A storage tank is a container for holding various liquids, chemicals, petroleum, petrochemical products and compressed gases. Storage tanks operate under no internal pressure, vacuum, or slight pressure. Storage tanks are often cylindrical in shape, are perpendicular to the ground with flat bottoms, and have a fixed or floating roof. They are used in various sizes to store liquids throughout the process industries.
In petroleum oil refineries, storage tanks are utilized for storing crude oil, finished petroleum products, intermediate products, refinery fuel oil, underground sumps, Amines, sour water, demineralized water storage, raw water, plant water, fire water, slop oil, liquefied petroleum gas, caustic and various chemicals storage.
These chemicals should keep in the right storage tank. Design and safety concern has come to great concern as reported case of fires and explosion in storage tank has been increasing over the years and these accident cause injuries and fatalities. Spills and tank fires not only cause environmental pollution but there would also be severe financial consequences and significant impact on the future business due to the industry’s reputation.
Major Types of Storage Tanks in the Oil and Gas Industry
The first four tank types are cylindrical in shape with the axis oriented perpendicular to the foundation. These tanks are almost exclusively above ground. Horizontal tanks (i.e., with the axis parallel to the foundation) can be used above ground and below ground. The following are major types of storage tanks used in the process industry;
- Fixed-roof tanks
- External floating roof tanks
- Internal floating roof tanks
- Horizontal tanks
- LNG Storage Tanks
- Spheres Storage
Pressure tanks often are horizontally oriented and “bullet” or spherically shaped to maintain structural integrity at high pressures. They are located above ground. Variable vapour space tanks can be cylindrical or spherical in shape.
1. Fixed roof tanks
The fixed roof tanks are used to store liquids, consisting of a cone- or dome-shaped roof that is permanently attached to a cylindrical shell of the tank. Fixed roof tanks are typically used to store products that have relatively low volatilities and flash points. Large quantities of petroleum distillates (Crude oil, diesel, fuel oil etc.), petrochemical, and other liquid chemicals are stored at atmospheric pressure.
Most of the fixed-roof tanks are equipped with a Breather Valve (pressure-vacuum valve) to allow for operation at extremely low internal pressure or vacuum. Gauge hatches, sample wells, float gauges, and roof manholes provide accessibility to these tanks and also act as potential sources of volatile emissions.
Breather vents may be also called conservation vents, although hardly any conservation of vapours happens at such low-pressure settings. The term conservation vent is used to describe a pressure setting of 17 kPa (67 in. w.c.) or less. Vents with settings greater than 17 kPa (67 in. w.c.) are commonly called pressure vents.
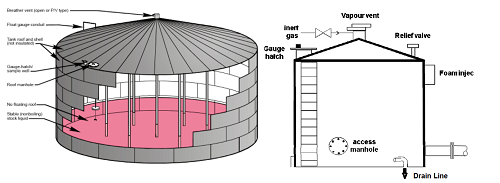
The main disadvantage of a fixed-roof tank is product losses due to the escape of vapour from the free space between the oil level and the roof through the breathers installed at the top. These losses are either breathing losses, caused by the difference in day and night temperature, or filling losses when flowing oil expels an equal volume of vapour through the vents.
2. Floating roof tanks
The roof of a floating roof tank moves on the surface of stored liquid, floating up or down with the level of stored liquid. There is an annular space with a seal gland between the floating roof and the tank wall, to separate atmospheric air. Compared to fixed roof tanks;
- Floating roof tanks can reduce evaporation loss to ~ 90%, thus not only saving product loss but also saving the environment, workers, and the surrounding community by eliminating harmful gases.
- Under extreme heat or earthquakes, the floating roof protects from internal waves and avoiding the tank from being damaged.
A floating roof tank is the most economical and efficient solution for reducing emissions and product loss. As the roof tank rises and falls with the liquid level, vapour losses, fire, and tank collapse hazards are reduced. But floating roof tanks require more maintenance cost as compared to fixed roof tanks.
Products having a greater vapour pressure, like gasoline and other fuels, are stored in this kind of tank. Floating roof tanks can be divided into internal floating roof tanks and external floating roof tanks.
2.1 External Floating Roof (EFR) Tank
An external floating roof tank consists of an open-topped cylindrical steel shell that is equipped with a floating roof on the surface of the stored liquid. The floating roof is comprised of a deck, fittings, and a rim seal system. Floating roof decks are constructed of welded steel plates and are of three general types: pan, pontoon, and double deck type. Although numerous pan-type roof decks are currently in use, the present trend is toward pontoon and double-deck type floating roofs.
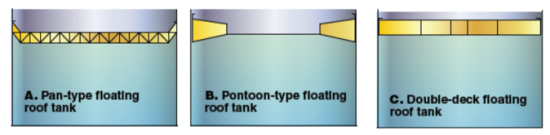

External floating roof tanks are supplied with a rim seal system that runs around the circumference of the roof and touches the tank wall. As the roof is lifted and lowered, the rim seal system slides against the tank wall. The external floating roof design is such that evaporative losses from the stored liquid are limited to losses from the rim seal system and deck fittings (standing storage loss) and any exposed liquid on the tank walls (withdrawal loss).
Due to an open roof, snow and rainwater can accumulate on the roof, therefore requiring a proper draining system. Further, roofs are exposed to sunlight and weather which can accelerate corrosion. The wind and other external factors may cause the roof to swing and even harm an exterior floating roof tank.
2.2 Internal Floating Roof Tank/Closed floating roof tank
An internal floating roof has both a permanent fixed roof and a floating roof within the tank that rests on the liquid inside. There are two basic types of internal floating roof tanks; tanks in which the fixed roof is supported by vertical columns within the tank; and tanks with a self-supporting fixed roof and no internal support columns.
The fixed roof is not necessarily free of openings but does span the entire open-plan area of the vessel. Fixed roof tanks that have been retrofitted to employ an internal floating roof are typical of the first type, while external floating roof tanks that have been converted to an internal floating roof tank typically have a self-supporting roof.
Internal floating roofs also incorporate the rim seals that slide against the tank wall as the roof moves up and down. Circulation vents and an open vent at the top of the fixed roof are generally provided to minimize the accumulation of hydrocarbon vapours in concentrations approaching the flammable range. Flame arresters are an option that can be used to protect the vessel from fire or explosion.
Its fixed roof has natural water draining as compared to an external floating roof tank. Internal floating roof tank eliminates natural ventilation of the tank vapour space. Instead, the closed roof internal floating tank is equipped with a pressure-vacuum vent and may even include a gas blanketing system such as that used with fixed roof tanks.
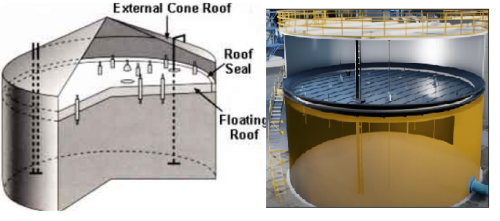
Internal floating roof tanks have the disadvantage of difficult inspection and maintenance as compared to external floating roof tanks. Internal floating roof tanks have fewer losses as compared to external floating roof tanks even though the EFR tanks have secondary seals installed.
2.3 Difference Between External Floating Roof (IFR) and Internal Floating Roof Tanks
The primary difference between an external floating roof (EFR) and an internal floating roof (IFR)Tank is that EFR does not require a fixed roof. Therefore, external floating roof tanks are better for maintenance and inspection as compared to internal floating roof tanks with fixed roofs. Further, evaporation losses are less in internal floating roofs compared to external floating roof tanks.
3. Horizontal Tank
Horizontal-type tanks are present in both above-ground and underground locations. Horizontal tanks are made so that the length of the tank is not more than six times the diameter to ensure the structural integrity of the tank. Most typically, horizontal tanks are fitted with pressure-vacuum vents, gauge hatches, and sampling wells. Underground tanks may be cathodically protected to avoid corrosion of the tank casing.
Cathodic protection is performed using sacrificial anodes linked to an impressed current system or by employing galvanic anodes in the tank. But, most refined petroleum products include corrosion inhibitors that render internal cathodic protection ineffective.
The potential emission sources for above-ground horizontal tanks are the same as those for fixed-roof tanks. Emissions from underground storage tanks are mainly associated with changes in the liquid level in the tank. Losses due to changes in temperature or barometric pressure are minimal for underground tanks because the surrounding earth limits the diurnal temperature change and changes in the barometric pressure would result in only small losses.
4. Liquified Natural Gas Storage Tank
The LNG storage tank is a special type of storage tank, utilized for the storing of liquefied natural gas. Storage tanks may be placed on, above, or in LNG ships. LNG storage tanks have the property to store LNG at an extremely low temperature of -162 °C.
LNG storage tank systems keep the gas in its liquid state for storage or transportation. These tank systems are complex and highly engineered. LNG storage systems use auto-refrigeration to keep the pressure and the temperature in the tank constant. There are three main storage containment types for LNG storage systems: single, double, or full containment.
A single containment system contains an inner and outer container. The inner container is designed to hold liquid and is liquid-tight. The outer container is designed for product vapour pressure. It retains and protects the insulation, but does not contain liquid if the inner container leaks.
A double containment system consists of a liquid and vapour-tight primary tank system. This system is built inside a secondary container that is liquid-tight. This secondary liquid container is liquid-tight but not vapour-tight.
A full containment system consists of a liquid-tight primary container and a liquid and vapour-tight secondary container. Both can independently contain the product. The secondary container controls vapour release in case of a primary product leak. Another design feature of this containment system is thermal corner protection (TCP). TCP protects the base-to-wall joint on the outer tank. In the case of a primary container leak, TCP provides liquid tightness and thermally isolates the joint from the cold liquid.
5. Spherical tanks
Round storage tanks or spheres are typically used to store high-pressure fluids like propane, butane, LPG Ammonia etc. Gases are stored under pressure at a temperature lower than their liquefaction temperature. The curved shape makes spherical tanks very strong.
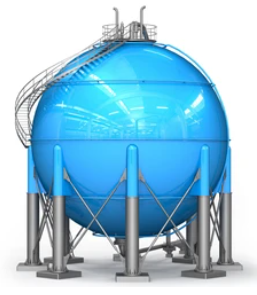
The main advantage of the spherical construction is that the stress concentration will be minimal while storing pressurized gases as the stress resistance will be uniform over the total surface. Another advantage is the reduced exterior surface for a given storage volume as compared to all other possible shapes.
Top References
- The Above Ground Storage Tank Handbook by Brian D.Grado and Gregory A. Thorp
- www.wikipedia.com
- www.wermac.org
- www.klmtechgroup.com
For further information, discussion and queries please comment in the box below or contact us at admin@ or follow us on Facebook & LinkedIn.