The Minimum Pressurization Temperature (MPT) or Minimum Safe Pressurization Temperature (MSPT) is the lowest temperature at which the hydroprocessing reactor can be pressurized again after a shutdown without the risk of brittle fracture of low alloy steel. At temperature above the MPT low alloy steel ensures sufficient toughness that saves it from brittle fracture. The MPT intends to ensure that the hydroprocessing reactor is not subject to above-threshold primary stresses from pressure and temperatures where the material of construction is susceptible to hydrogen and temperature embrittlement.
The MPT envelopes permissible pressure-temperature combinations for the safe operation of the unit. It is recommended that 25% of the design pressure of equipment is the maximum pressure that can be applied below the MPT i.e., the system pressure must not exceed the 25 % of design pressure until the equipment temperature has exceeded the minimum temperature to prevent the material from brittle fracture. This 25% point is critical to prevent brittle fracture.
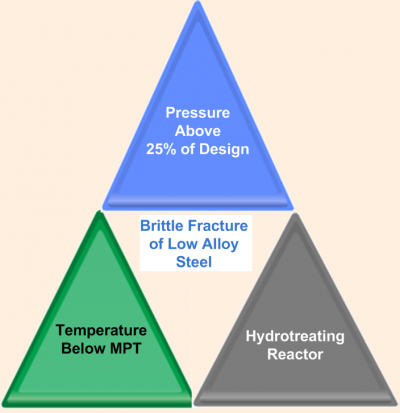
MPTs generally range from 170 °C for the earliest, most highly temperature embrittled steels, down
to 50 °C for newer, temperature-embrittlement-resistant steels as required to also minimize
effects of Hydrogen embrittlement.
The vessel fabricator defines the MPT requirement based on the standards or by sound industry practices to avoid brittle fracture of the base material and welds during vessel operation including startup and shutdown.
It is better to follow the manufacturer’s recommended MPT and avoid the optimization of the temperature for saving the startup time, although this temperature is defined with margins. Further, over the years, actual MPT can also be increased due to reaction conditions prevailing.
Conditions When MPT to be Established
The process engineer should always consider MPT not only when starting up but also when temperatures start to fall in a shutdown or any other case. There may be another vessel in the high-pressure loop similar to the reactor that also has its own MPT value and that must be considered before any pressurization above 25% of design pressure is initiated. Not knowing the MPT can result in a catastrophic failure so consult original records or have a coupon from the reactor tested (if available) to determine an appropriate MPT.
The monitoring point of MPT is the skin temperatures of the hydroprocessing reactor wall and all the temperature indicators must show the temperature above MPT. Further, this critical condition must be covered in standard operating procedures and operating manual. Following conditions may arise during operation of hydrotreating unit;
- During the hydrotreating unit startup, when the reactor has been opened for repair or inspection or when the new equipment has been installed, the unit heating is carried out at defined rates. It might take a long duration to achieve the desired reactor wall skin temperatures of the reactor. Once tall reactor skin temperature indicators have been gone above the MPT, it is safe to increase pressure in the system pressure up to the normal operating point.
- For a normal shutdown, there might not be serious concerns as the reactor wall bears high skin temperature but for a long shutdown, the system should be depressurized before the threshold temperature value can be achieved.
- Another critical condition that can be faced is the shutdown of the hydrotreating unit, for catalyst replacement. For safe handover, the reactor wall is cooled gradually below 50°C by establishing recycle gas circulation. At this stage, firstly the reactor circuit must be depressurized below 25 % of the design pressure when the reactor temperatures drop below the MPT. Secondly, monitor the system pressure or reactor inlet pressure, and if any sudden pressure is observed then immediately operate an emergency depressurization system.
Relationship of Hydrogen embrittlement with MPT
Hydrogen embrittlement (HE) is a type of stress corrosion cracking, resulting in several forms of damage. Known effects of HE are loss of ductility and fracture strength and macroscopic damage due to hydrogen entrapment at mechanical interfaces. HE is suffered from various high-strength steels.
At high temperature and pressure, molecular hydrogen partially breaks to form atomic hydrogen, (H2 ↔ 2H) which is a reversible, equilibrium-limited reaction. Atomic hydrogen is soluble in steel and will enter the lattice structure of the reactor walls. The inner surface of the steel becomes saturated and atomic hydrogen starts diffusing towards the outer surface. If a discontinuity or defect is present or the reactor is below MPT then atomic hydrogen that is diffusing through the steel can reversibly form molecular hydrogen in the void, which becomes trapped and starts to accumulate. These trapped pockets of hydrogen create fissures (long and narrow lines of breakage made by cracking) that lead to intergranular cracking.
At the re-pressurization phase of the unit, the MPT tries to re-establish the equilibrium profile for atomic hydrogen through the steel to minimize the potential for molecular hydrogen present at the grain boundaries that could result in rapid brittle failure. The heating of the hydrotreating unit is normally achieved by heating up a recycle gas stream through the fired heater before entering the reactor. Once the minimum temperature has been achieved, it is safe to start increasing pressure in the system up to the normal operating point.
Relationship of Temperature Embrittlement With MPT
Temperature embrittlement is the loss of ductility after prolonged exposure to high temperatures that may be exhibited by specific Cr-Mo steels containing high levels of residual elements. Temperature embrittlement takes place after the equipment has operated at elevated temperatures (340~540°C) for long periods of time.
Temperature embrittlement can lead to brittle fracture when vessels are pressurized at temperatures well below design in the 40°C to 150°C temperature range. In the as-fabricated condition, Cr- Mo steel exhibits a low transition temperature typical for steels with good resistance to fast brittle fracture, while after long-term elevated temperature service, the steel displays a high transition temperature typical for steels affected by temper embrittlement.
Top References
- The Effects of Hydrogen for Establishing a Minimum Pressurization Temperature (MPT) for Heavy Wall Steel Reactor Vessels, API TECHNICAL REPORT 934-F, PART 4.
- Protecting your hydroprocessing reactor by ERIC LIN and RICHARD TODD Norton Engineering Consultants
- Effect of temper and hydrogen embrittlement on mechanical properties of 2,25Cre1Mo steel grades e Application to Minimum Pressurizing Temperature (MPT) issues. Part I & Part II.
- Optimization of Minimum Safe Pressurization Temperature(MSPT) for Hydroprocessing Reactor.
- Damage Mechanisms Affecting Fixed Equipment in the Refining Industry, ANSI/API RECOMMENDED PRACTICE 571.
For further information, discussion and queries please comment in the box below or contact us at admin@ or follow us on Facebook & LinkedIn.
3 thoughts on “Minimum Pressurization Temperature in Hydroprocessing Units”
Assalam o Alaikum sir,
Please write on the amine scrubber.
Regards;
Muhammad Asif
A well explained and nicely written article. Thumbs up for great work sir.