Process Safety Management (PSM) is a system used to stop major accidents in industries that deal with dangerous materials. It focuses on being prepared, managing risks early and making the whole system stronger. PSM brings together people, engineering practices and industrial processes to avoid both small injuries and big disasters. Events like Bhopal, Piper Alpha and the Flixborough explosion show how important PSM is for saving lives, protecting the environment and keeping a company’s reputation safe.
What is Process Safety Management?
Process Safety Management (PSM) is a management system that is used to handle processes involving highly hazardous chemicals or materials. It identifies, assess and control risks in facilities handling hazardous substances like flammable liquids, toxic chemicals or high energy processes. It is not just about keeping workers safe but also preventing large scale incidents like explosions, fires or toxic releases that could harm employees, communities and the environment. From research and design to operation and maintenance, PSM ensures that hazards are controlled to protect people, property and the environment. It addresses the following key questions:
- What could go wrong in a process?
- How severe could the consequences be?
- How likely is an incident?
- What steps can prevent or mitigate risks?
This approach ensures that high risk industries like chemical plants, refineries and oil and gas facilities operate with minimal risk.
Why Process Safety Management Matters (Learning it from History)
The importance of Process Safety Management (PSM) becomes clear when we look at past industrial disasters. The Bhopal gas leak (1984) released methyl isocyanate, killing thousands due to inadequate safety measures. The BP Texas City explosion (2005) claimed 15 lives from a startup error and weak safety culture. The Piper Alpha disaster (1988), a platform fire that killed 167 people, cost $2.5 billion due to maintenance and protocol failures. These tragedies highlight PSM’s role in preventing human, environmental and economic losses, ensuring compliance with regulations like OSHA’s PSM Standard and encouraging a safety-first culture.
The Evolution of Process Safety Management
PSM has grown over the years by learning from past accidents. Big disasters like the Flixborough explosion in 1974 (caused by a badly designed bypass) and the toxic dioxin release in Seveso in 1976 led to major safety changes around the world. These events pushed for new rules, like the Seveso Directive in 1982 and the creation of the Center for Chemical Process Safety (CCPS) in 1985. In the U.S., after accidents like the Phillips explosion in 1989, OSHA introduced a safety rule in 1992 with 14 key requirements. Later in 2007, the CCPS introduced a new safety approach with 20 elements grouped under four main pillars.
- Commit to Process Safety: Fostering a strong safety culture and leadership.
- Understand Hazards and Risks: Identifying dangers using tools like HAZOP.
- Manage Risk: Implementing controls and emergency planning.
- Learn from Experience: Investigating incidents for continuous improvement.
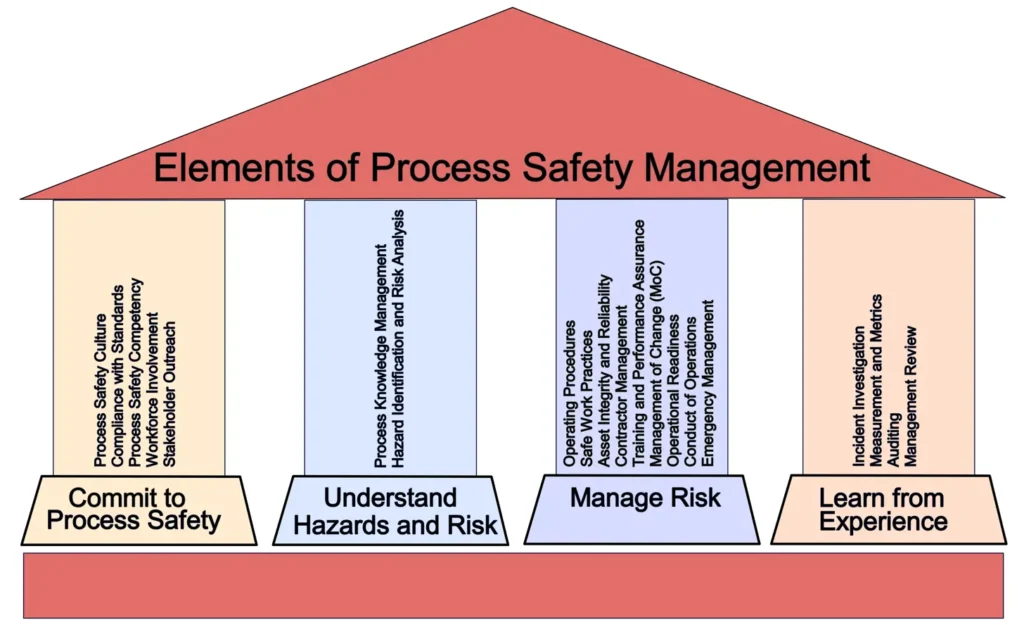
Elements of Process Safety Management
Commit to Process Safety includes:
- Process Safety Culture: It is an essential element of PSM focusing on safety first over other aspects. It requires committed leadership, open communication and learning from mistakes to avoid disasters.
- Compliance with Standards: Adherence to codes (e.g., OSHA) to ensures safe engineering practices.
- Process Safety Competency: Training and knowledge sharing prevent incidents.
- Workforce Involvement: Engaging of all the associated staff to enhances safety.
- Stakeholder Outreach: Sharing best practices with industry and communities.
Understand Hazards and Risk comprises:
- Process Knowledge Management: Involves compiling, cataloging and maintaining data on processes, chemicals and equipment such as Safety Data Sheets. It goes beyond data collection to ensure understanding and accessibility of this knowledge.
- Hazard Identification and Risk Analysis (HIRA): It encompasses activities to identify hazards and assess risks throughout a facility’s lifecycle using methods like HAZOP.
Manage Risk includes:
- Operating Procedures: Written guidelines for safe operations.
- Safe Work Practices: Procedures like lockout-tag-out prevent incidents.
- Asset Integrity and Reliability: Equipment maintenance on time prevents any mishap.
- Contractor Management: Ensures contractors or third-party people follow safety protocols.
- Training and Performance Assurance: Focus on training and emergency response to ensure high human reliability.
- Management of Change (MOC): Assesses risks from changes.
- Operational Readiness: Verifies safe startups, vital in refinery turnarounds.
- Conduct of Operations: Ensures consistent performance.
- Emergency Management: Plans for crises.
Learn from Experience involves:
- Incident Investigation: Identifies causes.
- Measurement and Metrics: Tracks PSM effectiveness.
- Auditing: Detects gaps.
- Management Review: Drives continuous improvement.
How often should PSM audits be conducted?
PSM audits should typically be conducted every three years, as required by OSHA’s PSM Standard for facilities handling hazardous chemicals. However, companies with a history of near misses or incidents might do audits more often to be extra careful. Some companies also have their own rules that require more frequent audits to make sure safety measures are working well. These regular checks help find problems early and keep safety a top priority.
The Three Models of Process Safety Management
PSM combines three models for comprehensive safety:
1. The Person Model
This model emphasizes individual behavior using training, audits and injury statistics to prevent errors. Frank Birk’s accident pyramid (1 serious injury, 10 minor injuries, 30 property damages, 600 near misses) highlights the need to address minor issues to prevent major ones.
2. The Engineering Model
Focusing on system design, this model uses Hazard Operability Studies (HAZOP), Probabilistic Risk Assessments (PRA), and Cognitive Task Analyses to create reliable, intuitive systems. The ARCO Channelview explosion (1990) showed how poor interface design can lead to errors.
3. The Organizational Model
This model views accidents as systemic failures, addressing latent conditions like inadequate maintenance. Inspired by Man-Made Disasters by Barry Turner, it emphasizes safety barriers. The Deepwater Horizon blowout (2010), killing 11, underscored the need to learn from near misses.
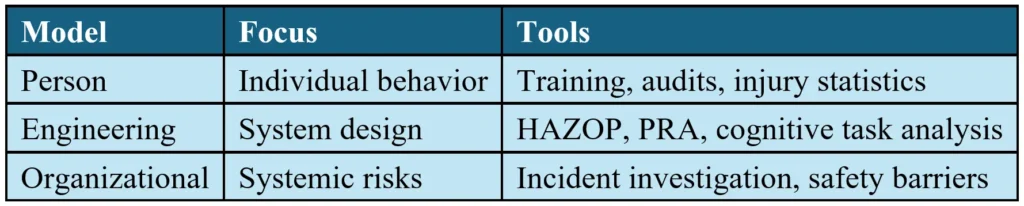
Roles and Applications of Process Safety Management
PSM is a team effort where everyone plays their role. Engineers check for potential hazards, operators stick to safety procedures and management works to create a strong safety culture. It applies to:
- Chemical Plants: Managing flammable materials with redundant systems.
- Oil and Gas: Preventing leaks or explosions via audits.
- Petroleum Refineries: Ensuring proper siting and training.
- Research Facilities: Handling reactive chemicals.
How can industries improve their PSM programs?
Industries can make their PSM programs better by building a strong safety culture where everyone puts safety first. Doing regular checks helps find and fix problems in the system. Giving proper training makes sure workers know the risks and follow the rules. Looking back at past accidents or near misses helps improve things over time. Good communication and strong support from leaders are also important to keep safety a top priority.
Challenges in Process Safety Management Implementation
PSM faces hurdles like:
- Resource Constraints: Audits and training demand significant resources.
- Complex Processes: Large facilities require modified strategies.
- Cultural Resistance: It’s hard to build a safety-first culture when people aren’t fully committed or open to change.
Companies must invest in training and encourage open communication to overcome these.
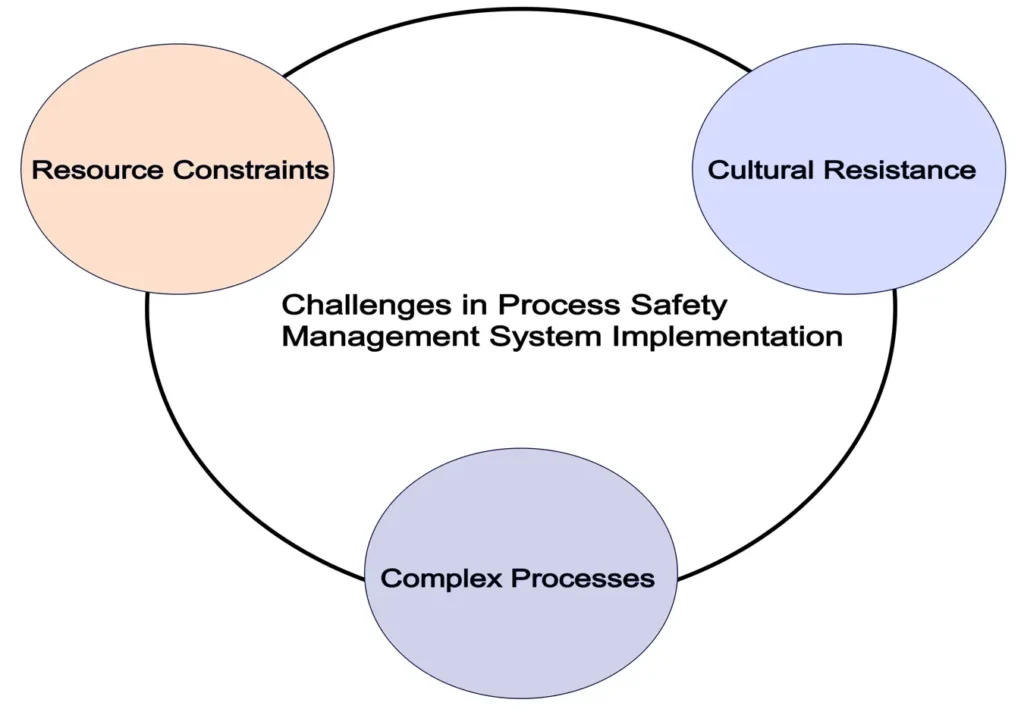
Common Myths About Process Safety Management
- Low Injury Rates Mean a Safe System: Low Lost-Time Injury Frequency (LTIF) does not ensure protection against major incidents. Non-injury events like leaks are critical.
- PSM Only Applies to Physical Hazards: PSM principles extend to any high-risk system including financial sectors.
- Human Error is the Main Cause: Systemic issues, like poor design, often drive errors.
References:
- CCPS (Center for Chemical Process Safety). Process Safety for Engineers: An Introduction. Wiley, 2022.
- CCPS (Center for Chemical Process Safety). Guidelines for Auditing Process Safety Management Systems. Second Edition. American Institute of Chemical Engineers, 2011.
- American Institute of Chemical Engineers, Center for Chemical Process Safety. Introduction to Process Safety for Undergraduates and Engineers. 2016.
- Reason, J. Managing the Risks of Organizational Accidents. Ashgate Publishing, 1997.
- Mannan, S., Lees, F. P. Lees’ Loss Prevention in the Process Industries: Hazard Identification, Assessment, and Control. Elsevier Butterworth-Heinemann, 2005.
- https://www.osha.gov
- https://ei1.com