In petroleum refineries, hydroprocessing is a catalytic process in the presence of Hydrogen to stabilize petroleum products, remove objectionable elements from feedstocks, and crack heavy hydrocarbons into useful lighter products. In Hdyrocprossing the hydrogen-to-carbon ratio of the feed is increased in the presence of a catalyst and hydrogen-rich conditions. In petroleum refineries, the term hydroprocessing is used for both Hydrotreating and Hydrocracking process units.
Hydroprocessing units are the most common process units in modern petroleum refineries. The world’s hydrotreating capacity is more than half as large as the world’s crude distillation capacity. A typical modern petroleum refinery uses at least three hydrotreaters – one for naphtha, one or two for light gas oils, and one or two for heavy gas oil or vacuum gas oil.
In 2022, the global oil refining capacity has almost reached 102 million barrels per day. The market is expected to witness a growth of more than 13% over 2023-2027. The global refinery hydrotreater unit capacity is nearly 63 mmbd in 2023. It is expected that hydroprocessing will grow at an annual growth rare of ~3 % during 2023-2026.
The hydroprocessing process, due to its flexibility, can be employed to upgrade a variety of petroleum streams, ranging from naphtha to vacuum residues, or even full-range crude oils. The role of hydroprocessing in the petroleum refinery is defined as follows;
- Increases the fraction of heavy, sour crudes that must be processed.
- Controls the product quality parameters as per stringent environmental regulations.
- Decreases the heavy fuel oils consumption and increases the requirement for lighter products.
- Pretreatment of feedstocks of downstream conversion processes such as catalytic reforming, catalytic cracking, and hydrocracking.
- To treat the final petroleum products as a finishing step for Kerosene, diesel, or naphtha and achieve the required product quality ecological specifications i.e. to produce ultra-low sulfur products.
- To increase the hydrogen content of the feedstock.
Fixed-bed reactors are the most frequently used in the petroleum industry among all the available hydrotreating reactor technologies. In such systems, gas and liquid flow co-currently down through a catalyst bed in a trickle-flow regime.
Other types of reactors such as moving-bed reactors (MBRs), slurry bed reactors, and ebullated-bed reactors (EBRs) are also available specifically for upgrading the heaviest fractions. Their main feature is their capacity for replacing spent catalysts without interrupting the operation. The selection between each type of technology is dictated by catalyst deactivation, which depends on the nature of the feedstock.
Hydroprocessing is carried out under a wide range of operating conditions. The severity of the process is adjusted depending on the properties of the feed and the required product composition. The main process variables are pressure, temperature, hydrogen-to-oil (H2/oil) ratio, and space velocity. Each variable affects the process in different ways; therefore, the set of operating conditions must be carefully adjusted to achieve an efficient operation.
The Hydrotreating reactions that take place during the HDT process are hydrodesulfurization (HDS), hydrodenitrogenation (HDN), hydro-dearomatization (HDA), hydrodeoxygenation (HDO), and hydrodemetallization (HDM. Another type of reaction in which high molecular weight compounds are broken down into lighter molecules is the Hydrocracking reaction. In the case of hydrocracking of asphaltenes, the process is often referred to as hydro-deasphaltenization (HDAs).
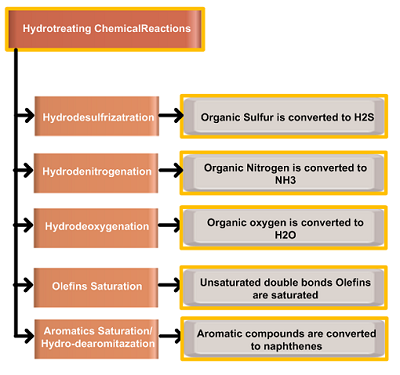
The most common catalyst metals used in hydroprocessing are Mo (Molybdenum) and Tungsten promoted by Ni (Nickel) and Co (Cobalt) because of their high activity, selectivity, and stability. Hydrocracking catalysts have a cracking function and a hydrogenation–dehydrogenation function. The cracking function is provided by acidic support, whereas the hydrogenation–dehydrogenation function is provided by active metals. The acidic support can be (a) amorphous oxide (e.g. silica–alumina), (b) a crystalline zeolite (mostly modified Y zeolite) plus binder (e.g. alumina), or (c) a mixture of crystalline zeolite and amorphous oxides.
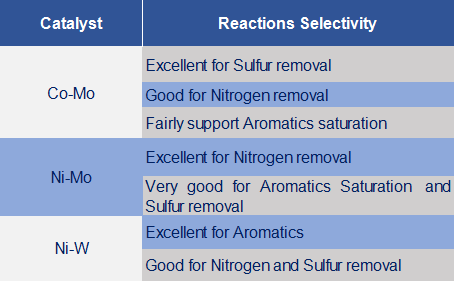
Hydrotreating
Hydrotreating involves the following processes;
- Stabilization or saturation involves converting unsaturated hydrocarbons like olefins and unstable diolefins to paraffins.
- Objectionable elements removed by hydroprocessing include sulfur, nitrogen, oxygen, halides, and trace metals. When the process is explicitly employed for sulfur removal it is usually called hydrodesulfurization (HDS).
- The hydrotreating process is applied to Naphtha, Kerosene, and Diesel range petroleum streams.
- In the Hydrotreating process, fixed bed reactors are utilized.
Hydrotreating of petroleum residua feedstocks involves three important reactions: hydrodesulfurization (HDS), hydrodenitrogenation (HDN), and hydrodemetallization (HDM) for the removal of organically-bound sulfur, nitrogen, and metals respectively. Sulfided Mo, CoMo, and NiMo catalysts are applied at 315~400°C and at pressures 25~90 Kg./cm2.
Hydrocracking
Hydrocracking involves, the cracking of high molecular weight hydrocarbons into lighter low molecular weight products at high temperatures and pressures in the presence of catalysts and hydrogen. At the same time that hydrocracking takes place, sulfur, nitrogen, and oxygen are almost completely removed, and olefins are saturated so that products are a mixture of essentially pure paraffins, naphthenes, and aromatics.
Hydrocracking is one of the most versatile of all petroleum refining processes. Any fraction from naphtha to distillates can be processed to produce almost any desired product with a molecular weight lower than that of the charge stock. Hydrocracking can deal with a variety of feeds from Naphtha to to heavy petroleum streams like reduced crude, vacuum gas oils, vacuum residue, heavy cycle oils, etc.
This feed flexibility gives the hydrocracking process a particularly important role as refineries attempt to meet the challenges of today’s economic climate. The combined influences of low-quality feed sources, capital spending limitations, hydrogen limitations, environmental regulatory pressures, and intense competition have created a complex optimization problem for refiners. The hydrocracking process is uniquely suited, with proper optimization, to assist in solving these problems.
Top References
- Catalytic Hydroprocessing of Petroleum and distillates by Oballa, Michael C
- Hydrotreating of oil fractions by Jorge Ancheyta, Anton Alvarez-Majmutov, and Carolina Leyva
- Hydrotreating and Hydrocracking Fundamentals, Paul R. Robinson and Geoffrey E. Dolbear
- Handbook of Petroleum Refining Processes by Robert A. Meyers
- www.statista.com
- www.globaldata.com