Catalytic cracking of heavy hydrocarbons in the presence of hydrogen is known as hydrocracking. The hydrocracking process converts heavy, high-boiling petroleum feedstock into lighter products (naphtha, kerosene, diesel, etc.) or high-quality lubricating oils. The hydrocracking process breaks the C-C bonds along with the hydrogen saturation of heavy feedstock in the presence of a catalyst under high hydrogen partial pressure and at severe operating conditions.
Hydrocracking unit in petroleum processing plays a key role and provides high-quality transportation fuels by upgrading low-quality feedstocks. Presently, the hydrocracking unit is the backbone of petroleum refineries, because no refinery can survive without a hydrocracking unit due to stringent environmental regulations. It is commonly applied to upgrade the heavier fractions of crude and vacuum distillation units including residue.
The major advantage of the hyrocracking process is its flexibility to process a variety of refinery feed streams. The major product of the hydrocracking unit is the middle distillate but other good quality products are also produced. The product boiling ranges and quantity can be varied by controlling process variables, catalytic conversion, and catalyst modification. The table shows the ranges of feeds and products in the hydrocracking process.
Feeds | Products |
Vacuum Gas Oils | LPG, light gases |
Heavy and Light Coker gas oils | Heavy and light naphtha |
Thermal gas oils | Jet fuel, Kerosene |
De-asphalted gas oil | Diesel fuel |
FCC light and heavy cycle oils | Low-sulfur fuel oil |
Vacuum and atmospheric residue | Olefin, FCC, ethylene cracker, and petrochemical feedstocks |
Asphalt, tar sands | Lube oils |
The final products obtained from hydrocracking are of good quality and serve as an excellent blending component with other refinery products. The light naphtha has octane numbers 75~85 and the heavy naphtha is high-quality reformer feedstock. Similarly, jet fuel is low in aromatics with a high smoke point, diesel fuel is low in sulfur with a relatively high cetane number, and fuel oil is low in sulfur.
In the hydrocracking unit, mainly multiple fixed beds reactor with a downward flow is applied. The hydrocracking reactor is similar to a typical hydrotreating reactor and is a cylindrical vessel with an inlet diffuser, top distribution tray, catalyst support grid, quench gas mixing section, and outlet collector. More detail about hydroprocessing reactors can be viewed in my previous blog ‘‘ Hydrotreating Reactor Internals”.
Hydrocracking Reactions
The cracking reactions are endothermic while the hydrogenation reactions are of exothermic nature. Hydrocracking feedstock is retreated by hydrotreating prior to hydrocracking in the same reactor or an additional upstream reactor. Hydrotreating reactions saturate unsaturated compounds and perform hydrodesulfurization, denitrogenation, metals removal, olefin saturation, hydro deoxidation, etc.
During hydrocracking, there are two main chemical reactions occurring; 1. catalytic cracking of heavy hydrocarbons into lighter unsaturated hydrocarbons, and 2. the saturation of these newly formed hydrocarbons with hydrogen. Further, hydrocracking reactions, isomerization of paraffin, hydro de-cyclization, hydrodealkylation, and aromatics saturations also take place.
Hydrocracking Catalysts
Hydrocracking catalysts are dual-functional catalysts; the hydrogenation-dehydrogenation function is provided by metals, and the cracking function is provided by acidic support materials.
The acidic support can be 1. amorphous oxides (e.g. silica-alumina), 2. a crystalline zeolite plus binder (e.g. alumina), or 3. a mixture of crystalline zeolite and amorphous oxides. The metals can be; 1. noble metals (palladium, platinum) or 2. non-noble metals in the sulphided from Group VIA (molybdenum, tungsten) and group VIIIA (cobalt, nickel).
The Acidic Support | Metals Catalyst |
1. Amorphous oxides (e.g. silica-alumina)
2. Crystalline zeolite plus binder (e.g. alumina) 3. Mixture of crystalline zeolite and amorphous oxides |
1. Noble metals (palladium, platinum)
2. non-noble metals in the sulphided from Group VIA (molybdenum, tungsten) and group VIIIA (cobalt, nickel) |
Key Operating Conditions
Operation of the hydrocracking unit within the set operating conditions is very critical for a longer cycle length of the catalyst. Some key operating conditions of the hydrocracking unit are; operating temperature: 300~450 C, operating pressure: 60~200 bar, liquid hour space velocity: 0.5~2.5, Hydrogen to hydrocarbon ratio: 500~1600 NM3/m3 of feed, hydrogen consumption: 200~600. High hydrogen partial pressure plays a vital role to reduce the rate of coking and deactivation of the hydro-cracking catalysts. Please also view the blog ” Key Operating Variables of Hydrocracking Unit”.
Types of Hydrocracking Processes
The flow scheme of the hydrocracking process is very similar to the typical hydrotreating process with some exceptions. The hydrocracking process is categorized into the single-stage reaction system and the two-stage reaction system, based on the flow scheme through the hydrocracking reactor. In general, the single-stage reactor system is used for producing kerosene and diesel oil with less conversion (30~80%), and the two-stage reactor system is for complete conversion of the feedstock, thus increasing the yield of the middle distillate oils.
Mild and Conventional Hydrocracking Processes
Another category of the hydrocracking process is based on the severity of the process i.e. conventional hydrocracking and Mild Hydrocracking.
Mild hydrocracking is a less severe process used to produce relatively high yields of lighter products by using less severe operating conditions as compared to conventional hydrocracking. The major difference between the two processes is the hydrogen partial pressure at which they operate; mild hydrocrackers operate at 30~70 bar pressure while conventional Hydrocracking at 100~200 bar pressure. Further, mild hydrocracking is a once-through process whereas most conventional hydrocrackers recycle the unconverted oil. The lower hydrogen partial pressure in mild hydrocracking leads to lower conversion (30~70%) and to less hydrogenated products. Mild Hydrocracking produces a large quantity of low-sulfur fuel oil and smaller quantities of middle distillates. Furthermore, Conventional hydrocracking can achieve the total conversion of feedstock but cannot be achieved with mild hydrocracking.
Single-Stage Hydrocracking Process
The hydrocracking process description of a single-stage reactor system is further categorized into the complete conversion system by recirculating the unconverted oil called a recycle hydrocracking process, and the one-through system that partially converts the oil without re-circulation called a once-through hydrocracking process. For a recycle hydrocracking process, the fractionator bottom is recycled back to the reactor to increase the conversion.
In a single-stage hydrocracking process, the fresh feed (oil & gas) is preheated by heat exchange with reactor effluent streams and finally by a fired heater before entering one or two reactors. The first section of the reactor is often packed with a guard and hydrotreating catalyst to protect the more sensitive cracking catalyst further down in the reactor from impurities of sulfur, nitrogen, and metal poisoning.
Hydrocracking reactors normally contain two or more catalyst beds. Quench gas is provided to maintain equal temperatures across the catalyst beds. The reactor effluent is cooled and partially condensed by heat exchange before entering the high-pressure separator.
A gas stream rich in hydrogen is separated and recycled back to the reactor as recycle gas after treatment with amine by removing H2S. The hydrocarbon liquid phase from the high-pressure separator is first sent to the stripper to remove the lighter gases. Stripper bottom liquid enters the product fractionator where products are separated by fractionation and sent to storage.
In some configurations, the HP separator liquid is routed to a Low-pressure separator where a second gas stream is also flashed off. This will have a lower hydrogen content but will contain a higher content of C3 and C4 components. For this reason, the stream is often routed to an absorber column for maximizing LPG recovery. Both of the liquid hydrocarbon streams from high pressure and low-pressure separator are first sent to the stripper to remove the lighter gases. Stripper bottom liquid enters the product fractionator where products are separated by fractionation and sent to storage. The process flow diagram (PFD) of the hydrocracking single-stage once-through and recycle process is shown below.
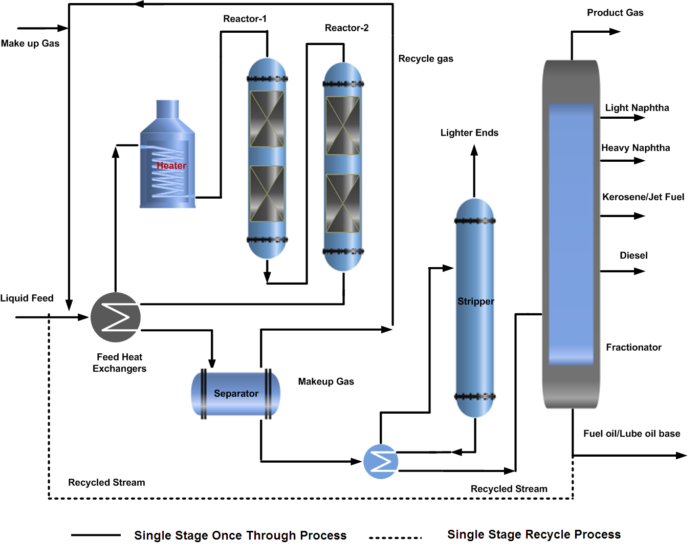
Two-Stage Hydrocracking Process
It is more complex as compared to single-stage hydrocracking. In two-stage hydrocracking, the bottom of the product fractionator is fed to the second stage of the hydrocracking reactor where the same process is repeated and the separated gases from the separator join the recycle gas stream while the liquid joins the stripper feed to remove lighter ends and then get separated in product fractional into products along with single-stage process stream.

Commercial Hydrocracking Processes
Different companies that license hydrocracking technology have trade names for their processes.
- UOP’s Unicracking Process
- ART/Chevron’s Isocracking Processes
- Shell, Shell Development Co.
- BASF-IFP Hydrocracking
- Axens High Conversion Hydrocracking
For further discussion and query please comment in the comment box below or contact admin@ OR follow us on Linkedin.com and facebook.com