Solenoid valves are essential in process industries. These electrically controlled devices manage the flow of fluids and gases with precision, ensuring safety and efficiency in complex systems. From small scale applications to high pressure systems, understanding their working principles and types is important. By selecting the right valve based on media, pressure, and safety requirements, you can optimize performance and mitigate risks in chemical manufacturing, petroleum refining, and oil and gas operations.
What Is a Solenoid Valve?
A solenoid valve is an electromechanical device that controls the flow of liquids or gases using an electric current. It consists of a solenoid (an electromagnet) and a valve body. When energized, the solenoid generates a magnetic field that moves a plunger, opening or closing the valve to regulate flow. These valves are vital in applications requiring precise control, such as emergency shutdown systems in refineries or fluid management in chemical plants.
Why are solenoid valves so important?
They’re fast, reliable, and energy-efficient, making them ideal for automation and safety-critical processes. In industries where a single mistake can lead to catastrophic incidents, solenoid valves provide the precision needed to maintain control.
How Solenoid Valves Work
The working principle of a solenoid valve is straightforward yet interesting. Below is the process:
- De-Energized State: When no electric current flows through the solenoid coil, the valve remains in its default position (either open or closed, depending on its design). A spring or fluid pressure typically holds the plunger in place.
- Energized State: When an electric current is applied, the solenoid coil generates a magnetic field. This field pulls or pushes the plunger, which either opens or closes the valve’s flow path.
- Flow Control: The movement of the plunger allows or blocks the flow of the medium (liquid or gas) through the valve. The response is nearly instantaneous, making solenoid valves ideal for rapid shutoff or flow regulation.
- Return to Default: Once the current is switched off, the spring or fluid pressure returns the plunger to its original position, resetting the valve.
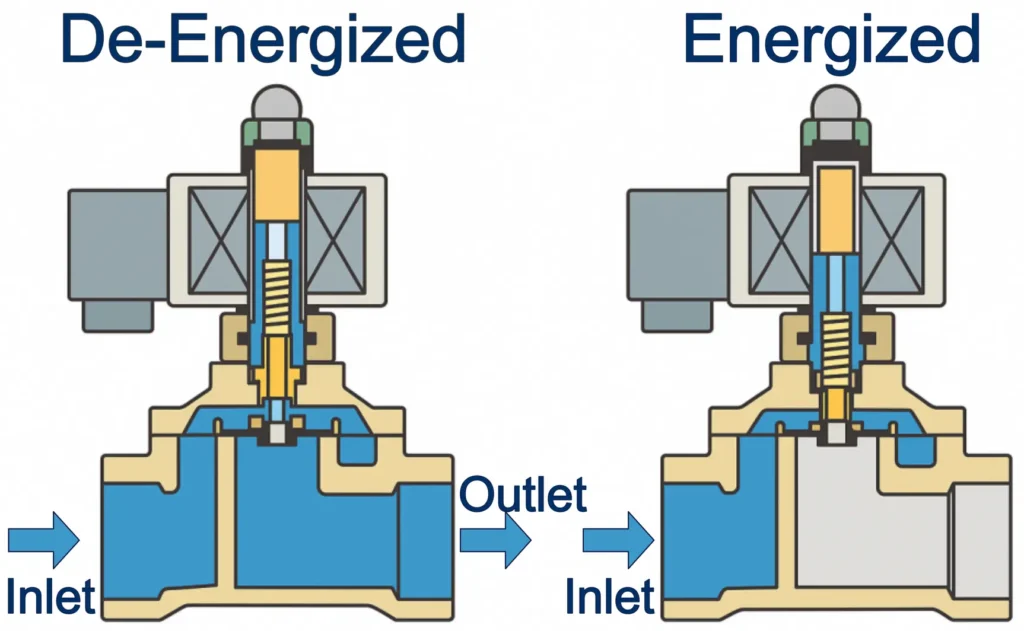
The quick response time and reliability make solenoid valves essential in process safety systems, such as those used in emergency shutdowns or pressure relief in petroleum refineries.
Are solenoid valves AC or DC?
Solenoid valves can operate on both AC (alternating current) and DC (direct current), depending on the system they are used in. The choice depends on the power supply available. DC solenoids are common in battery powered or remote systems, like oil field pipelines, because they’re energy efficient. AC solenoids are often used in industrial settings, such as chemical plants, where high voltage power is standard.
Types of Solenoid Valves
Solenoid valves come in various types, each designed for specific applications. Below, we explore the main types based on their operation, configuration, and functionality.
1. Based on Operation
Direct-Acting Solenoid Valves
Direct-acting Solenoid Valves use the solenoid’s magnetic force to directly move the plunger, opening or closing the valve. These are simple, reliable, and suitable for low-pressure applications. They are commonly used in small scale systems, such as laboratory equipment or water dispensers.
- Advantages: Simple design, fast response, works well at low pressures.
- Applications: Water treatment, small-scale chemical dosing.
Pilot-Operated Solenoid Valves
Pilot-operated Solenoid Valves use system pressure to assist in opening or closing the valve. The solenoid controls a small pilot orifice, which triggers the main valve. These are ideal for high pressure or large-flow systems, such as those in oil and gas pipelines.
- Advantages: Energy efficient, suitable for high pressure systems.
- Applications: Petroleum refinery pipelines, high pressure gas systems.
Manual Reset Solenoid Valves
These valves require manual intervention to reset after actuation, enhancing safety in critical applications. They’re often used in systems where automatic reopening could be hazardous, such as gas supply lines.
- Advantages: Enhanced safety, prevents unintended operation.
- Applications: Gas shutoff in chemical plants.
2. Based on Configuration
2-Way Solenoid Valves
These have one inlet and one outlet, used to start or stop flow. They are the most common type, found in applications like irrigation systems or fuel lines.
- Example: Shutting off fuel flow in a refinery process.
3-Way Solenoid Valves
With three ports, these valves direct flow between two outlets or mix fluids from two inlets. They’re used in systems requiring diversion or mixing, such as in HVAC systems.
- Example: Diverting coolant in a chemical reactor.
4-Way Solenoid Valves
These have four ports and are used in complex systems to control multiple flow paths, often in pneumatic or hydraulic systems.
- Example: Controlling actuators in oil and gas drilling equipment.
3. Based on De-Energized State
Normally Closed (NC) Solenoid Valves
In the de-energized state, the valve is closed, preventing flow. When energized, it opens. These are energy efficient for systems that remain closed most of the time, such as gas safety shutoff valves.
- Example: Emergency gas shutoff in a refinery.
Normally Open (NO) Solenoid Valves
These are open when de-energized and close when energized. They are used in systems where flow is typically required, such as cooling water systems.
- Example: Cooling water flow in a chemical plant.
Bi-Stable (Latching) Solenoid Valves
Bi-stable valves use a momentary pulse to switch states and remain in that position without continuous power. They are energy efficient and ideal for remote applications.
- Example: Remote pipeline control in oil fields.
4. Based on Material and Application
Solenoid valves are made from materials suited to specific media and environments. Common materials include:
- Brass: Cost effective, suitable for water and neutral fluids.
- Stainless Steel: Corrosion resistant, ideal for aggressive chemicals in chemical plants.
- PVC: Lightweight, used for low pressure, corrosive environments.
- Aluminum: Lightweight and thermally conductive, used in petroleum applications.
- Cast Iron: Durable, used in heavy duty industrial settings.
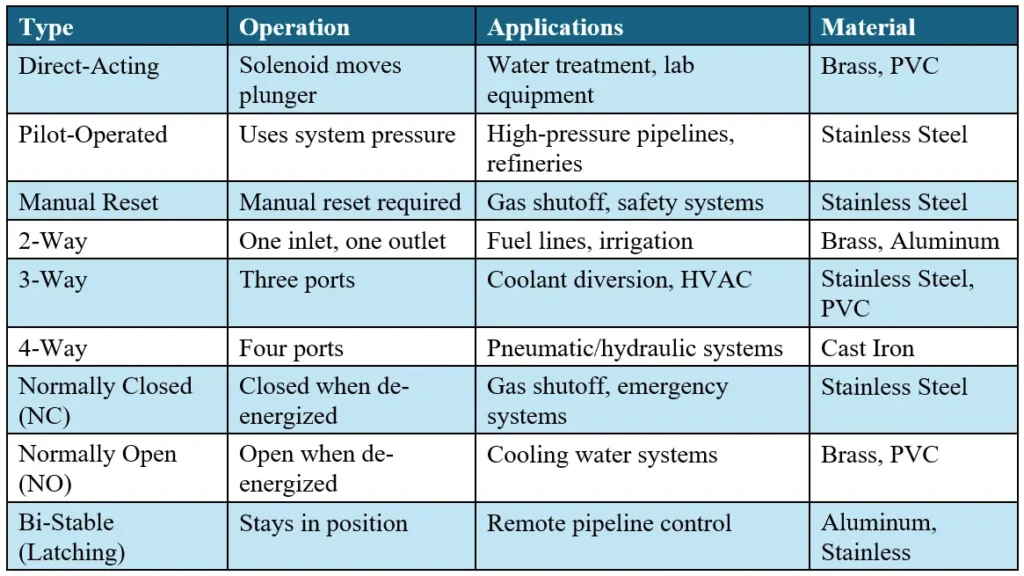
Applications in Process Industries
Solenoid valves are critical in process industries for their reliability and precision. Here are some key applications:
- Chemical Manufacturing: Controlling chemical dosing in reactors, ensuring precise flow to prevent hazardous reactions.
- Petroleum Refineries: Managing fuel and gas flow, including emergency shutoff to prevent leaks or explosions.
- Oil and Gas: Regulating flow in pipelines and drilling equipment, often in harsh environments.
- Process Safety: Used in emergency shutdown systems (ESD) and safety instrumented systems (SIS) to mitigate risks like overpressure or leaks.
For example, in a refinery, a normally closed solenoid valve might be part of an emergency shutdown system, instantly stopping gas flow if a pressure abnormality is detected, aligning with OSHA compliance and HAZOP analysis requirements.
Selection Criteria for Solenoid Valves
Choosing the right solenoid valve involves several factors:
- Media Compatibility: Ensure the valve’s housing and seal materials (e.g., PTFE for aggressive chemicals) are compatible with the fluid or gas.
- Pressure and Flow Requirements: Direct-acting valves suit low pressure systems, while pilot-operated valves handle high pressure applications.
- De-Energized State: Select normally closed, normally open, or bi-stable based on safety and energy needs.
- Voltage: Match the solenoid’s voltage to the power supply (e.g., 24V DC or 120V AC).
- Certifications: For hazardous areas, choose ATEX-certified valves; for drinking water, ensure compliance with relevant standards.
What is the common problem of solenoid valves?
Solenoid valves can face issues like clogging, coil failure, or leakage. Clogging happens when debris blocks the valve, especially in dirty fluids, affecting flow control. Coil failure occurs if the solenoid overheats or gets damaged, stopping the valve from opening or closing. Leakage might result from worn seals, particularly with aggressive chemicals in chemical plants. Choosing the right material, like PTFE seals for corrosive media, and regular maintenance can help prevent these problems. Always ensure the valve matches the system’s pressure and media requirements.
References
- Baumann, H. D. (2008). Control Valve Primer: A User’s Guide. ISA.
- Lyons, J. L., & Askland, C. L. (1996). Lyons’ Valve Designer’s Handbook. Van Nostrand Reinhold.
- Nesbitt, B. (2011). Handbook of Valves and Actuators. Butterworth-Heinemann.
- Skousen, P. L. (2011). Valve Handbook. McGraw-Hill Education.
- Zappe, R. W. (1998). Valve Selection Handbook. Gulf Professional Publishing.
- https://www.burkert.com
- https://www.sciencedirect.com