A Visbreaking (means viscosity breaking) unit is a processing unit in a petroleum refinery that reduces the viscosity of a refinery residue and produces more valuable petroleum products. The Visbreaking process is a non-catalytic thermal cracking process that transforms the atmospheric or vacuum residues to gas, naphtha, distillate, and mainly fuel oil blending components. Visbreaking reduces the quantity of cutter stock requirement to meet the specifications of fuel oil thus reducing the overall quantity of furnace oil.
Objectives of Visbreaking Unit
- Visbreaking unit reduces the viscosity of the residual stream which reduces the required quantity of high-quality and high-value distillates to meet the fuel oil viscosity specifications.
- Converts residues feedstock to distillates and other lighter products, which can be further treated and blended with refined products.
- Reduces the overall production of residual fuel oil by the refinery while reducing the pour point and viscosity of the fuel oil.
The conversion of the residues is achieved by heating the residue feedstock at high temperatures in a furnace. The process fluid is passed through a soaking zone, located either in the furnace or in an external drum, under controlled temperature and pressure. The heater effluent is then quenched with a quenching medium to stop the reaction.
Atmospheric vacuum residues and Solvent Deasphalter bottoms are typical feeds of the Visbreaking unit and transform to gas, gasoline, gas oil, and Visbroken bottom residue depending on the process severity and feedstock characteristics. It is one of the bottom of the barrel upgradation technique in petroleum refineries.
Product stability of the visbreaker residue is the main concern in selecting the severity of the visbreaker operating conditions. Increasing visbreaking severity and conversion will initially lead to a reduction in the visbroken fuel oil viscosity. However, fuel oil stability will decrease as the level of severity increases beyond a certain point.
Types of Visbreaking Process
There are two types of Visbreakers;
- Coil Visbreaking, Foster Wheeler, and UOP are the Technology providers in which thermal cracking occurs in the coil of the furnace,
- Soak Visbreaking, in which cracking occurs in a soak drum or vessel. The soaker process is licensed by Shell. Foster Wheeler has engineered a number of these types of visbreakers as well.
Coil Visbreaking Process
The Coli Visbreaking process achieves conversion by high-temperature cracking within a dedicated soaking coil in the furnace. Coil visbreaking is described as a high-temperature, short-residence-time conversion process.
Heating of the material to predetermined heater outlet temperatures and rapid quenching of furnace outlets facilitates the thermal cracking and altered viscosity necessary for further processing.
The feedstock is introduced into the heated coil in the furnace and slightly cracked. Reaction temperatures range from 450 to 495 °C while working pressures range from 3 to 20 bar.
After exiting from the furnace, the visbroken products are quickly quenched to stop the cracking reactions. To avoid coking in the fractionation tower, the quenching phase is crucial. The most frequent quenching streams are gas oil and Visbreaker residue.
After quenching, the effluent is transferred to the fractionator’s lower section, where it is flashed. The fractionator separates the yield into gas, gasoline, gas oil, and Visbreaker tar (residue). The fractionated gas oil is steam stripped to remove volatile components before being mixed with the Visbreaker bottoms or routed for further processing, such as hydrotreating, catalytic cracking, or hydrocracking.
The main advantage of the coil-type design is the two-zone fired heater. This type of heater provides a high degree of flexibility in heat input, resulting in better control of the material being heated. With the coil-type design, decoking of the heater tubes is accomplished more easily by the use of steam-air decoking.

Soaker Visbreaking Process
The soaker-type VB process is very similar to the coil-type process except the conversion is proceeded mainly in a vessel called Soaker after the heater. It achieves some conversion within the heater. However, the majority of the conversion occurs in a reaction vessel or soaker which holds the two-phase effluent at an elevated temperature for a predetermined length of time. Soaker visbreaking is described as a low-temperature, high-residence-time route.
The soaker drum design allows the heater to operate at a lower outlet temperature by providing the residence time required to achieve the desired cracking reactions. This lower heater outlet temperature results in lower fuel cost which is the advantage over the coil-type visbreaking process. The basic configuration of the Soaker Process includes the heater, soaker, and fractionators, and a vacuum tower can also be applied to recover more distillate products.
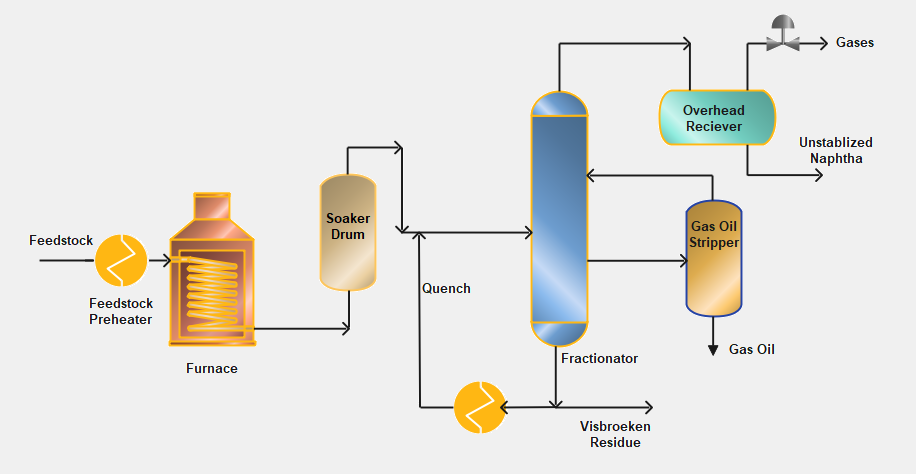
Coil visbreaking produces slightly more stable visbreaker products, which are useful for some feedstocks and applications. Soaker cracking often involves less capital investment, uses less energy, and has longer on-stream durations. Product qualities and yields from the coil and soaker drum design are essentially the same at a given severity and are independent of the visbreaker configuration.
Top References
- Springer Handbook oƒ Petroleum Technology Hsu Robinson (Editors).
- Fundamentals of Petroleum Refinery by M.A Fahim.
- Handbook of Petroleum Processing, 2nd Edition by Steven A. Treese, Peter R. Pujado, David S. J. Jones.
- Handbook of Petroleum Refining by James G. Speight.
For further information, discussion and queries please comment in the box below or contact us at admin@ or follow us on Facebook & LinkedIn.