The physical process of mixing two or more petroleum products with different properties to produce a homogeneous finished product with desired characteristics is called blending in petroleum refinery. The main objective of products blending is to find the best way of mixing different intermediate products available from the refinery and some additives in order to adjust the product specifications and avoiding product quality giveaway and improve the refinery margin. For example, diesel oil blend is produced by a number of components that include straight run, hydrotreating, hydrocracking diesel stream, and treated kerosene. Lubricity chemical is also added to improve the lubricity property of diesel products.
Online analyzers are available to continuously analyze the quality specifications but the final quality of the finished products is always checked by laboratory tests before market distribution. Gasoline is tested for sulfur, octane number, Reid vapor pressure (RVP), and volatility. Kerosene is tested for flashpoint, conductivity, sulfur, color, and volatility. Gas oils are tested for diesel index, flash point, pour point, sulfur, and distillation.
Petroleum Products Blending Methods
Blending methods normally employed include batch blending and continuous in-line blending.
1. Batch Type Blending or Tank Blending
In batch mixing or In-tank blending, the known blending streams are added together in the storage tank. The materials are then mixed together using agitators for a predetermined time until the homogenous product of desired specifications is obtained. Tanks may also be equipped with temperature, pressure, and level instruments.
The components from individual process units are sent to run-down or base-stock tanks. The specifications of each component are determined from lab analysis to quantify the share for the final blend. Each component stream is next pumped separately from base run-down storage tanks into a blending tank. Additives are then added and mixed thoroughly. After laboratory analysis, the blended product is pumped for shipping.
Batch-wise blending is not preferred because of the high cost of blending stocks and the requirement of various resources. The resources may include mixtures, steam coils heating system, cooling system, pumps, storage tanks, and instrumentation
Fig.01 below shows the general description of Batch Type Mixing.
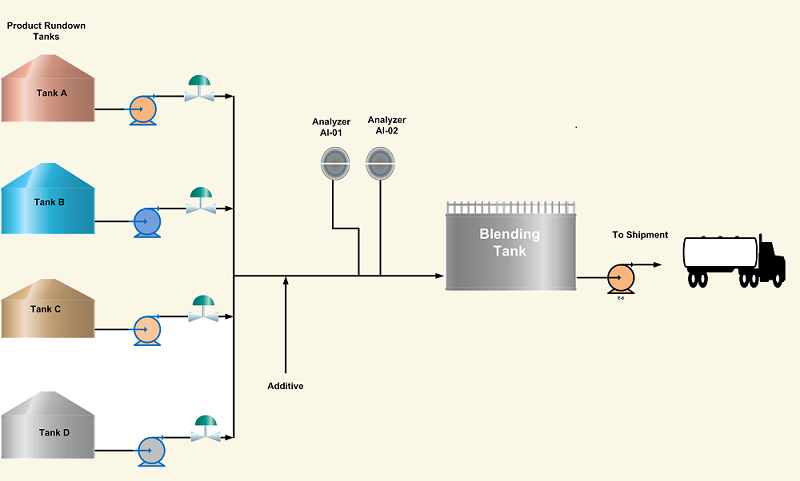
2. Continuous In-line Blending
This process also called line blending is widely used in petroleum refineries. All the blending components are pumped to a common header at specified rates or the units run down rates. Flow rates of the streams are adjusted according to the blending recipe or product specifications by using control valves. The long pipe or header acts as a mixer and sometimes static mixers are also installed on the header. The common header may also be equipped with an online analyzer showing the main blending property. For diesel oil blending, sulfur and flashpoints analyzer may be applied and similarly, for gasoline online RON, sulfur analyzers can be applied.
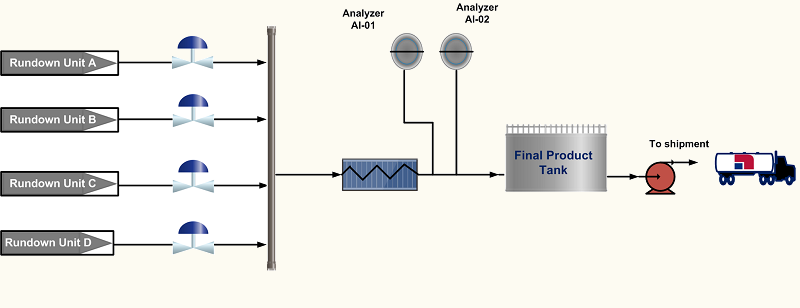
Continuous in-line blending is preferred because of continuous production of the blend, product in-spec throughout the entire blending process, rapid availability of the product, less storage of the products in a plant, less investment on storage tanks and mixing accessories, all tanks designated to final products, reduction of costly giveaways and time-saving for blend preparations.
Batch mixing blending has the advantage of the flexibility of flow streams variation during the blending. Flow rates of components can be adjusted according to the requirement because of the source tanks. On the other side, during online continuous blending, stream flows are coming directly from the plants at constant rates. For example, for diesel oil blending, the major streams are hydrotreating and hydrocracking diesel, so adjusting their streams means production loss. So, their quality parameters are adjusted continuously based on online analyzers and lab results in order to meet the desired blending specifications.
Predictions of the Specified Properties of Petroleum Products
Perhaps the most difficult phase of the petroleum products blending process is to predict the properties of the final product. In oil refineries, various mixing rules and correlations are employed to approximate the blend characteristics such as specific gravity, RVP, viscosity, flash point, pour point, cloud point, octane number, and aniline point. Some properties that are linear or additive include specific gravity, boiling point, and sulfur content. However, properties like viscosity, flash temperature, pour point, aniline point, RVP, and cloud point are not linear.
- Process Engineers can calculate and estimate the specific linear and non-linear properties using the correlation given in the books, 1. Fundamentals of Petroleum Refining by M.A Fahim, T.A Alsahaf, A.S Elkelani, 2. Refining Process Handbook by Surinder Parkash and 3. Petroleum Refining Technology and Economics James H. Gary, Glenn Handwerk.
- Another method used by most of the refineries is the computer-controlled in-line blending for blending gasoline and other high-volume products. Inventories of blending components, together with cost and physical property data are maintained in the computer. When a certain volume of a given quality product is specified, the computer uses linear programming models to optimize the blending operations to select the blending components to produce the required volume of the specified product at the lowest cost. Both linear and geometric programming techniques are used by computer-based programs.
- Various companies provide the latest computer-based blending systems solutions the include; Refinery Blending by Aspentech, Blending Optimization System by Yokogawa, Blending Systems by Emerson, Blending solutions by Modcon, and many more.
- Manual blending using operating experience. The properties of the blending products are estimated using lab analysis, online analyzers, and components properties; flow rates of blending streams are adjusted accordingly. For example in the fuel oil blending, the low viscosity of fuel oil is controlled by increasing the flows of components having high viscosity.
For further discussion please comment or ask at admin@thepetrosolutions.com