A fired heater, or furnace, is a vital piece of equipment in oil refineries, used to heat crude oil or other fluids to high temperatures for processes like distillation or cracking. It works by burning fuels to create heat that is transferred to the fluid through special tubes. They’re designed for efficiency and safety, but poor operation can lead to costly issues or environmental problems. Proper design and maintenance are key to keeping them running smoothly and safely.
What Is a Fired Heater?
A fired heater or furnace is a direct-fired heat exchanger that uses the combustion of fuels (like natural gas or refinery gas) to heat process fluids, typically crude oil or intermediate streams, to high temperatures. These heaters are critical in processes like crude distillation, catalytic cracking, and hydrotreating, where precise temperature control is vital for efficiency and product quality. Unlike boilers, which generate steam, fired heaters transfer heat directly to the process stream.
Fired heaters operate by burning fuel in a combustion chamber, transferring heat through radiant and convective sections to tubes containing the process fluid. The design must balance efficiency, safety, and environmental compliance, as inefficiencies or malfunctions can lead to costly downtime, safety incidents, or emissions violations.
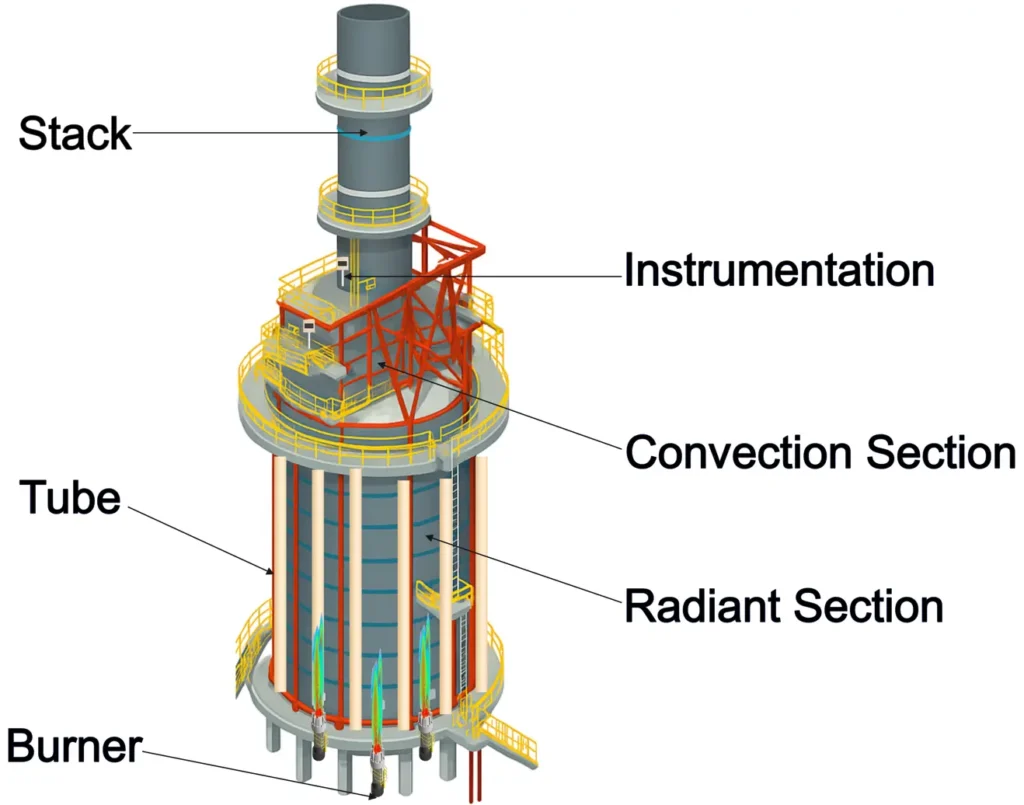
What is the difference between a boiler and a fired heater?
A boiler and a fired heater both generate heat, but they serve different purposes. A boiler creates steam by heating water, which is then used for power or heating elsewhere. A fired heater, on the other hand, directly heats process fluids, like crude oil, for refinery processes such as distillation or cracking. Boilers focus on steam production, while fired heaters target specific process streams. Fired heaters also operate at higher temperatures and are designed for precise heat control in refining operations.
What is refinery gas?
Refinery gas is a mix of light gases produced as a byproduct during various refining processes. It typically contains gases such as methane, ethane, propane, and butane, which can be used as fuel. Refinery gas is often burned in fired heaters because it’s readily available and cost-effective. Using it helps refineries reduce reliance on external fuels like natural gas, improving efficiency and lowering costs.
Types of Fired Heaters
They come in different designs; each suited for specific needs. Here are the main types:
- Vertical Cylindrical Heater: These are tall, tube-shaped heaters that save space. Burners at the bottom heat tubes arranged in a circle. Heat moves up through radiant and convective sections. They’re great for smaller processes due to their compact design and ease of maintenance.
- Box-Type Heater: Shaped like a big rectangular box, these handle heavy-duty tasks like crude distillation. Tubes run along the walls, with burners at the bottom or sides. They have a high heat capacity but need careful design to avoid uneven heating.
- Cabin-Type Heater: Similar to box-type but with a sloped, cabin-like roof, these ensure even heat distribution. They’re used for processes like hydrotreating and are efficient for large scale operations but need more space.
Each type is chosen based on the refinery’s space, process requirements, and efficiency goals. Modern designs focus on better heat transfer and lower emissions to improve performance and safety.
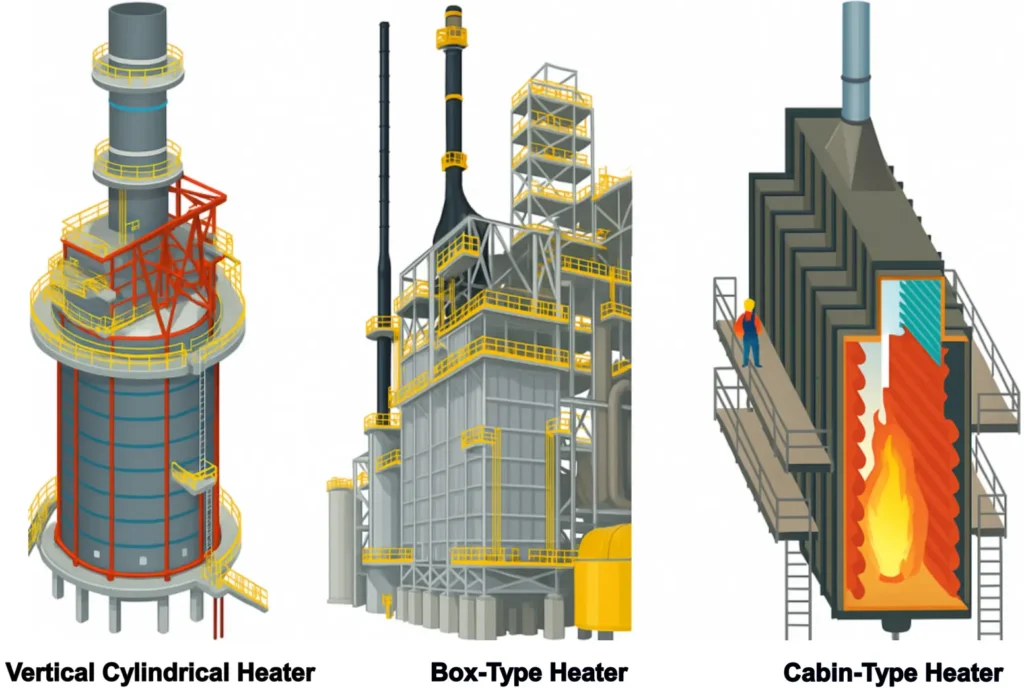
Why Are Fired Heaters Critical in Refineries?
Fired heaters are crucial because they:
- Enable Key Processes: Provide the high temperatures needed for distillation, cracking, and reforming.
- Impact Efficiency: Consume significant fuel, affecting refinery operating costs.
- Pose Safety Risks: Improper operation can lead to fires, explosions, or toxic emissions.
- Influence Emissions: Contribute to NOx, CO, and CO₂ emissions, requiring careful control to meet environmental standards.
Design and Components of Fired Heaters
Fired heaters come in various configurations, such as vertical cylindrical, box-type, or cabin-type, depending on the refinery’s needs. Their core components include:
- Burners: Initiate combustion, controlling flame shape and heat distribution.
- Radiant Section: Where most heat transfer occurs via radiation from the flame to the tubes.
- Convective Section: Recovers additional heat from flue gases, improving efficiency.
- Tubes: Carry the process fluid, designed to withstand high temperatures and corrosion.
- Stack: Releases flue gases, often equipped with dampers for draft control.
- Instrumentation: Includes sensors for temperature, pressure, and oxygen levels to ensure safe operation.
Fired heaters must be designed for thermal efficiency, typically achieving 80–90% efficiency by optimizing heat transfer and minimizing heat loss.
Key Design Considerations
- Heat Transfer: Balancing radiant and convective heat transfer to maximize efficiency.
- Fuel Selection: Using refinery byproducts (e.g., fuel gas) or natural gas to optimize costs.
- Tube Layout: Ensuring uniform heat distribution to prevent hot spots and tube failure.
- Draft Control: Maintaining proper airflow to optimize combustion and reduce emissions.
Poor design, such as inadequate tube spacing, can lead to flame impingement, causing tube damage and reduced heater lifespan.
Safety Challenges and Mitigation Strategies
Fired heaters are inherently hazardous due to high temperatures, flammable fuels, and complex control systems. Key hazards include:
- Fire and Explosion: Fuel leaks or improper combustion can ignite flammable vapors.
- Tube Rupture: Overheating or corrosion can cause tubes to fail, releasing hot fluids.
- Emissions: Incomplete combustion produces CO and NOx, posing health and environmental risks.
Safety Mitigation Layers
A modern approach to fired heater safety involves multiple protection layers:
- Process Control Systems: Automated controls monitor temperature, pressure, and fuel-air ratios to prevent unsafe conditions.
- Safety Instrumented Systems (SIS): Emergency shutdown systems activate during critical failures, such as high furnace pressure.
- Operator Training: Well-trained operators are critical for recognizing and responding to abnormalities.
- Maintenance and Inspection: Regular inspections detect tube corrosion or burner issues before they escalate.
- Burner Management Systems (BMS): Ensure safe startup, operation, and shutdown, preventing fuel accumulation.
A notable example is the 1989 Pasadena refinery explosion, where a fired heater-related failure contributed to a catastrophic incident, underscoring the need for robust safety protocols.
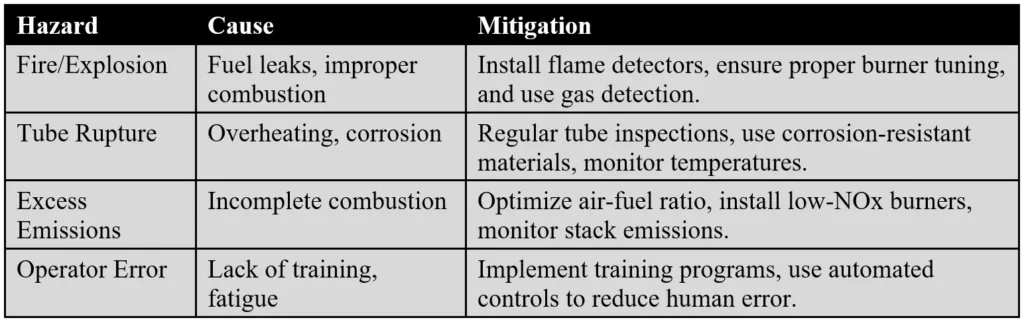
What is burner management system in fired heater?
A Burner Management System (BMS) in a fired heater is an automated safety system that controls and monitors the burners to ensure safe operation. It manages the startup, operation, and shutdown of burners, preventing issues like fuel leaks or flameouts that could lead to fires or explosions. The BMS checks things like fuel flow, air supply, and flame stability, and it can trigger an emergency shutdown if something goes wrong. BMS is crucial for reducing risks and ensuring safe combustion in fired heaters.
Optimization Strategies for Fired Heaters
Optimizing fired heaters improves efficiency, reduces fuel consumption, and minimizes environmental impact. Some strategies are:
- Improve Combustion Efficiency: Adjust the air-fuel ratio to minimize excess air, reducing fuel waste. Studies show that a 10% reduction in excess air can improve efficiency by 1–2%.
- Use Low-NOx Burners: These reduce emissions while maintaining performance.
- Heat Recovery: Install economizers in the convective section to recover waste heat, potentially increasing efficiency by 5–10%.
- Advanced Controls: Implement predictive control systems to optimize burner operation dynamically.
- Tube Cleaning: Regular cleaning removes fouling, improving heat transfer efficiency by up to 3%
Modern fired heaters with advanced controls can achieve up to 92% thermal efficiency, significantly reducing operating costs.
Environmental and Regulatory Considerations
Fired heaters contribute significantly to refinery emissions, making compliance with environmental regulations. Strategies include:
- Low-NOx Burners: Reduce nitrogen oxide emissions by up to 50%.
- Flue Gas Treatment: Use scrubbers to remove sulfur compounds.
- Monitoring Systems: Continuous emission monitoring ensures compliance with OSHA and EPA standards.
Retrofitting older heaters with modern burners can reduce emissions while improving efficiency, a win-win for refineries.
Top References
- Gary, J. H., & Handwerk, G. E. (2007). Petroleum Refining: Technology and Economics. CRC Press.
- Anderson, J. B. (2010). Refinery Process Design. Wiley.
- Crowl, D. A., & Louvar, J. F. (2011). Chemical Process Safety: Fundamentals with Applications. Prentice Hall.
- Coker, A. K. (2018). Petroleum Refining Design and Applications Handbook. Wiley.
- Fanchi, J. R. (2016). Introduction to Petroleum Engineering. Wiley.
- https://seoulsolution.kr
- https://www.digitalrefining.com