Block and bleed valves are vital for ensuring safety and efficiency in process industries like oil and gas, chemical manufacturing, and petrochemicals. By isolating equipment and releasing trapped pressure, they prevent chemical plant incidents and comply with safety protocols and regulations. Whether it’s a single block and bleed for low pressure systems or a double block and bleed for high-risk applications, these valves are essential for protecting workers and facilities. Understanding their types, applications, and maintenance needs is crucial for process safety engineers and industry professionals.
What is a Block and Bleed Valve?
A block and bleed valve is a specialized valve system designed to isolate process equipment and release trapped pressure, enabling safe maintenance in high-risk environments. It typically comprises one or more block valves to halt fluid flow and a bleed valve to vent residual pressure or fluid, preventing hazardous releases. These valves are essential for isolating process systems during maintenance, ensuring no unintended flow of flammable or toxic substances.
These valves are crucial in industries like oil and gas, chemical engineering, and petrochemical facilities to ensure equipment is safely isolated, reducing risks of chemical plant incidents.
Why Are Block and Bleed Valves Critical?
Block and bleed valves are the base of process safety management (PSM), protecting workers and facilities from industrial hazards. They are important in preventing catastrophic incidents by isolating equipment and controlling pressure. Key benefits include:
- Safe Isolation: Prevents unintended fluid releases during maintenance or emergency shutdowns.
- Risk Mitigation: Reduces the likelihood of fires, explosions, or chemical exposures.
- Regulatory Compliance: Meets standards like API 500, API RP 14J, and OSHA regulations.
- Operational Efficiency: Enables precise control over fluid systems, minimizing downtime.
Types of Block and Bleed Valves
Block and bleed valves come in various configurations, each for specific applications:
1. Single Block and Bleed Valve
- Consists of one block valve and one bleed valve in a single assembly.
- Suitable for low to medium pressure systems.
- Used in applications like sample collection points or chemical injection lines.
- Its simple and cost effective.
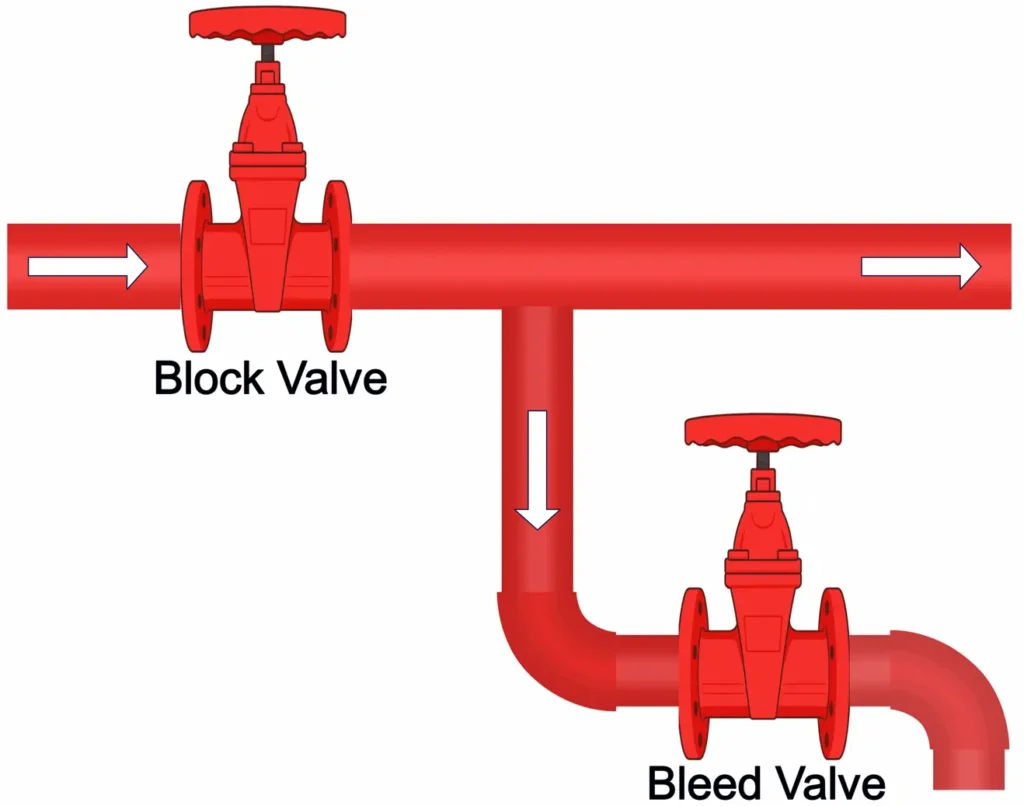
2. Double Block and Bleed Valve (DBB)
- Features two block valves and one bleed valve, providing enhanced isolation.
- Recommended for high pressure systems or sour services with high H2S content.
- Offers greater assurance of isolation, critical for high risk environments like refineries.
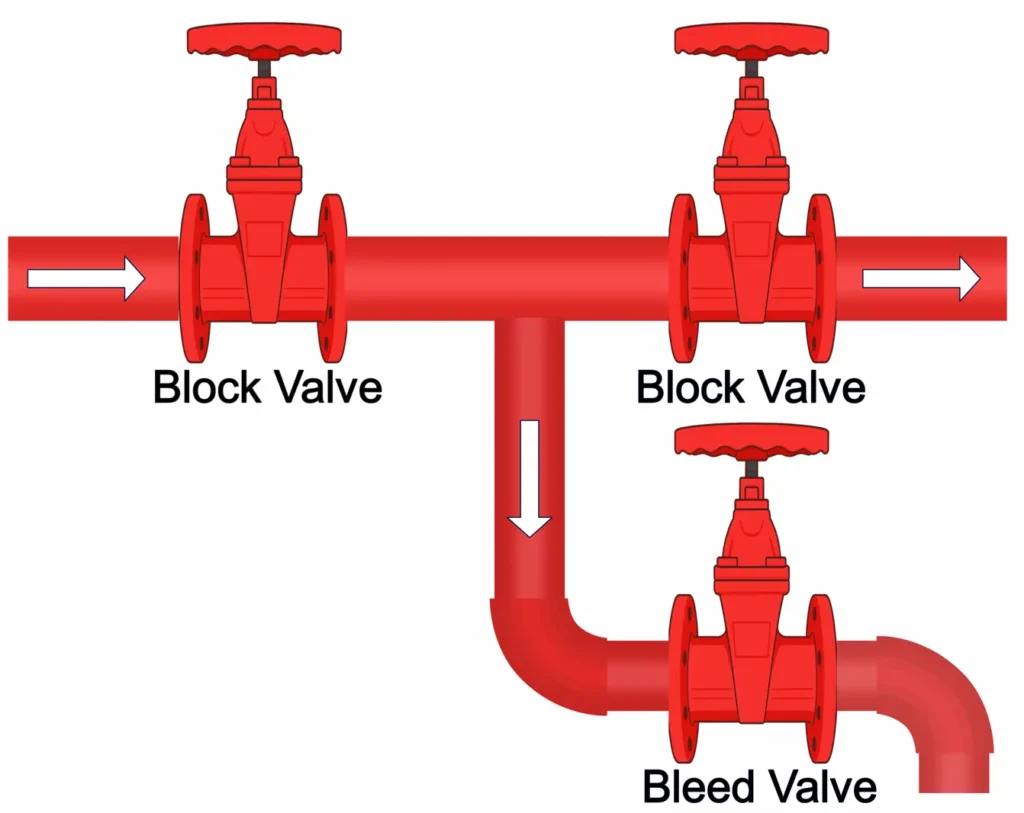
3. Single Unit Double Block and Bleed Valve
- Integrates two block valves and a bleed valve into a compact unit.
- Ideal for space-constrained areas like offshore platforms.
- Reduces installation complexity and piping weight, though maintenance can be more difficult.
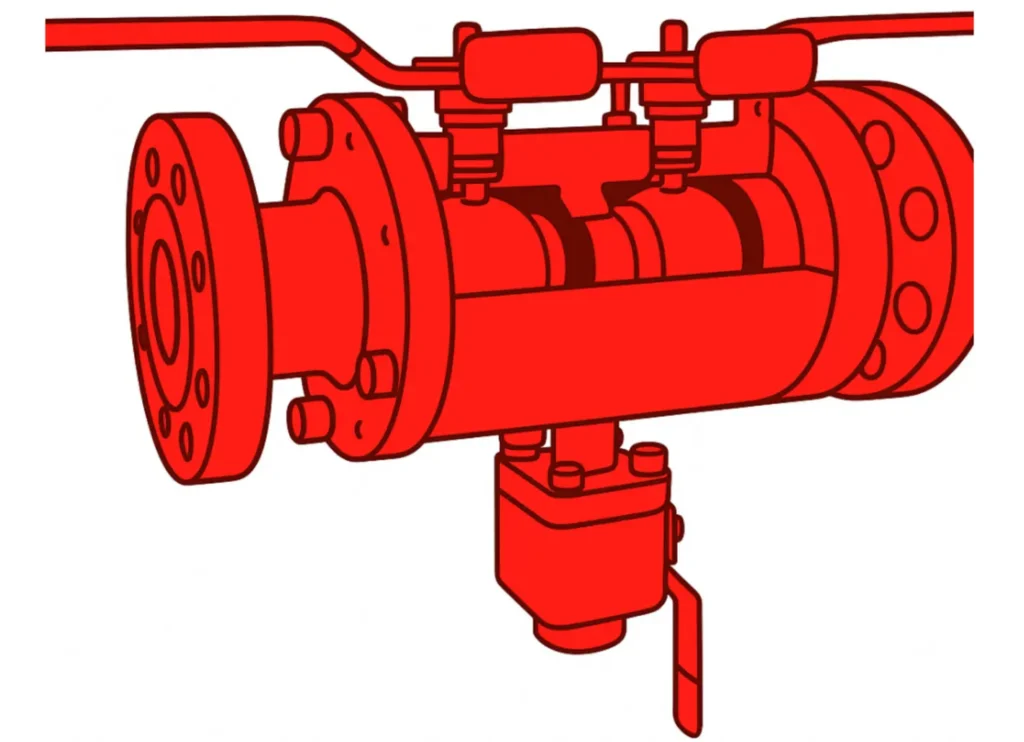
The choice of valve depends on factors like pressure rating, fluid corrosivity, and space constraints.
How Block and Bleed Valves Work
The operation of a block and bleed valve is simple yet critical for safety:
- Isolation: The block valves are closed to stop fluid flow from the upstream process, isolating the downstream equipment.
- Pressure Release: The bleed valve is opened to vent trapped pressure or fluid, ensuring the isolated section is depressurized.
- Verification: Operators confirm zero pressure in the system using gauges or visual checks before maintenance begins.
This process is vital during turnaround activities, where equipment like heat exchangers or pumps must be isolated. Improper isolation can lead to major incidents, such as hydrocarbon leaks.
What is the function of the bleed valve?
The bleed valve in a block and bleed system releases trapped pressure or fluid from the isolated section of a piping system, ensuring safety. It allows to vent hazardous substances, like flammable hydrocarbons, preventing risks like explosions or chemical exposure. This function is critical in high pressure environments like refineries to comply with safety standards by confirming depressurization.
Applications in Process Industries
Block and bleed valves are widely used across process industries:
- Petroleum Refineries: Isolate piping systems during maintenance of crude distillation units, vacuum towers, or fluidized catalytic crackers etc. They prevent leaks of flammable hydrocarbons, reducing fire risks.
- Chemical Plants: Handle reactive or corrosive substances like phenols, amines, or acids, ensuring safe isolation during emergency shutdowns.
- Offshore Platforms: Compact single-unit DBB valves are used in confined spaces for isolating high pressure systems handling LNG or LPG.
- Instrumentation and Sampling: Used in sample lines or chemical injection systems to safely collect samples or inject chemicals without exposing workers to hazards.
DBB valves are mandatory for systems handling toxic or flammable fluids, ensuring compliance with safety protocols.
Block and Bleed Valves Selection Criteria
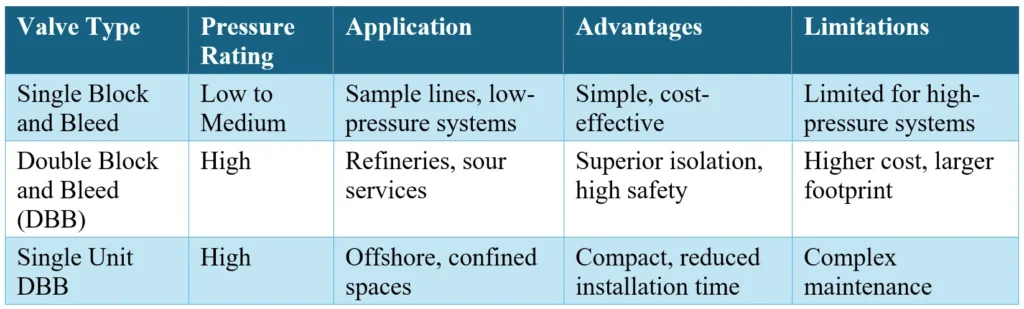
Process Safety and Block and Bleed Valves
Block and bleed valves are critical for preventing chemical plant incidents. They are integral to process safety management (PSM), ensuring safe isolation during maintenance or emergency shutdowns. These valves are essential for compliance with regulations, particularly in refineries handling high pressure hydrocarbons or toxic substances.
Case Study: 2015 Refinery Incident
A 2015 incident investigated by the US Chemical Safety Board involved a hydrocarbon release due to improper isolation during maintenance, leading to a fire. The investigation found that a single block and bleed valve was used in a high-pressure system, which failed to provide adequate isolation. The report recommended double block and bleed valves for such applications, highlighting their role in preventing major incidents.
Quantitative Data: Incident Reduction
Double block and bleed valves in high pressure systems reported a 30% reduction in isolation-related incidents compared to those using single block and bleed valves. This underscores that the enhanced safety provided by DBB systems in critical applications.
Standards and Guidelines
Several standards govern the design and use of block and bleed valves, ensuring compliance with safety protocols:
- API 500: Provides guidelines for classifying hazardous locations and selecting valves for petroleum facilities, emphasizing block and bleed valves for high-risk areas.
- API RP 14J: Recommends block and bleed valve systems for high-pressure applications.
- PSM Regulations: Mandate block and bleed systems for safe equipment isolation.
- API 598: Specifies testing requirements for valve integrity, ensuring reliability in high pressure or corrosive services.
These standards ensure that block and bleed valves meet rigorous safety and performance criteria, minimizing industrial hazards.
Challenges and Best Practices
Despite their benefits, block and bleed valves face some challenges:
- Corrosion and Plugging: In crude oil or sour service, valves can corrode or become plugged with debris, compromising performance.
- Improper Selection: Using single block and bleed valves in high pressure or toxic systems can lead to safety failures.
- Maintenance Costs: DBB valves, while safer, are more expensive and require skilled maintenance.
Best Practices
- Material Selection: Use corrosion resistant materials like stainless steel for sour services.
- Regular Inspections: Conduct periodic checks for corrosion, blockages, or seat wear.
- Operator Training: Ensure personnel are trained in valve operation and HAZOP analysis, aligning with OSHA requirements.
- Process Hazard Analysis (PHA): Incorporate block and bleed valves into PHAs to identify risks.
- Documentation: Maintain detailed records of valve maintenance and testing, as required by PSM regulations.
References
- Nolan, D. P. (2019). Handbook of Fire and Explosion Protection Engineering Principles for Oil, Gas, Chemical, and Related Facilities. Elsevier.
- Coker, A. K. (2021). Petroleum Refining Design and Applications Handbook, Volume 3. Wiley-Scrivener.
- Petroleum Engineering Handbook, Volume III: Facilities and Construction Engineering. (2006). Society of Petroleum Engineers.
- Fundamentals of Petroleum Refining. (2010). Elsevier.
- Nelson, W. L. (1949). Petroleum Refinery Engineering. McGraw-Hill Book Co.
- https://pecm.co.uk
- https://www.sciencedirect.com