Imagine a chemical plant, where a single overlooked valve or ignored pressure reading could spark a catastrophic explosion. Process safety is the critical discipline that prevents such disasters in high-risk industries like chemical manufacturing, oil and gas, and petrochemicals. It is a commitment to protecting lives, the environment and businesses. By understanding hazards, managing risks and learning from past incidents, engineers and industry professionals can prevent disasters.
What is Process Safety?
Process safety focuses on preventing major incidents, such as fires, explosions, or toxic releases in industries handling hazardous materials or complex processes. Unlike occupational safety, which protects workers from immediate risks like slips or cuts, process safety addresses systemic, high-consequence risks. It blends engineering, management, and regulatory practices to control dangerous substances and processes ensuring operations run safely and reliably.
For instance, occupational safety might involve wearing protective gear to avoid cuts, while process safety ensures a chemical reactor is designed and operated to prevent an explosion. This distinction is vital in fields like chemical manufacturing, petroleum refining, and oil and gas, where the stakes are extraordinarily high.
What is the difference between process safety and occupational safety?
Process safety focuses on preventing major incidents like explosions or chemical leaks in industries handling hazardous materials ensuring systemic risks are controlled. Occupational safety, on the other hand, protects workers from everyday workplace injuries such as slips, falls, or cuts often through measures like wearing protective gear. While process safety addresses high-consequence, low-frequency events, occupational safety deals with frequent, individual risks. Both are crucial for safe operations but target different types of hazards.
Why Process Safety Matters
Neglecting process safety can lead to devastating consequences for lives, the environment and businesses. Here is why it is essential:
- Humanitarian Impact: Process safety safeguards workers and nearby communities from injuries, fatalities, or long-term health issues caused by incidents like chemical leaks.
- Environmental Protection: It prevents spills or emissions that harm ecosystems, as seen in the Deepwater Horizon blowout (2010), which caused massive environmental damage.
- Economic Stability: Incidents result in costly downtime, equipment damage, and legal penalties. A 1970s chlorine tank car leak in Florida led to $200 million in liability claims, dwarfing the company’s assets.
- Reputation and Trust: A strong safety record fosters confidence among communities and stakeholders, while failures like the Bhopal disaster (1984) severely damage a company’s reputation.
Historical incidents drive home these points. The Bhopal tragedy, where 40 metric tons of methyl isocyanate leaked, killed thousands due to inadequate safety systems. The BP Texas City Refinery explosion (2005) claimed 15 lives because of improper startup procedures, and the Imperial Sugar dust explosion (2008) caused 14 deaths due to poor hazard awareness.
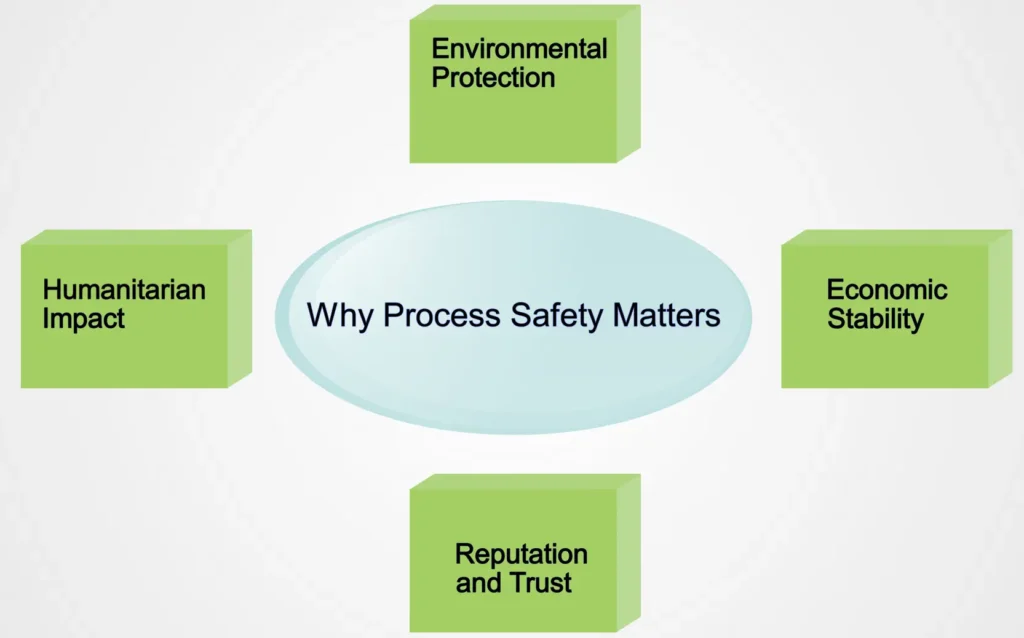
What is process safety in HSE?
In Health, Safety and Environment (HSE), process safety is about preventing major incidents like fires, explosions or toxic releases in industries handling hazardous materials. Process safety manages systemic risks in complex processes. It involves engineering, management and regulations to keep dangerous substances and operations safe. This ensures protection for workers, communities and the environment from catastrophic events.
Key Components of Process Safety Management
Process safety management (PSM) is a structured approach to identifying, evaluating and controlling risks in hazardous processes. The Center for Chemical Process Safety (CCPS) Risk-Based Process Safety (RBPS) framework, introduced in 2007, outlines four pillars:
1. Commit to Process Safety
- Safety Culture: Build an environment where safety is a core value, as weak safety cultures contributed to disasters.
- Compliance with Standards: Follow regulations like OSHA’s PSM and API codes.
- Competency and Training: Equip workers with knowledge to handle hazardous processes.
- Workforce Involvement: Engage operators and maintenance staff in safety reviews.
- Stakeholder Outreach: Communicate risks and safety measures to communities and regulators.
2. Understand Hazards and Risk
- Process Knowledge Management: Maintain accurate data on hazardous materials, like Safety Data Sheets (SDS) or Piping and Instrumentation Diagrams (P&IDs), to avoid failures.
- Hazard Identification and Risk Analysis (HIRA): Use tools like HAZOP to assess and mitigate risks systematically.
3. Manage Risk
- Operating Procedures: Develop clear and written instructions for safe operations.
- Safe Work Practices: Implement protocols like lockout-tagout (LOTO) and hot work permits.
- Asset Integrity: Regularly inspect equipment to prevent failures.
- Contractor Management: Ensure contractors adhere to safety protocols.
- Management of Change (MOC): Review process or staffing changes to avoid risks.
- Emergency Preparedness: Plan for effective incident response.
4. Learn from Experience
- Incident Investigation: Analyze incidents and near-misses to prevent recurrence.
- Metrics and Auditing: Track leading indicators (e.g., training completion) and lagging indicators (e.g., injury rates) to monitor performance.
- Management Review: Regularly assess PSM systems for continuous improvement.
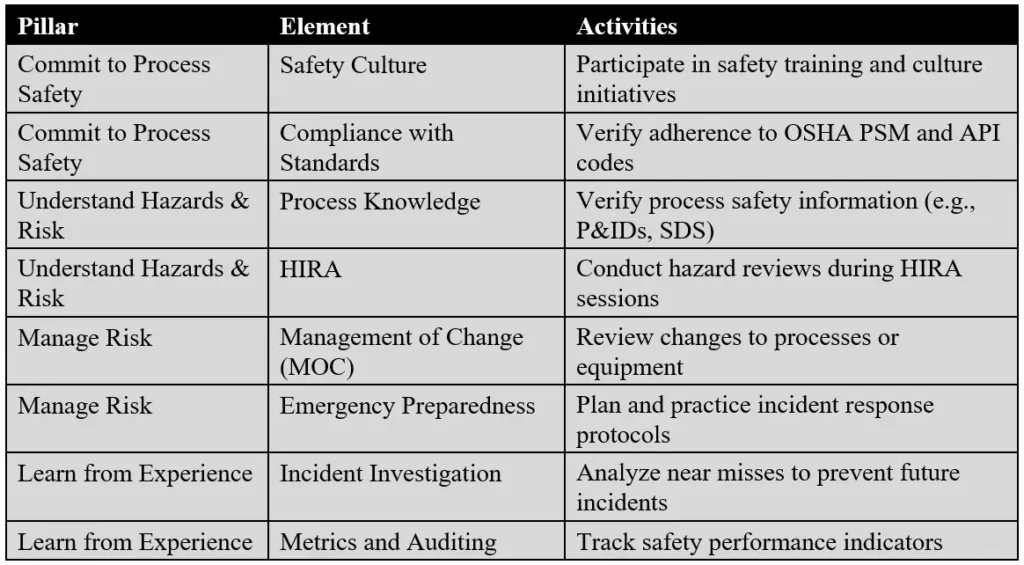
Inherently Safer Design
Inherently Safer Design (ISD) minimizes hazards through strategies like:
- Minimize: Use smaller quantities of hazardous materials.
- Substitute: Replace dangerous substances with safer alternatives, like less hazardous solvents.
- Moderate: Operate under less hazardous conditions, such as lower temperatures or pressures.
- Simplify: Design simpler, error-tolerant systems with fewer valves or clearer layouts.
This approach reduces risks at the design stage, making processes inherently safer.
Lessons from Past Incidents
Learning from history is vital. Key incidents include:
- Bhopal (1984): A methyl isocyanate leak killed thousands due to cost-cutting and poor safety systems.
- Texas City (2005): An explosion from improper startup procedures killed 15 workers.
- Deepwater Horizon (2010): A blowout caused 11 deaths and environmental devastation due to risk assessment failures.
- Piper Alpha (1988): A gas release from maintenance errors led to 167 deaths.
These tragedies highlight the need for hazard identification, risk management and a strong safety culture.
Building a Strong Safety Culture
A safety culture prioritizes safety at every level. To build a safety culture:
- Leadership Commitment: Leaders must model safety behaviors and provide resources.
- Open Communication: Encourage reporting of issues without fear of reprisal.
- Training: Provide regular education on protocols, HAZOP and emergency procedures.
- Empowerment: Equip workers to stop unsafe operations.
- Metrics: Use leading (e.g., safety suggestions) and lagging (e.g., injury rates) indicators to track performance.
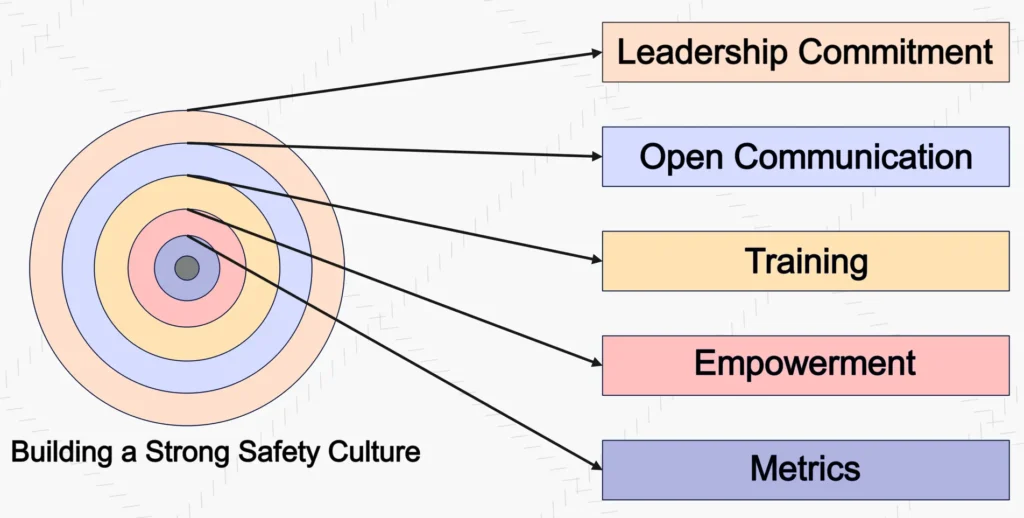
Process Safety for New Professionals
New professionals can play a crucial role in process safety by:
- Conducting hazard reviews during HIRA sessions.
- Verifying compliance with standards like OSHA PSM or API codes.
- Participating in incident investigations to analyze near misses.
- Implementing MOC to review changes to processes or equipment.
The Safety and Chemical Engineering Education Committee offers training modules to integrate process safety into curricula, covering hazard identification, risk analysis and incident investigation.
How to Implement Process Safety in Your Organization
- Foster a Safety Culture: Encourage leadership commitment and open communication.
- Invest in Training: Educate staff on HAZOP, emergency shutdowns and safety protocols.
- Adopt RBPS: Tailor the framework to your facility’s risk level, per CCPS guidelines.
- Learn from Incidents: Use investigations and audits to drive continuous improvement.
- Engage Stakeholders: Involve workers, contractors and communities in safety planning.
References:
- Introduction to Process Safety for Undergraduates and Engineers, American Institute of Chemical Engineers, Center for Chemical Process Safety, New York, NY, 2016.
- Brauer, R. L. Safety and Health for Engineers, Second Edition, John Wiley & Sons, Inc., 2006.
- Process Safety for Engineers: An Introduction, Center for Chemical Process Safety, Wiley, 2022.
- Cheremisinoff, Nicholas P. Practical Guide to Industrial Safety Methods for Process Safety Professionals, CRC Press, Taylor & Francis Group, 2000.
- Crowl, Daniel A., and Louvar, Joseph F. Chemical Process Safety: Fundamentals with Applications, Pearson, 2020.
- https://www.environmentandsociety.org
- https://whsandtrainingcompliance.com.au