Sour water treatment in a petroleum refinery is a vital process that ensures the safe handling and disposal of water produced during the refining process. The water, known as sour water, contains impurities such as hydrogen sulfide (H2S) and ammonia (NH3) which are harmful to human health and the environment. The treatment process involves a series of chemical reactions and treatments to neutralize and remove these impurities, making the water safe for further use or disposal. Additionally, the process also allows for the recovery of valuable chemicals such as sulfur. With the right techniques and chemicals, the sour water can be treated to a high standard, ensuring the safe and efficient operation of a crude oil refinery.
Feed to the sour water stripper may include effluent water from the crude unit overhead condensers, water phase from the desalters, condensed water from the vacuum unit’s hot well, and all the water condensate. Sour water in refining operations originates from using steam as a stripping medium in distillation columns or from reducing the hydrocarbon partial pressure in thermal or catalytic cracking units, crude unit overhead condensers, water phase from desalters, and condensed water from vacuum unit’s hot well.
Also, in hydrotreating and hydrocracking units, wash water is injected to absorb corrosive compounds ( Salts of H2S and Ammonia) or salts that might cause plugging. This wash water comes in contact with the reactor’s effluent hydrocarbons containing H2S, Ammonia, and ammonium salts, as a result, sour water is formed. The NH3 present in sour water comes from the nitrogen in the crude oil or from ammonia injected into the crude fractionator to avoid corrosion. In addition to H2S and NH3, sour water may contain phenols, cyanide, CO2, and even salts and acids.
Sour Water Treatment Process Description
The sour water collected from various refinery processing units passes through a flash or separation drum to flash off dissolved gases which are normally flared. After the removal of gases, the sour water is stored in a tank to remove hydrocarbon oils and solids by giving settling time in a storage tank. The separated oil is skimmed off and sent to the slop oil recovery tank.
The sour water becomes stripper feed and is heated by exchange with stripper bottoms water. The heated water is introduced in a stripper tower with ~ 40 sieve trays. Ammonia and H2S are stripped from this water in this sour water stripping column. The column has a thermosyphon reboiler with low-pressure steam to provide the required heat for stripping the gases from the sour water.
The stripped H2S and NH3 vapors flow to the sulfur recovery plant at a temperature of ~ 90°C.
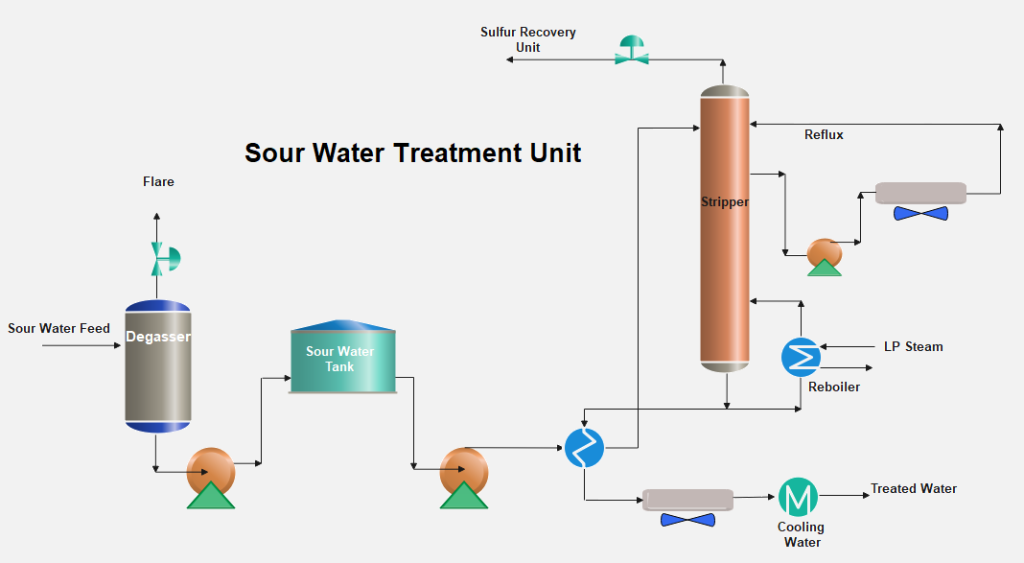
A pump around to provide the reflux to the column is removed from the column and returned to the column top. The stripped water is cooled by exchange with the feed and is further cooled by air or water. The stripped water can be used in crude oil desalters and extra water is sent to a final effluent-treating unit for biological treatment.
Process Chemistry Sour Water Treatment
The chemistry assumes that NH3 and H2S are present in the aqueous solution as ammonium hydrosulfide (NH4HS), which is the salt of a weak acid (H2S) and a weak base (NH4OH). The salt hydrolyzes in water to form free NH3 and H2S, which then exert partial pressure and can be stripped. The aqueous phase equilibrium is;
NH4 + H2S ←→ H2S + NH3
Increasing the temperature shifts the equilibrium to the right, and makes it easier to strip out H2S and NH3. H2S is much less soluble and is therefore more easily stripped. When acidic components such as CO2 or CN- are present, they replace HS- in the above equations, and the NH3 becomes bound in solution as a salt such as (NH4)2CO3. The free NH3 formed by hydrolysis is small. Thus, the H2S removal is higher than predicted, while the NH3 removal is lower.
Sour Water Stripping, Process Variables
A typical stripped water specification limits H2S to 1 to 10 wt ppm and NH3 to 30 to 200 wt ppm. Normally, it is the NH3 specification that governs the stripper design, since it is much more difficult to strip than H2S. Some stripper designs use caustic to free the bound ammonia, particularly when the feed has appreciable CO2 or cyanides. The presence of phenols and cyanides in the sour water also can have an impact on the number of strippers. Nonphenolic sour water strippers process sour water with H2S and NH3 only.
It is desired to recycle as much of the stripped water as possible. Stripped water can be reused in the crude desalter, makeup water for coker units, wash water for the hydrotreating units, and sometimes as cooling towers make up water.
On the other hand, Phenolic sour water contains phenols and other pollutants from catalytic crackers and cokers, and stripped water from phenolic sour water strippers is corrosive and may poison catalysts if used as injection wash water.
In conventional single-stage strippers, an acid gas containing H2S and NH3 is produced. The Sulfur Recovery Unit must be designed for NH3 burning. An alternative method is to use a two-stage stripper that produces separate NH3 and H2S product streams.
Top References
- Handbook of Petroleum Refining Processes by Robert A. Mayers
- Refining Processes Handbook by Surinder Parkash
For further information, discussion, and queries please comment in the box below or contact us at admin@ or follow us on Facebook & LinkedIn.