed and hydrogen mixture to the required temperature.
- Pumps and Compressors: Maintain high pressure and recycle hydrogen gas.
- Separators: Remove H₂S and other byproducts from the treated diesel.
- Catalysts: CoMo or NiMo catalysts, chosen based on feedstock characteristics and nitrogen content.
Catalyst Selection
The choice of catalyst depends on the feedstock. For high nitrogen feeds, NiMo catalysts are preferred due to their higher hydrogenation activity, while CoMo catalysts are more effective for sulfur specific removal.
Challenges in DHDS Operations
Producing ULSD is not easy. Refineries face several hurdles:
- Complex Sulfur Compounds: Simple sulfur compounds like mercaptans are easy to remove, but complex molecules like dibenzothiophenes (DBTs) are sterically hindered, making deep desulfurization challenging.
- Aromatic Inhibition: High aromatic content, especially in FCC or coker feeds, competes with sulfur compounds for catalyst sites, slowing HDS. Polyaromatics are particularly problematic.
- Catalyst Deactivation: Silicon from antifoaming additives or metals like vanadium and nickel can deposit on catalysts, reducing their effectiveness.
- Lubricity Loss: Removing sulfur strips diesel’s natural lubricity, requiring additives to meet standards.
- High Energy Consumption: The process requires significant energy for heating and pressurization, increasing operational costs.
Optimizing DHDS Units for Efficiency
Refineries employ several strategies to enhance DHDS performance:
- Advanced Catalysts: NiMo catalysts supported on novel materials like LaAlOx show improved activity for ultra deep desulfurization.
- Reactor Design: Increasing reactor volume or improving feed distribution enhances efficiency.
- Hydrogen Management: Higher hydrogen partial pressure or purer makeup hydrogen boost reaction rates.
- Cycle Length Optimization: Catalyst cycles typically last 24–36 months, limited by pressure drop. Higher hydrogen pressure can extend cycle life.
Diesel Fuel Properties and Their Impact
The quality of diesel affects both engine performance and emissions. Key properties include:
- Sulfur: Lower sulfur reduces PM emissions, cylinder wear, and deposits, enabling advanced emission controls.
- Cetane Number: Higher cetane improves combustion efficiency and reduces engine knock.
- Aromatics: Lower aromatics reduce particulate emissions but may impact fuel density.
- Density and Distillation: Proper density and distillation points ensure optimal engine performance and cold flow properties.
References:
- Zhu, F. X., Hoehn, R., Thakkar, V., & Yuh, E. (2017). Hydroprocessing for Clean Energy: Design, Operation, and Optimization. American Institute of Chemical Engineers, John Wiley & Sons.
- Nour Shafik El-Gendy, James G. Speight. (2015). Handbook of Refinery Desulfurization. CRC Press.
- Oballa, Michael C. (1994). Catalytic Hydroprocessing of Petroleum and Distillates. CRC Press.
- Fahim, M.A., Al-Sahhaf, T.A., & Elkilani, A. (2010). Fundamentals of Petroleum Refining. Elsevier.
- Gary, J.H., Handwerk, G.E., & Kaiser, M.J. (2007). Petroleum Refining: Technology and Economics (5th ed.). CRC Press.
- https://www.researchgate.net
- https://www.sciencedirect.com