The operating conditions of Hydroprocessing units make them vulnerable to various corrosion phenomena. The severity of the hydroprocessing units in petroleum refineries has increased due to higher levels of sulfur and nitrogen in feedstocks and the demand for low Sulfur in products. Adopting best design-operating practices and selecting the best material for construction can make the unit operations corrosion-free.
The corrosion process in Hydrotreating and Hydrocracking units has received special attention in the last few years due to the strong dependence of the refineries on these technologies. Material of construction, unit design and operating conditions are improving gradually to maximize the life cycle of the units. Following are some major corrosion phenomena that take place in Hydroprocessing units.
- Naphthenic Acid Corrosion
- Sulfidation (High-Temperature H2S Corrosion with or without Hydrogen)
- Erosion Corrosion
- Polythionic Acid Attack
- High-Temperature H2 Attack (HTHA).
- Hydrogen Embrittlement
- Ammonium Bisulfide (NH4HS) Corrosion
- Ammonium Chloride (NH4Cl )Corrosion
- HCl Corrosion
1. Naphthenic Acid Corrosion (NAC)
Naphthenic Acid Corrosion (NAC) is caused due to organic naphthenic acids present in crude oil that transfer to the downstream hydroprocessing units with feed. The severity of corrosion increases with increasing acidity of the hydrocarbon phase, temperature, low sulfur content and high velocity.
The neutralization number or TAN is a measure of the acidity (organic acid content). NAC primarily occurs in hot hydrocarbon streams above 175~425 °C but severity increases with increasing temperature.
Sulfur promotes iron sulfide formation and has an inhibiting effect on NAC, up to a point. Naphthenic acids remove protective iron sulfide scales on the surface of metals. NAC can be a particular problem with very low sulfur crudes. While a crude TAN threshold of 0.30 is typically cited as the TAN level below which NAC is not expected, however, some NAC cases have also been reported with low sulfur and crude TAN as low as 0.10.
Naphthenic acids are destroyed by catalytic reactions in hydroprocessing units. NAC of 300 series SS is also inhibited by the injection of hydrogen in the feed. Atmospheric gas oil (AGO) circuits, heavy vacuum gas oil (HVGO) and sometimes light vacuum gas oil (LVGO) circuits contain naphthenic acid. NAC has been reported in the light coker gas oil (LCGO) and heavy coker gas oil (HCGO) streams in delayed coking units processing high TAN feed.
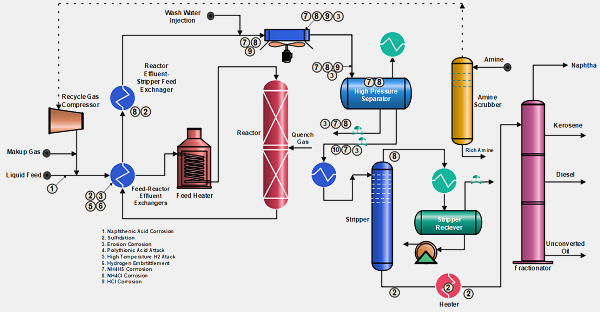
2. Sulfidation
There are two types of Sulfidation Corrosion, I- Sulfidation in the presnce of Hydrogen II- Sulfidation without Hydrogen.
I. High Temperature H2/H2S Corrosion
This corrosion occurs in most of the sections of the Hydroprocessing units because of the H2 and H2S presnce. The presence of hydrogen in H2S-containing streams increases the severity of high-temperature sulfidation (sulfidic) corrosion at temperatures above 230 °C. Corrosion rate increases with the rise in temperature, concentration and partial pressure of H2S. Because of the smooth, large, relatively uniformly corroded surface produced by high-temperature H2/H2S corrosion, it can lead to rupture-type failure rather than a localized or pinhole leak.
High-temperature H2/H2S Corrosion rates are higher in high-pressure Hydrocrackers and Hydrotreaters due to the high partial pressure of H2S as compared to lower-pressure hydrotreaters.
The addition of hydrogen promotes cracking of the reactive sulfur species into H2S prior to the reactor, increasing the rate of corrosion in comparison to corrosion from the reactive sulfur alone.
II. Sulfidation without Hydrogen
This type of corrosion occurs in the feed section before the Hydrogen is introduced and in stripping sections where hydrogen has been removed. This corrosion occurs at temperatures 260~540 °C by direct reaction of sulfur-containing compounds with the metal surface. The corrosion rate increases with the temperature and concentration of sulfur compounds.
3. Erosion-Corrosion
Erosion-corrosion is the type of corrosion that occurs when particle erosion or high flow velocity contributes to corrosion by removing protective films or scales from the piping or otherwise accelerating the corrosion rate. This is also called velocity-assisted corrosion.
Hydroprocessing reactor effluent piping may be subject to erosion-corrosion by ammonium bisulfide. The metal loss is dependent on several factors including the ammonium bisulfide concentration, H2S and NH3 partial pressures, velocity and shear stress on the pipe wall, and corrosion resistance of the material.
Changes in shape, geometry, and materials can help mitigate erosion and erosion-corrosion. Examples include increasing the pipe diameter to reduce velocity, streamlining bends to reduce impingement, and using replaceable impingement baffles
4. Polythionic Acid Stress Corrosion Cracking
Intergranular stress corrosion cracking can occur in sensitized austenitic stainless steels and some Ni alloys when the sulfide scale formed on the surface during operation is exposed to air and moisture. The combination of sulfide scale, air (i.e. oxygen), and moisture creates sulfur acids on the surface that then cause polythionic acid stress corrosion cracking (PTA SCC). It normally occurs during shutdowns or start-ups, adjacent to welds or in high-stress areas. Cracking may propagate rapidly through the wall thickness of piping and components in a matter of minutes or hours.
In Hydroprocessing Units, Feed Heater tubes, hot feed-reactor effluent exchanger tubes, reactors, associated piping, and bellows are prone to Polythionic Acid SCC.
Preventive measures to minimize or eliminate PTA SCC include (i) flushing the equipment during or immediately after shutdown with alkaline or soda ash solution to neutralize the acids formed after shutdown and exposure to air and moisture or (ii) purging or preserving with dry nitrogen or nitrogen/ammonia during the shutdown to prevent air exposure.
5. High-Temperature Hydrogen Attack
High-temperature hydrogen attack (HTHA) results from exposure of steels to hydrogen gas at elevated temperatures above 204 °C and pressures above 15.17 MPa. At elevated temperature molecular Hydrogen dissociates into the atomic form which can readily diffuse through the steel. Hydrogen molecule reacts with carbon in the steel to form CH4 methane. If diffusion of carbon to the surface is limited, CH4 is formed internally from internal decarburization. Internal CH4 cannot diffuse through the steel. As a result, internal CH4 pressure builds up, initially forming bubbles or cavities, then micro fissures, and finally fissures that may combine to form cracks.
Combined feed exchangers, reactor effluent exchangers and reactors in Hydrotreating and Hydrocracking units are susceptible to HTHA attack.
Using alloy steels with chromium and molybdenum will increase carbide stability, thereby minimizing CH4 formation and resistance to HTHA. Other carbide-stabilizing elements include tungsten and vanadium.
6. Hydrogen Embrittlement
Hydrogen embrittlement (HE) is the loss in strength, ductility, and fracture toughness of materials due to the penetration and diffusion of atomic hydrogen. HE can lead to brittle cracking and can occur during manufacturing, welding, or from services that charge hydrogen into the metal.
In service at high-temperature above 205 °C molecular hydrogen dissociates to form atomic hydrogen that can diffuse into the metal. Heavy wall equipment in hot hydrogen service typically requires controlled shutdown and start-up procedures to control the pressurization sequence as a function of temperature.
In Hydroprocessing units, combined feed exchangers, and reactors are places to get Hydrogen embrittlement attacks. Maintaining Minimum Pressurization while startup and shutdown is the key to saving the equipment.
7. Ammonium Bisulfide Corrosion
In hydroprocessing reactors, nitrogen in the feed is converted to ammonia and reacts with H2S to form NH4HS. NH4HS precipitates out of the vapour phase in the reactor effluent stream when temperatures drop to within the range of 50~65 °C, depending on the concentration of NH3 and H2S, and may cause fouling and plugging in reactor effluent air-cooled exchanger unless washed away with sufficient quantity of wash water.
NH4HS corrosion can cause failures in air cooler header boxes, inlet outlet piping, reactor effluent final heat exchanger tubes, reactor effluent separator, its sour water boot piping, separated gases line containing entrained sour water vapours and stripper column overheads.
Control Measures to Avoid NH4HS Corrosion
- Injection of a sufficient amount of washing water, controlling Nitrogen in the feed and also the concentration of NH4HS in sour water of high-pressure separator boot less than 8 %.
- Symmetrical and hydraulically balanced flow in and out of air-cooled exchangers.
- Use resistant materials of construction (e.g. duplex stainless steel, Alloy 825) at velocities above 20 fps (6 m/s), depending on NH4HS concentration
- Properly design and maintain water wash injection with low oxygen content; provide sufficient excess water to ensure that an adequate amount of water remains as liquid to dilute the NH4HS salts.
- Use proper injection spray nozzles and metallurgy.
8. Ammonium Chloride Corrosion
Ammonium chloride salts may precipitate from high-temperature streams as they are cooled, depending upon the concentration of NH3 and HCl, and may corrode piping and equipment at temperatures well above the water dew point.
NH4Cl salting has been observed up to approximately 205 °C in reactor effluent exchangers and air-cooled exchangers. Ammonium chloride salts are hygroscopic and readily absorb water. A small amount of water can lead to very aggressive corrosion. Ammonium chloride is highly water soluble, highly corrosive, and forms an acidic solution when mixed with water.
Control Measures to NH4Cl Corrosion
- Monitor and control chlorides in the liquid and make-up gas feeds to the reactor.
- A continuous or intermittent water wash may be required in the reactor effluent stream to flush out the salt deposits or prevent them from forming.
- Monitoring of the feed streams and effluent waters will give an indication of the amount of ammonia and chlorides present.
- Process simulation also be used to determine the concentrations and dew point temperatures of NH4Cl. If the ammonium chloride salt deposition temperature has been calculated, temperature monitoring and control may be effective for maintaining metal temperatures above the salt deposition temperature
9. Hydrochloric Acid Corrosion
Hydrochloric acid (aqueous HCl) causes both general and localized corrosion and is very aggressive to most common materials of construction across a wide range of concentrations.HCL Damage is most often associated with dew point corrosion in which vapours containing water and hydrogen chloride condense from the overhead stream of a distillation, fractionation, or stripping tower. The first water droplets that condense can be highly acidic (low pH) and promote high corrosion rates.
The severity of corrosion increases with increasing HCl concentration and temperature. Aqueous HCl can form beneath deposits of ammonium chloride or amine hydrochloride salts in exchangers and piping. The deposits readily absorb water from the process stream or from injected wash water. Hydrogen chloride gas is normally not corrosive in dry process streams but becomes very corrosive where water is available to form hydrochloric acid.
Chlorides may enter the unit as inorganic or organic chloride in the hydrocarbon feed, or with the makeup hydrogen gas from Naphtha Reforming Unit, and react to form HCl.
Avoiding HCl Formation
- Chlorides in H2 streams should be minimized (e.g. by installing scrubbers or guard beds to remove Chlorides from hydrogen produced in catalytic reforming units.
- Corrosion-resistant nickel-based alloys should be used where necessary.
- The pH of water drawn from fractionator and stripper tower overhead drums in hydroprocessing and catalytic reformer units should also be checked regularly.
Top References
- Hydroprocessing for Clean Energy By Frank (XIN X.) ZHU, RICHARD HOEHN, VASANT THAKKAR, EDWIN YUH
- API932B, API-571-2020, API939C-2019
- NACE SP0170
- Corrosion Problems and Solutions in Oil Refining and Petrochemical Industry by Alec Groysman
- Wash Water Injection in Hydroprocessing Units
For further information, discussion and queries please comment in the box below or contact admin@, or follow us on Facebook & LinkedIn.