A Coriolis flow meter is a highly accurate device that measures the mass flow of fluids, like liquids, gases, or slurries, using a fascinating principle called the Coriolis effect. Unlike traditional meters that focus on volume, it directly tracks mass, making it super reliable for industries like oil, food, or pharmaceuticals. By vibrating a tube and detecting how the fluid twists it, the meter delivers precise readings down to 0.1% error. It can also measure density and temperature, all in one go. Its versatility and low maintenance make it a top choice for demanding applications.
What is a Coriolis Flow Meter?
A Coriolis flow meter is a high-precision instrument that directly measures the mass flow rate of fluids (whether liquids, gases, or slurries) without relying on secondary factors like volume or pressure. Unlike traditional volumetric meters, it uses the Coriolis effect, a physics principle tied to the Earth’s rotation, to deliver accurate readings. Available in sizes from 1/25 inch to 10 inches, these meters handle everything from crude oil to chocolate syrup, making them indispensable in industries where precision is critical.
Why Choose Coriolis Flow Meters?
- Direct Mass Measurement: No need for extra sensors to adjust for temperature or pressure changes.
- Versatility: Works with a wide range of fluids, from corrosive chemicals to viscous liquids.
- High Accuracy: Achieves errors as low as 0.1-0.5% of the flow rate.
- Multi-Parameter Capability: Measures mass flow, density, and temperature in one device.
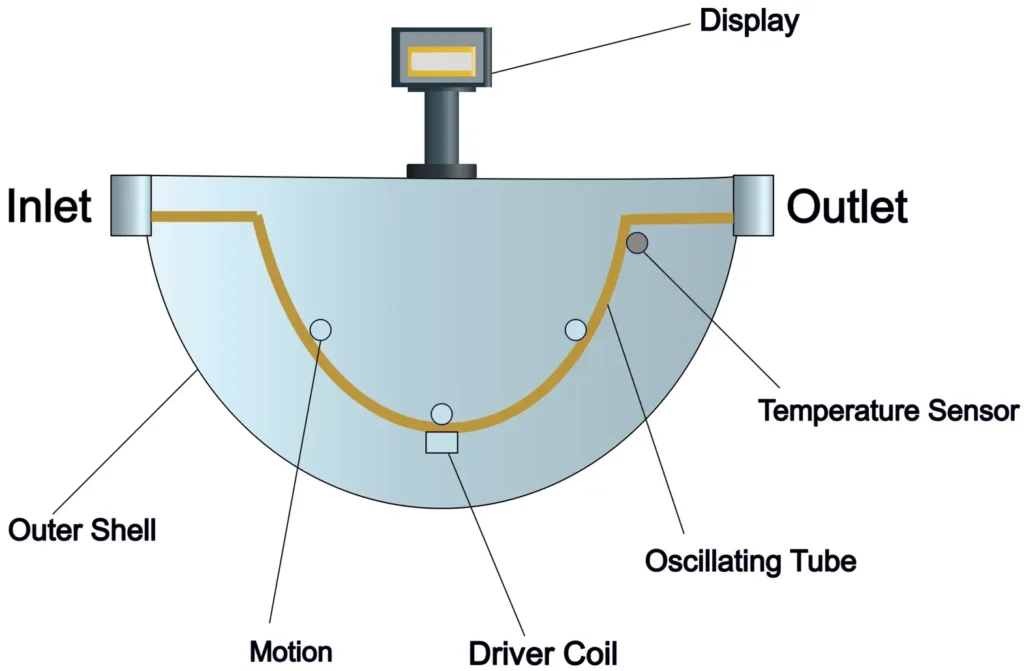
How Coriolis Flow Meters Work
The heart of a Coriolis flow meter is the Coriolis effect, which causes a vibrating tube to twist when fluid flows through it. This twist is directly tied to the fluid’s mass flow rate. Here’s a step-by-step look at the process:
- Tube Vibration: The meter features one or two tubes vibrated at their natural frequency by a drive coil, similar to a tuning fork. This requires minimal energy, often just a few milliamps.
- Coriolis Force: As fluid flows through the vibrating tube, it experiences a Coriolis force (F = 2m × v × Ω, where m is mass flow, v is fluid velocity, and Ω is the tube’s angular velocity). This force causes the tube to twist slightly.
- Twist Detection: Sensors (often electrodynamic, with a coil and magnet) measure the phase difference or time lag between the tube’s inlet and outlet halves. This lag, typically 60-120 microseconds, correlates to the mass flow rate.
- Density and Temperature: The tube’s vibration frequency shifts with the fluid’s density, enabling density measurement. Temperature sensors adjust for thermal effects on the tube’s properties, ensuring accuracy.
- Data Processing: A microprocessor converts sensor data into mass flow, density, and temperature readings, output as a 4-20 mA signal or frequency.
What is the Coriolis effect in flow measurement?
The Coriolis effect is a force experienced by a moving mass in a rotating system, causing it to deviate from a straight path. In flow meters, this force deforms vibrating tubes, and the deformation is measured to calculate the mass flow rate.
Why the Twist Matters in Coriolis Flow Meter?
The twist in the tube is the key to measuring mass flow. As the tube vibrates upward, the Coriolis forces are maximized at the mid plane and drop to zero at the peak. When the tube moves downward, the forces reverse, creating a rhythmic pattern. By measuring the time difference between the tube’s halves, the meter calculates the mass flow with high precision.
Beyond Mass Flow: Multi-Parameter Measurement
Coriolis flow meters measure not just only one parameter. They can measure:
- Density: By analyzing the tube’s oscillation frequency, which changes with the fluid’s density.
- Temperature: Using sensors like platinum resistance thermometers (PRT) for accurate readings, though placement can affect precision by up to ±2°C.
- Volumetric Flow: Calculated from mass flow and density.
- Viscosity: Some designs measure shear stress to estimate viscosity.
This multi-parameter capability makes them versatile for applications like custody transfer or monitoring complex fluids in chemical plants.
Design Variations: U-Tube vs. Straight Tube
Coriolis flow meters come in different designs, each suited to specific needs:
U-Tube Design:
- Features one or two U-shaped tubes vibrating in counterphase, like a tuning fork.
- Dual-tube designs cancel out external vibrations, improving accuracy.
- Ideal for high-precision applications, like pharmaceuticals or food processing.
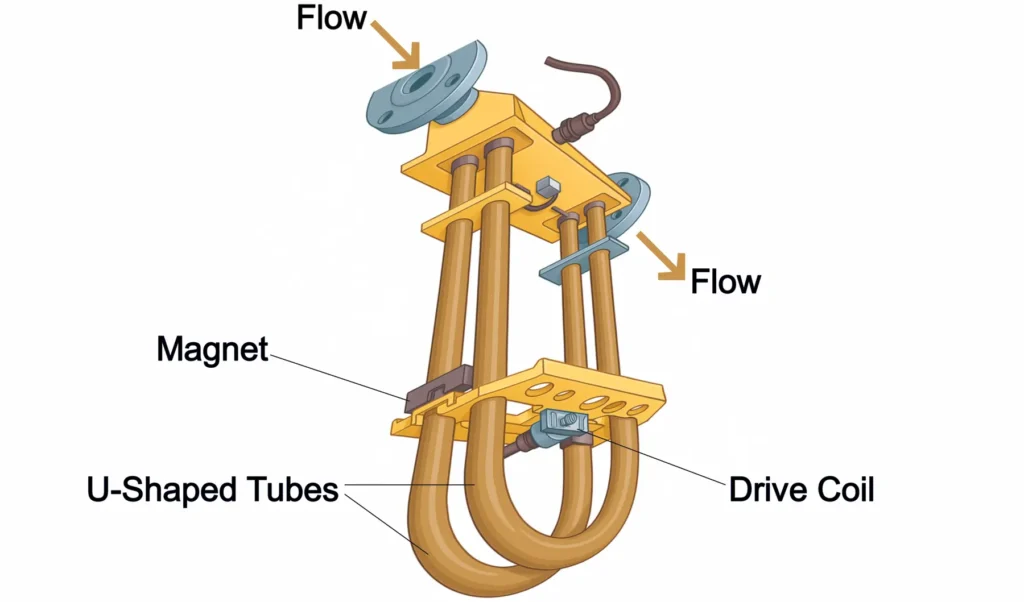
Straight-Tube Design:
- Uses a single straight tube, minimizing pressure loss.
- Compact and suitable for high viscosity or abrasive fluids.
- More sensitive to external vibrations, requiring robust mounting.
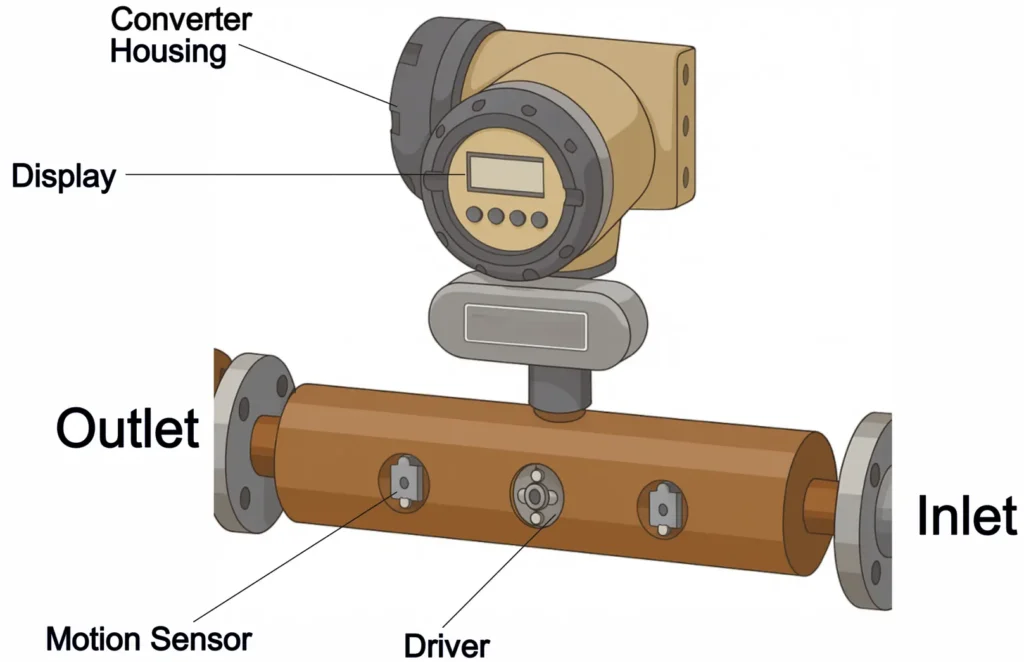
Tube Materials:
- Common materials include 316L stainless steel for durability, or corrosion-resistant options like Hastelloy, titanium, or zirconium for harsh fluids.
- Thin wall tubes enhance sensitivity for low velocity liquids or gases.
Key Applications in Industry
Coriolis flow meters shine in demanding environments due to their versatility and precision. Here are some key applications:
- Oil and Gas: Accurate custody transfer for crude oil, diesel, or jet fuel, unaffected by density variations.
- Chemical Processing: Handles aggressive fluids like sulfuric acid or adhesives, provided materials are compatible.
- Food and Beverage: Measures viscous liquids like honey, chocolate, or milk in sanitary designs.
- Pharmaceuticals: Ensures precise dosing for drug manufacturing.
- Pulp and Paper: Monitors coating or pulp slurries.
Advantages of Coriolis Flow Meters
These meters offer compelling benefits:
- Unmatched Accuracy: Errors as low as 0.1% for liquids, ideal for critical applications.
- Wide Range: Operates reliably from -50°C to 200°C and across various pressures.
- Low Maintenance: No moving parts in contact with fluid, reducing wear.
- Flow Profile Independence: No need for flow conditioners, as accuracy is unaffected by viscosity or density.
- Bidirectional Flow: Measures forward and reverse flows accurately.
- Low Power Use: Operates with minimal energy.
Limitations to Consider
Despite their strengths, Coriolis flow meters have drawbacks:
- High Cost: More expensive than volumetric meters, though justified when density measurement is needed.
- Temperature Limits: Not suitable for fluids above 420°C.
- Two-Phase Flow Challenges: Errors can reach 4-10% in gas-liquid mixtures, like oil-water with 30% water-cut.
- Size Constraints: Limited to 10-inch pipelines; larger flows require parallel units.
- Gas Sensitivity: Low-density gases need high velocities, causing pressure drops.
Installation and Maintenance Tips
To maximize performance, follow these guidelines:
- Keep Tubes Full: For liquids, install vertically with upward flow to avoid gas bubbles. For gases, avoid low points to prevent liquid buildup.
- Vibration Isolation: Use flexible piping and robust supports, especially for single tube designs.
- Calibration: Perform zero and span adjustments at operating temperature. Recalibrate for significant temperature changes.
- Monitor Wear: Corrosive fluids can thin tubes, affecting accuracy. Single-tube designs are less prone to wear.
- Avoid Build-Up: Tube coatings can restrict flow, reducing range and accuracy.
What is the difference between Coriolis flow meter and orifice meter?
Coriolis flow meters directly measure mass flow using the Coriolis effect, where fluid twists a vibrating tube, offering high accuracy (0.1-0.5% error) for liquids, gases, or slurries, with minimal maintenance. They also measure density and temperature but are pricier and less effective for two-phase flows. While Orifice meters measure volumetric flow via a pressure drop across an orifice, requiring extra sensors for mass flow and offering lower accuracy (~0.5%). They’re cheaper but prone to clogging with dirty fluids and have higher pressure loss. Coriolis excels in precision and versatility; orifice meters suit simpler, cost-sensitive applications with clean fluids.
References:
- Roger C. Baker – Flow Measurement Handbook: Industrial Designs, Operating Principles, Performance, and Applications (2016, Cambridge University Press)
- Spitzer, D. W. – Industrial Flow Measurement (2004, ISA: The Instrumentation, Systems, and Automation Society)
- Bela G. Liptak – Instrument Engineers’ Handbook, Volume 1, Fourth Edition, Process Measurement and Analysis (2003, CRC Press)
- Lipták, B. G. (Ed.) – Process Control: Instrument Engineers’ Handbook (1995, Butterworth-Heinemann Ltd)
- https://www.sciencedirect.com
- https://automationforum.co