Pumps are the primary movers in process industries like chemical manufacturing, oil and gas, and petroleum refining, tirelessly moving fluids through complex systems. But even these can falter without proper care, especially when it comes to two critical concepts: Pump Priming and Cavitation. Priming lays the groundwork for smooth startup by removing air, while preventing cavitation safeguards your pump from destructive vapor bubbles. By mastering NPSH, optimizing suction design, and choosing the right pump, you can ensure reliable, efficient, and safe operations.
What is Pump Priming?
Pump priming is the process of filling a pump and its suction line with liquid to remove out air or gases before starting it. This step ensures the pump can generate the suction needed to move fluid efficiently.
Why Priming Matters?
Centrifugal pumps, widely used in process plants, rely on liquid to create a low-pressure zone at the impeller’s eye, pulling in more fluid. If air is trapped in the pump or suction line, it disrupts this process, dropping efficiency or stopping the pump altogether. Without priming, you risk:
- Poor Performance: Air pockets reduce the pump’s ability to generate pressure, leading to low flow or no flow.
- Mechanical Damage: Running a pump dry can overheat components or wear them out prematurely.
- Downtime: A pump that fails to start halts operations, costing time and money.
Priming is especially critical for pumps with suction lift, where the liquid source is below the pump, as air can easily infiltrate the system.
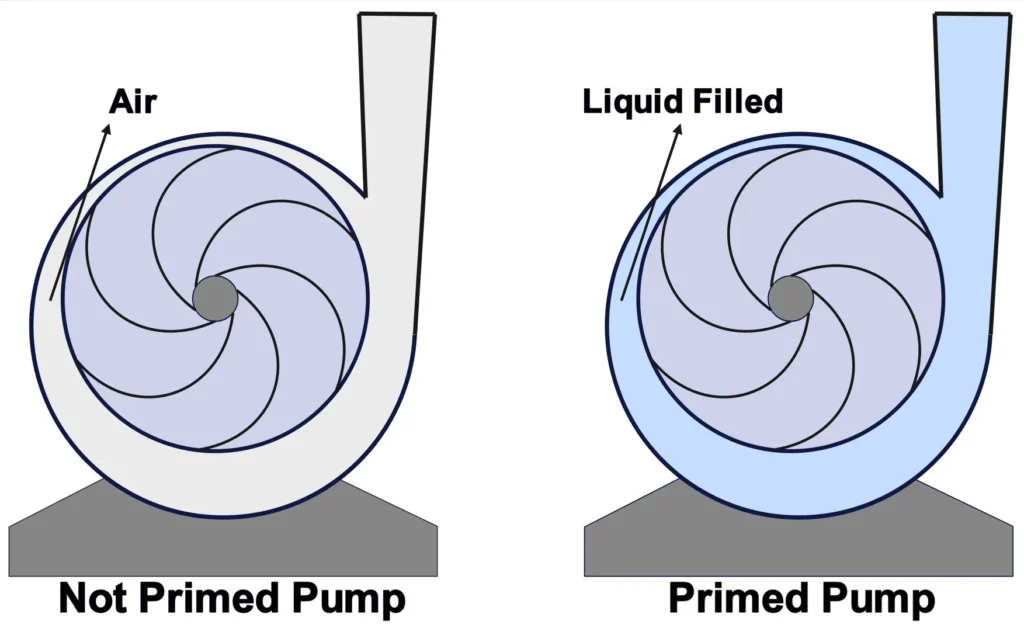
How to Prime a Pump
Priming methods vary based on the pump’s design and application. Here are the main approaches:
- Manual Priming: Fill the pump casing and suction line with liquid through a priming port or by backfilling from the discharge side. This is common in smaller systems but requires vigilance to prevent air re-entry.
- Self-Priming Pumps: These pumps are built to handle priming automatically. They use a reservoir or dual-volute design to recirculate liquid, expelling air until the system is fully primed. Ideal for applications like chemical transfer or mine dewatering.
- Vacuum-Assisted Priming: A vacuum pump or system removes air from the suction line, often used in large setups like sewage systems. Electrodes and solenoid valves prevent liquid carryover.
- Flooded Suction: Install the pump below the liquid source so gravity keeps the system filled, eliminating the need for manual priming.
- Foot Valves: A non-return valve at the suction line’s end retains liquid, preventing air ingress when the pump stops. Useful for long suction lines but can cause minor pressure losses.
Pro Tip: For long suction lines (hundreds of meters), a foot valve submerged in the liquid is essential for reliable priming.
Priming Challenges
Priming is not always straightforward. Long suction lines, leaks, or liquids with high vapor pressures (like volatile hydrocarbons) can complicate the process. If the suction line isn’t sealed, air leaks can disrupt priming, leading to vapor lock, where gas bubbles block flow. Always consult the pump’s manual for specific priming instructions to avoid issues.
What is Cavitation?
Cavitation is a sneaky problem that can quietly destroy your pump. Tiny bubbles forming in a liquid, then collapsing with enough force to chip away at metal. That’s cavitation in a pump. It occurs when the pressure in a pump drops below the liquid’s vapor pressure, causing the liquid to vaporize into bubbles. These bubbles implode in higher-pressure areas, unleashing shockwaves that damage components.
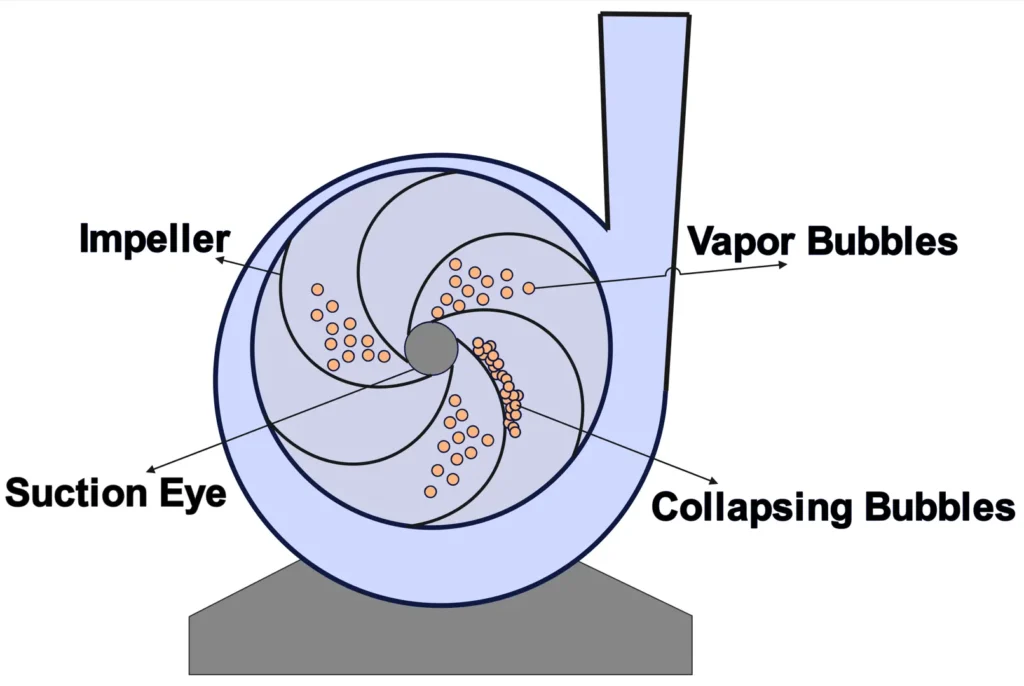
Why Cavitation Happens
Cavitation typically strikes at the pump’s suction side, where pressure is lowest, often near the impeller’s eye in centrifugal pumps or near valves in positive displacement pumps. Common causes include:
- Low Suction Pressure: High suction lift, restricted suction lines, or clogged filters reduce pressure at the pump inlet.
- High Fluid Temperature: Warmer liquids have higher vapor pressures, making them more prone to vaporizing.
- Excessive Flow Rates: Running a pump beyond its design capacity lowers pressure in critical areas.
- Improper Pump Selection: A pump with a high Net Positive Suction Head Required (NPSHr) may not suit a system with low Net Positive Suction Head Available (NPSHa).
- Operation Far from Best Efficiency Point (BEP): Operating outside 70-120% of BEP causes flow disruptions like recirculation, triggering cavitation.
The Dangers of Cavitation
Cavitation is not just a nuisance it’s a pump killer. Its effects include:
- Component Damage: Bubble implosions erode impellers, casings, and valves, causing pitting, cracks, or material loss. Water, with its high latent heat of vaporization, is especially destructive.
- Reduced Efficiency: Vapor bubbles disrupt flow, lowering head and flow rates.
- Noise and Vibration: Cavitation produces a “gravel-like” or “pinking” noise and excessive vibration, stressing bearings, seals, and pipework.
- Overheating: Prolonged cavitation can heat the liquid, risking seizures in tight-tolerance parts.
- System Downtime: Severe cavitation can lead to pump failure, halting critical processes.
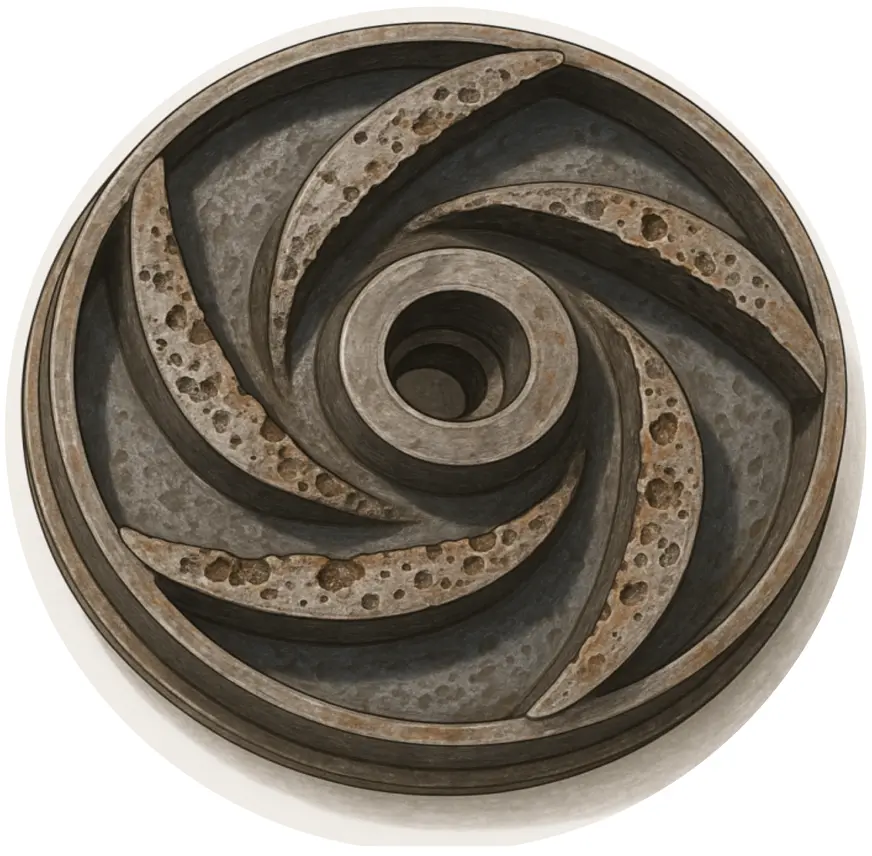
Types of Cavitation
Cavitation comes in different forms, each with unique triggers:
- Classical Cavitation: Caused by suction pressure dropping below the liquid’s vapor pressure, forming bubbles that collapse in high-pressure zones.
- Recirculation Cavitation: Occurs when a pump operates far from its BEP, creating eddy currents or flow reversal at the impeller’s inlet or outlet. This is like classical cavitation but stems from hydraulic inefficiencies.
Net Positive Suction Head (NPSH)
To keep cavitation away, you need to ensure the pump’s suction pressure stays above the liquid’s vapor pressure. That’s where Net Positive Suction Head (NPSH) comes in, an important factor for pump performance.
- NPSHa (Available): The actual pressure at the pump’s suction, based on system design, liquid properties, and flow conditions. It’s calculated considering:
- Static pressure at the liquid source.
- Elevation difference between the source and pump.
- Frictional losses in the suction line.
- Vapor pressure of the liquid.
- NPSHr (Required): The minimum pressure the pump needs to avoid cavitation, specified by the manufacturer. It increases with flow rate and can spike at low flows due to blade angle mismatches.
For cavitation-free operation, NPSHa must exceed NPSHr, ideally with a safety margin.
Effects of Dissolved and Entrained Gases
Liquids often carry dissolved or entrained gases (e.g., up to 10% air in lubricating oil or 20% in petrol), which amplify cavitation risks:
- Centrifugal Pumps: Gas reduces head and efficiency, destabilizing the head-flow (H-Q) curve. Air above 2-4% can cause loss of prime.
- Positive Displacement Pumps: Gases lower flow rates by occupying displacement volume and cause pressure pulsations, leading to vibration and component failure.
Preventing Cavitation and Ensuring Proper Priming
Here are practical steps to keep your pumps running smoothly:
- Select the Right Pump: Match the pump to your application. Axial flow pumps suit high-flow, low-head systems, while positive displacement pumps excel for consistent flow.
- Optimize Suction Design: Use short, large-diameter suction lines with minimal bends. Add pulsation dampers for reciprocating pumps to reduce acceleration head loss.
- Monitor NPSHa vs. NPSHr: Ensure NPSHa exceeds NPSHr with a safety margin. For high-suction energy pumps, aim for 2-20 times NPSHr.
- Prime Thoroughly: Use flooded suction or self-priming pumps where possible. Vent the system before startup to remove trapped air.
- Maintain Wear Rings: In low-specific-speed pumps, check wear ring clearances to prevent leakage-induced cavitation.
- Leverage Advanced Designs: Variable pitch vane pumps or double-suction impellers reduce cavitation by optimizing flow and lowering NPSHr.
- Collaborate with Manufacturers: Share detailed operating conditions (liquid properties, gas content, flow rates) to ensure the pump fits your system.
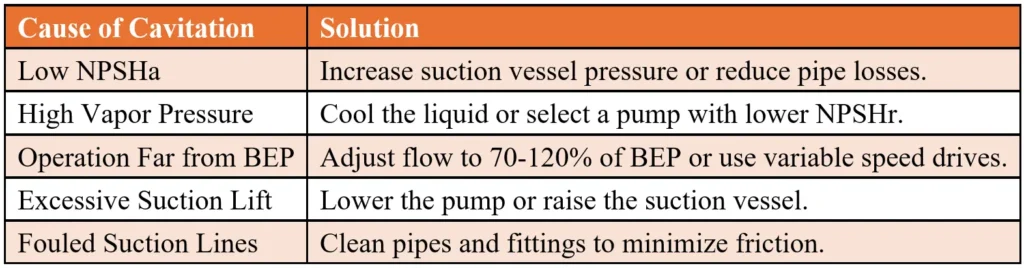
Difference between Pump Priming and Cavitation
To clarify the differences:

People Also Asked Questions with Answers
What happens if a pump is not primed?
Without priming, air in the pump or suction line prevents it from generating enough pressure to move fluid, leading to inefficiency, overheating, or failure to start.
How do you know if a pump is cavitating?
Look for a rattling or gravel-like noise, excessive vibration, reduced flow or head, and visible pitting or erosion on the impeller or casing.
Can cavitation be completely eliminated?
While cavitation can’t always be eradicated, it can be minimized by ensuring NPSHa exceeds NPSHr, optimizing suction design, and operating near the pump’s BEP.
Why is priming important for centrifugal pumps?
Priming fills the pump with liquid, enabling it to create suction and move fluid. Without it, the pump may run dry, risking cavitation or mechanical damage.
Top References:
- Nesbitt, B. (2006). Handbook of Pumps and Pumping: Pumping Manual International. Elsevier.
- Bloch, H. P., & Soares, C. (1998). Process Plant Machinery. Butterworth-Heinemann.
- Karassik, I. J., Messina, J. P., Cooper, P., & Heald, C. C. (2007). Pump Handbook. McGraw-Hill.
- Girdhar, P., & Moniz, O. (2004). Practical Centrifugal Pumps: Design, Operation and Maintenance. Elsevier.
- Lobanoff, V. S., & Ross, R. R. (1992). Centrifugal Pumps: Design and Application. Gulf Professional Publishing.
- https://armoloy.com
- https://www.northridgepumps.com