In the dynamic world of process industries like chemical plants, petroleum refineries, and oil and gas facilities, achieving precise control over variables such as temperature, pressure, and flow is essential for safety, efficiency, and product quality. Cascade control and ratio control are transformative strategies for process industries, offering precision and efficiency in managing complex systems. Cascade control excels at rejecting disturbances through nested loops, while ratio control ensures consistent proportions for optimal performance.
What is Cascade Control?
If you are trying to maintain a steady temperature in a chemical reactor, but external factors like fluctuating coolant supply keep disrupting the process. A single feedback controller might lag, causing temperature swings. Cascade control steps in like a dynamic duo, using two controllers to tackle disturbances faster and keep the system stable.
How Cascade Control Works
Cascade control employs two loops:
- Primary Loop: Targets the main variable, such as the temperature of a process fluid in a reactor.
- Secondary Loop: Manages a related, faster-responding variable, like coolant flow rate, that influences the primary variable.
The primary controller sets a target for the secondary controller, which acts to correct disturbances before they significantly affect the main process. For example, in a heat exchanger, the primary controller monitors the outlet temperature and sets a setpoint for a secondary flow controller, which adjusts the steam valve to maintain the desired flow. This setup minimizes delays and ensures stability even when disturbances like steam pressure changes occur.
Example: Cascade Control in a Jacketed CSTR
In an exothermic Continuous Stirred-Tank Reactor (CSTR), maintaining a consistent reactor temperature is critical. A traditional feedback system might adjust coolant flow based on reactor temperature, but changes in coolant supply temperature could cause delays and fluctuations. With cascade control:
- The primary controller monitors the reactor temperature (T) and sets a target coolant temperature.
- The secondary controller adjusts the coolant flow rate (Q) to maintain the setpoint coolant temperature (Tc), responding quickly to supply changes.
This dual loop approach stabilizes the reactor temperature, ensuring consistent reaction conditions.
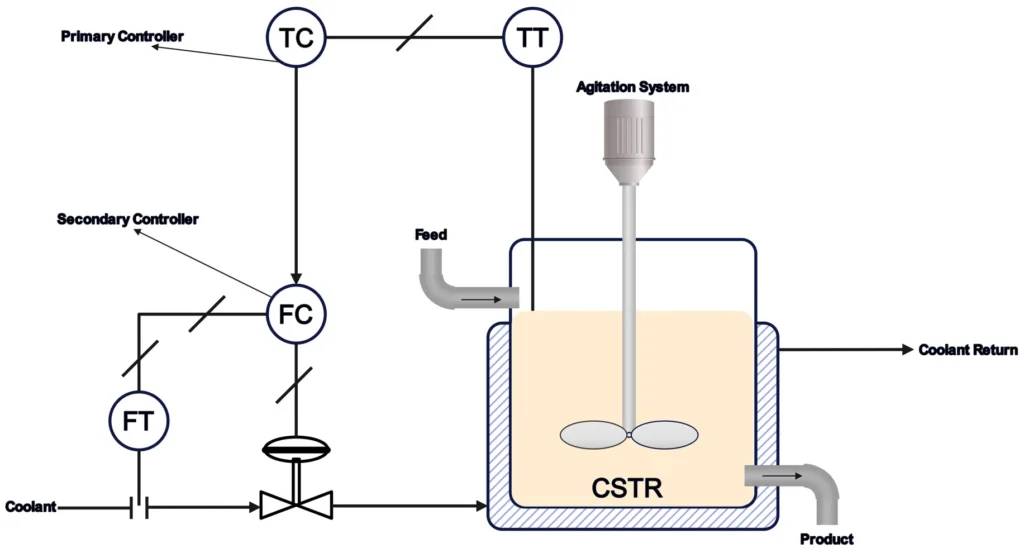
Benefits of Cascade Control
- Rapid Disturbance Rejection: The secondary loop corrects issues like pressure or flow changes before they impact the primary variable.
- Enhanced Stability: By addressing disturbances early, cascade control reduces oscillations and allows for more aggressive tuning of the primary controller.
- Improved Precision: The nested structure enables fine-tuned adjustments, ideal for complex processes with time lags.
Why is cascade control faster?
Cascade control is faster because it uses two controllers working together. The secondary controller quickly handles smaller, faster-changing disturbances, like changes in flow or pressure, before they affect the main variable, like temperature. This means the primary controller, which focuses on the main variable, doesn’t have to wait for the whole system to react. By catching issues early, cascade control reduces delays and keeps the process stable, making it more responsive than a single controller.
When to Use Cascade Control
Cascade control is most effective when the secondary loop is significantly faster, typically three times faster, than the primary loop. For instance, flow control is quicker than temperature control in a heat exchanger. It’s ideal when an intermediate measurement, like fuel flow in a furnace, can catch disturbances before they affect the primary variable, such as outlet temperature.
What is the main advantage of cascade control?
Cascade control quickly corrects disturbances in the secondary loop, minimizing their impact on the primary variable, leading to faster response times and improved stability.
What is Ratio Control?
Its like mixing ingredients for a perfect recipe, too much or too little of one component can ruin the result. Ratio control ensures that two process streams, like fuel and air in a combustion process, maintain a consistent proportion, optimizing efficiency and performance.
How Ratio Control Works
Ratio control adjusts one stream (the controlled variable) to maintain a fixed ratio with another (the wild or reference variable). For example, in a combustion system, the fuel flow might be the wild stream, and the air flow is adjusted to maintain an optimal air-to-fuel ratio, such as 10:1, for efficient burning.
There are two common methods:
- Method I: Measures the ratio of the two flows, compares it to the desired ratio, and adjusts the controlled flow using a PI controller. This can introduce nonlinear gain issues.
- Method II: Measures the wild stream, multiplies it by the desired ratio, and uses the result as the setpoint for the controlled stream’s controller. This method, preferred for its simplicity, avoids nonlinear complications.
Example: Ratio Control in Ammonia Synthesis
In ammonia synthesis, hydrogen (H₂) and nitrogen (N₂) must be fed in a 3:1 molar ratio for the reaction: 3H₂ + N₂ → 2NH3 A ratio control system measures the H₂ flow (wild stream) and multiplies it by the desired ratio (e.g., 3) to set the N₂ flow controller’s setpoint. If the H₂ flow increases, the N₂ flow adjusts automatically to maintain the ratio, ensuring optimal reaction conditions.
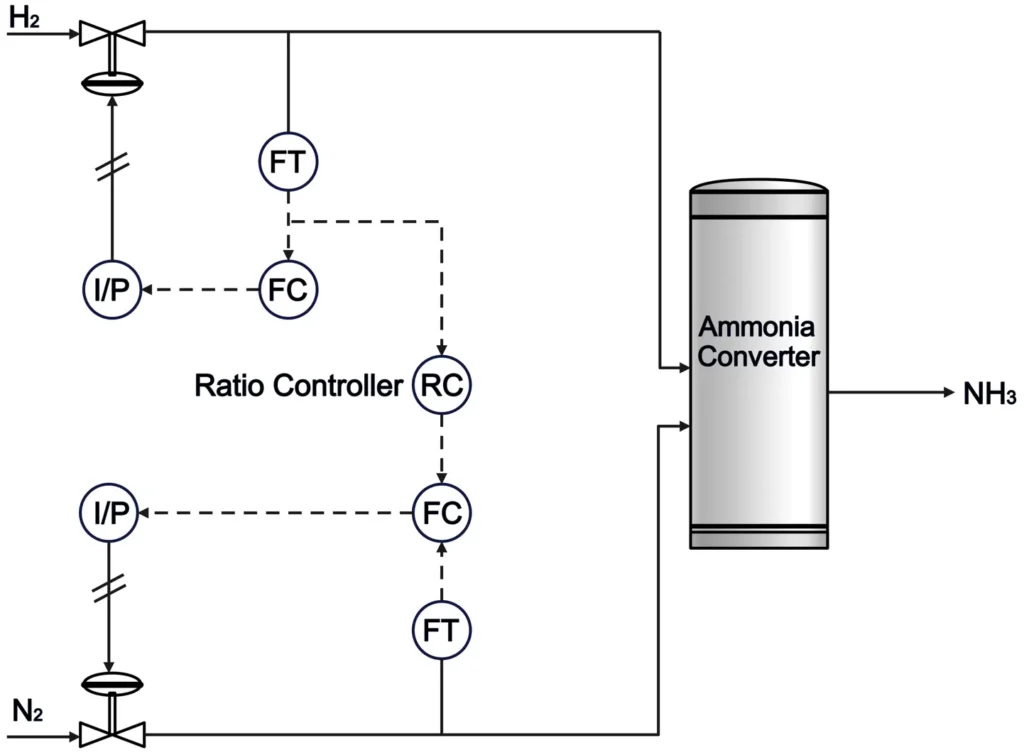
Benefits of Ratio Control
- Consistency: Maintains precise proportions, critical for processes like chemical blending or combustion.
- Efficiency: Optimizes resource use, reducing waste in fuel combustion or reactant feeds.
- Simplicity: Straightforward to implement, especially with digital systems, making it widely applicable.
Automatic Ratio Adjustment
For advanced applications, ratio control can be dynamic. In a combustion system, an oxygen sensor in the exhaust stack might adjust the air to fuel ratio to maintain 2% excess oxygen, optimizing efficiency and minimizing emissions.
Comparing Cascade Control and Ratio Control
While both strategies enhance process control, they serve distinct purposes:
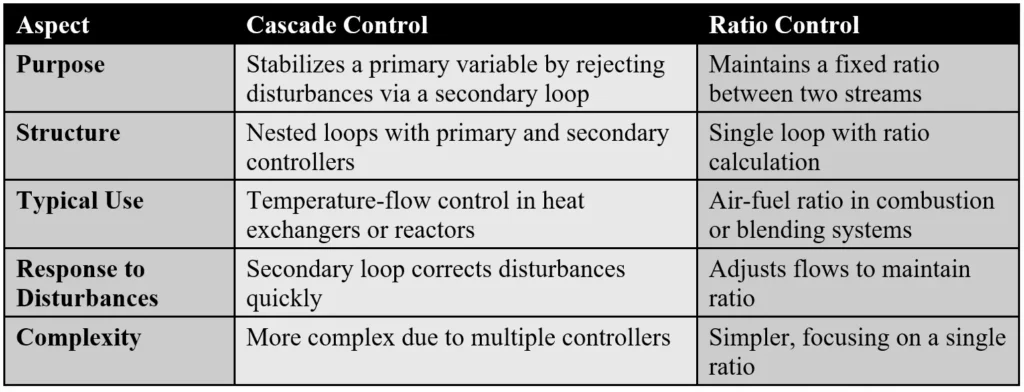
Real-World Applications
Cascade Control in Furnaces
In a fired heater, cascade control maintains a stable outlet temperature despite fuel gas pressure fluctuations. The primary controller monitors the hot oil temperature and sets a setpoint for the secondary flow controller, which adjusts the fuel gas valve. This setup corrects pressure changes before they affect the temperature, ensuring consistent performance.
Ratio Control in Blending Systems
In a chemical plant, ratio control ensures a precise mix of reactants entering a reactor. For example, maintaining a consistent ratio of two chemicals ensures optimal reaction conditions and product quality, reducing waste and improving efficiency.
Can cascade and ratio control be combined?
Yes, in complex systems like steam drum level control, cascade and ratio control can work together. A cascade loop manages valve disturbances, while a ratio controller maintains the steam-to-water ratio, ensuring robust performance across multiple disturbances.
Tuning Cascade Control Systems
Tuning cascade control requires a two-step approach:
- Secondary Loop: Tune the secondary controller (e.g., flow controller) first, treating it as an independent system. Methods like Ziegler-Nichols or Internal Model Control (IMC)-based PID can set parameters like proportional gain.
- Primary Loop: With the secondary loop tuned, adjust the primary controller (e.g., temperature controller) using frequency response methods like Bode plots, ensuring stability and responsiveness.
Challenges and Considerations
- Cascade Control: Requires the secondary loop to be significantly faster than the primary. Slow secondary dynamics or significant deadtime can reduce effectiveness.
- Ratio Control: Depends on accurate measurement of the wild stream. Model uncertainties may require feedback control to correct offsets.
- Physical Constraints: Both methods must account for time delays and nonminimum-phase behavior, which can limit controller design.
References:
- Wade, Harold L. Basic and Advanced Regulatory Control: System Design and Application, Third Edition, 2017.
- Stephanopoulos, G. Chemical Process Control: An Introduction to Theory and Practice, Prentice Hall, 1984.
- Seborg, D. E., Edgar, T. F., & Mellichamp, D. A. Process Dynamics and Control, 2nd Edition, Wiley, 2003.
- Bequette, B. W. Process Control: Modeling, Design, and Simulation, Pearson, 2023.
- https://www.controlglobal.com
- https://controlguru.com