In process industries such as oil and gas, chemical manufacturing, and petroleum refining, maintaining optimal temperatures in pipelines and equipment is critical for operational efficiency, safety, and compliance with regulations. Heat tracing systems are essential for preventing freezing, maintaining process temperatures, and ensuring smooth operations in challenging environments. These systems mitigate risks like pipe blockages, equipment failures, and hazardous incidents, aligning with standards and process safety protocols.
What is a Heat Tracing System?
A heat tracing system comprises heating elements, control systems, and insulation designed to maintain or raise the temperature of pipes, vessels, or equipment. These systems counteract heat loss due to ambient conditions, ensuring fluids remain at the desired temperature for processing, transportation, or storage. In process industries, heat tracing prevents issues like freezing, condensation, or viscosity changes that could disrupt operations or lead to safety hazards.
Why Heat Tracing Matters
- Prevents Freezing: Protects pipelines from blockages or bursts caused by frozen fluids in cold climates.
- Maintains Process Efficiency: Ensures fluids like crude oil, chemicals, or molten salts remain at optimal temperatures for flow and processing.
- Enhances Safety: Reduces risks of incidents like spills or explosions due to temperature fluctuations, supporting OSHA compliance and HAZOP recommendations.
- Reduces Downtime: Minimizes production halts caused by temperature related equipment failures.
- Ensures Product Quality: Maintains consistent fluid properties, critical for processes like distillation or chemical reactions.
What is the purpose of heat tracing in piping?
Heat tracing in piping keeps fluids at the right temperature to prevent freezing, ensure smooth flow, or maintain process conditions. It stops pipes from clogging or bursting in cold weather and helps maintain the quality of fluids like oil or chemicals. By avoiding temperature related issues, it boosts safety and reduces downtime, aligning with standards.
Types of Heat Tracing Systems
Heat tracing systems are broadly categorized into electrical heat tracing and steam heat tracing, each suited to specific applications based on process requirements, cost, and infrastructure availability.
1. Electrical Heat Tracing
Electrical heat tracing uses electric cables or tapes to generate heat, offering flexibility and precise control. These systems are widely used in modern facilities due to their adaptability.
- Self-Regulating Cables: Automatically adjust heat output based on ambient temperature, reducing energy waste. Ideal for variable temperature conditions.
- Constant Wattage Cables: Deliver consistent heat output, suitable for long pipelines with stable temperature requirements.
- Mineral-Insulated Cables: Designed for high temperature applications, offering durability in corrosive or extreme environments.
Advantages:
- Precise temperature control via thermostats or control panels.
- Energy efficient, especially self-regulating systems.
- Easy to install and maintain with minimal infrastructure.
Applications: Used in chemical plants, refineries, and water treatment facilities for freeze protection and temperature maintenance.
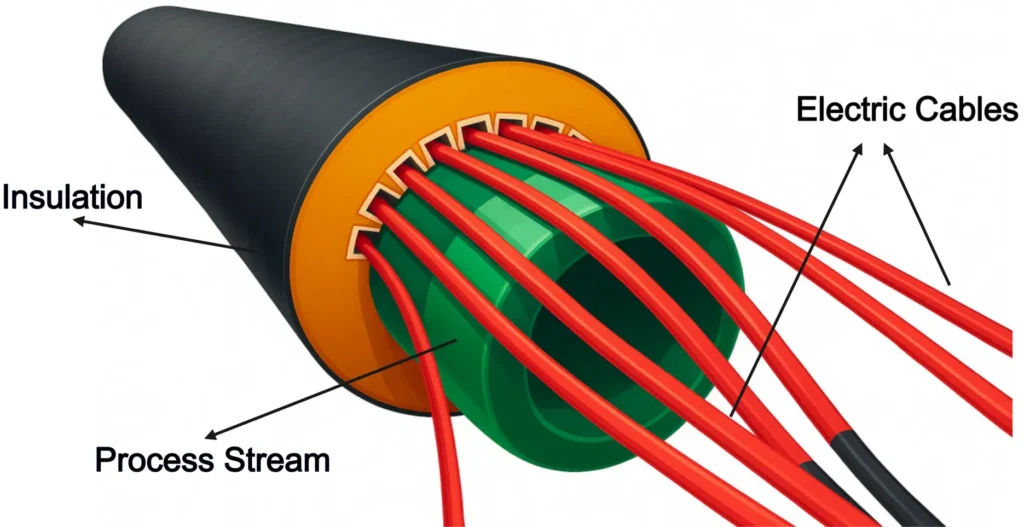
2. Steam Heat Tracing
Steam heat tracing involves circulating steam through tubes or jackets to transfer heat to pipelines or equipment. Steam tracing is prevalent in facilities with existing steam infrastructure.
- External Steam Tracing: Steam tubes run parallel to the process pipe, transferring heat through conduction.
- Jacketed Piping: Steam circulates in a jacket around the pipe, ideal for high-viscosity fluids or high-temperature processes.
- Light and Heavy Tracing: Light tracing uses fewer tubes for moderate heat needs, while heavy tracing employs multiple tubes for high heat demands.
Advantages:
- Cost-effective in facilities with abundant steam supply.
- Reliable for large-scale, high temperature processes.
- Minimal electrical infrastructure required.
Applications: Common in oil refineries and chemical plants for heating heavy oils, bitumen, or molten salts.
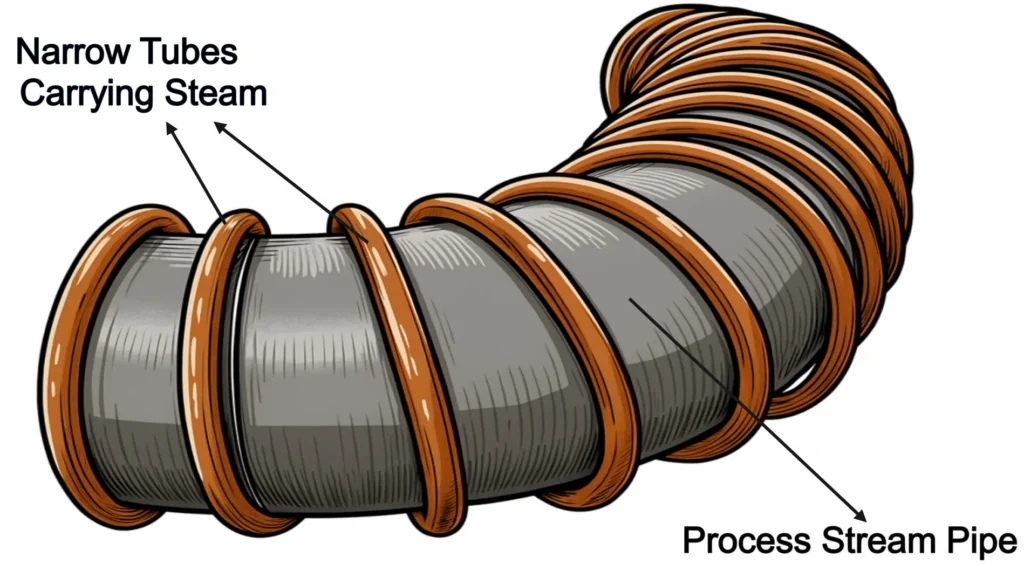
How do you select the right heat tracing system?
Choosing the right heat tracing system involves assessing the fluid type, required temperature, and available infrastructure, like steam or electricity. Calculate heat loss to determine the system’s capacity, and consider environmental factors like cold weather. A HAZOP analysis helps identify risks to ensure safety and compliance.
Electrical Heat Tracing vs. Steam Heat Tracing
The following table compares the two systems to guide selection.
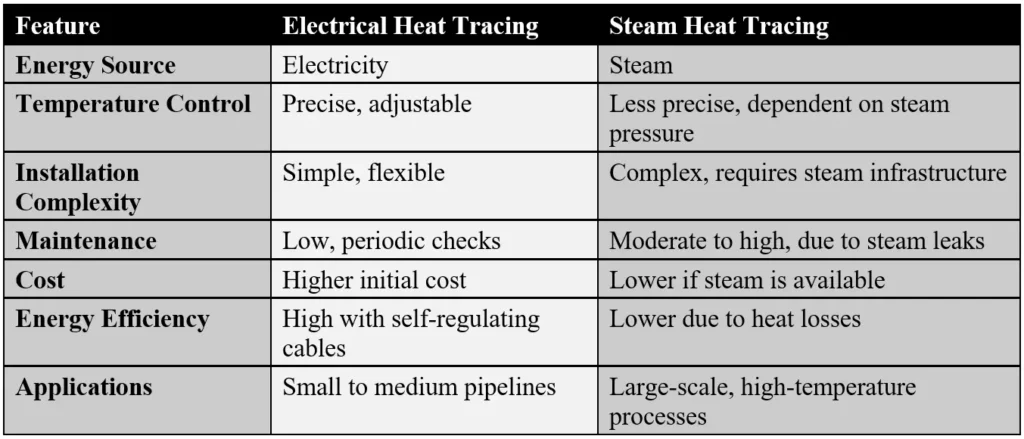
Applications in Process Industries
Heat tracing systems are critical across various process industries. Key applications include:
- Oil and Gas: Prevents wax buildup or hydrate formation in pipelines carrying crude oil or natural gas.
- Chemical Manufacturing: Maintains temperatures for reactive chemicals, preventing crystallization or viscosity issues that could disrupt reactions.
- Petroleum Refineries: Supports processes like distillation by maintaining temperatures in transfer lines.
- Environmental Engineering: Ensures water treatment systems or waste management pipelines remain operational in cold climates.
- Pharmaceuticals: Maintains precise temperatures for sensitive compounds during processing or storage.
- Power Plants: Protects boiler feedwater lines and fuel oil systems from freezing or viscosity changes.
Case Study: Heat Tracing Failure in a Refinery
A 2018 incident at a U.S. refinery where a heavy crude oil pipeline froze due to inadequate steam tracing during a cold weather. The blockage caused a 48-hour production halt, costing millions in losses. Upgrading to a self-regulating electrical heat tracing system with automated controls resolved the issue, reducing energy consumption by 15% and ensuring reliable operation.
Benefits of Heat Tracing Systems
Heat tracing systems offer significant advantages, aligning with process safety and operational goals:
- Improved Safety: Prevents hazardous conditions like pipe bursts, chemical spills, or explosions due to temperature fluctuations.
- Energy Efficiency: Self-regulating electrical systems optimize energy use, reducing operational costs.
- Cost Savings: Minimizes maintenance and downtime expenses by preventing blockages and equipment failures.
- Regulatory Compliance: Supports adherence to OSHA standards and HAZOP recommendations for risk management.
- Versatility: Applicable to diverse fluids, temperatures, and environmental conditions, from arctic climates to high temperature processes.
- Process Reliability: Ensures consistent fluid properties, critical for quality control in chemical reactions or refining processes.
Design Considerations for Heat Tracing Systems
Designing an effective heat tracing system requires careful planning. Key considerations include:
- Heat Loss Calculation: Determine the heat loss rate of the pipeline or equipment based on fluid properties, pipe material, and ambient conditions.
- System Selection: Choose electrical or steam tracing based on temperature requirements, infrastructure, and cost.
- Insulation: Select appropriate insulation materials (e.g., fiberglass or foam) to minimize heat loss.
- Control Systems: Implement thermostats, sensors, or distributed control systems (DCS) for precise temperature regulation.
- Environmental Factors: Account for wind speed, humidity, and temperature extremes in outdoor installations.
- Safety Analysis: Conduct a HAZOP study to identify temperature related risks and ensure compliance with safety protocols.
Challenges and Solutions
Heat tracing systems face challenges that require proactive solutions:
- Challenge: High initial costs for electrical systems.
- Solution: Use steam tracing in facilities with existing steam infrastructure or invest in energy-efficient self-regulating cables.
- Challenge: Steam leaks in tracing systems, leading to inefficiencies.
- Solution: Install steam traps and conduct regular inspections to detect and repair leaks.
- Challenge: Overheating risks in electrical systems, potentially damaging cables or fluids.
- Solution: Use control systems with temperature sensors and alarms to prevent overheating.
- Challenge: Inadequate insulation leading to heat loss.
- Solution: Select high-quality insulation and perform regular maintenance checks.
Advanced Practices for Heat Tracing
To optimize heat tracing systems, consider these advanced practices:
- Automated Monitoring: Use DCS or SCADA systems to monitor temperature and system performance in real-time, reducing manual oversight.
- Energy Optimization: Implement variable frequency drives (VFDs) or smart controllers to minimize energy consumption in electrical systems.
- Redundancy: Install backup tracing circuits to ensure reliability during system failures.
- Thermal Modeling: Use software tools to simulate heat loss and optimize system design, ensuring efficient performance.
- Regular Audits: Conduct periodic safety and performance audits to identify inefficiencies or risks, aligning with process safety protocols.
References
- Perry, R. H., & Green, D. W. (2008). Perry’s Chemical Engineers’ Handbook. McGraw-Hill.
- Coulson, J. M., & Richardson, J. F. (1999). Chemical Engineering: Volume 1. Butterworth-Heinemann.
- Sinnott, R. K. (2005). Chemical Engineering Design. Elsevier.
- Kister, H. Z. (1990). Distillation Design. McGraw-Hill.
- Lees, F. P. (2012). Lees’ Loss Prevention in the Process Industries. Butterworth-Heinemann.
- https://www.sciencedirect.com
- https://www.ignistrace.com